Understanding Sand Casting Examples and Applications
Sand casting, one of the oldest and most widely used metal casting processes, involves pouring molten metal into a sand mold to create intricate shapes and components. Its versatility and cost-effectiveness make it a popular choice across various industries, including automotive, aerospace, construction, and consumer goods. This article explores some of the diverse products created through sand casting, illustrating its significance and application in today’s manufacturing landscape.
1. Automotive Components
The automotive industry is one of the largest users of sand casting techniques. Various parts, such as engine blocks, cylinder heads, and transmission housings, are produced using this method. For instance, engine blocks made from aluminum sand castings are favored for their lightweight properties, contributing to improved fuel efficiency. The intricate designs that can be achieved with sand casting also allow for the integration of features like coolant passages, making the engine more efficient and effective.
Another example is the production of cast iron brake rotors. These components require excellent thermal properties and durability, both of which are enhanced by the sand casting process. The ability to produce large volumes of these components at relatively low cost further cements sand casting's role in the automotive sector.
2. Aerospace Components
In the aerospace industry, where safety and precision are paramount, sand casting is utilized to create lightweight and strong components. Turbine housings, brackets, and landing gear parts are just a few examples of components produced using this casting method. For instance, the manufacturing of turbine blades often employs advanced sand casting techniques to ensure high-quality and performance over extreme environments.
These components often undergo rigorous testing to meet stringent safety standards. Innovative sand casting methods, such as the use of lost foam casting, help in achieving complex geometries that are vital for performance-sensitive applications in aircraft engines.
Sand casting is also extensively used in producing industrial equipment. Components such as pump housings, valve bodies, and gear cases are commonly made using this method. These products often require a high degree of durability and resistance to wear, which can be achieved through the appropriate selection of alloys and casting techniques.
examples of sand casting products
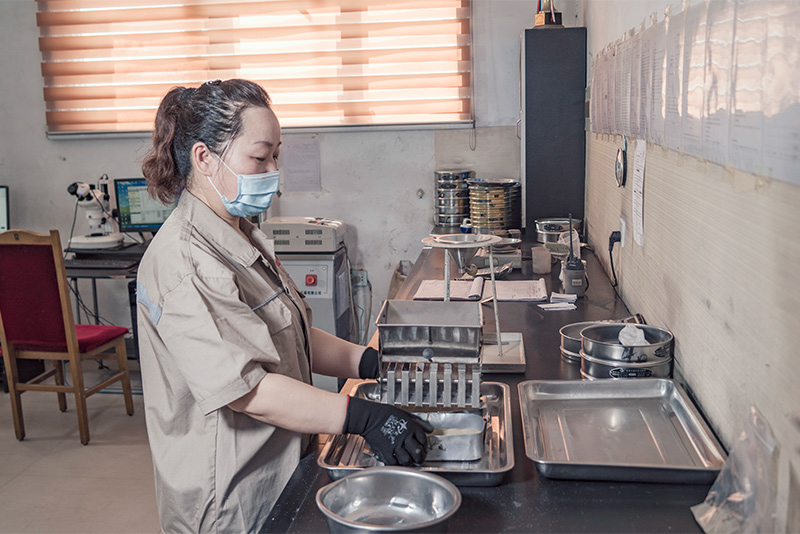
Pump housings, for example, are often made from gray iron or ductile iron for their excellent strength and corrosion resistance. The ability to produce these components in large quantities with consistent quality is a significant advantage of sand casting, catering to the demands of various industrial sectors.
4. Artistic and Architectural Applications
Beyond industrial applications, sand casting also finds a niche in the artistic and architectural realm. Sculptures, decorative pieces, and architectural elements such as balusters and decorative grilles are created using sand casting. Artists appreciate the versatility of sand casting, which allows for both intricate designs and a variety of finishes, from the rustic look of cast iron to the sleek appearance of aluminum and bronze.
For example, many public monuments and sculptures are created using sand casting techniques, allowing for both artistic expression and durability against the elements. The customizability of sand casting enables artists to push the boundaries of traditional sculpture, leading to unique installations that can withstand the test of time.
5. Consumer Goods
In everyday life, sand casting produces a wide array of consumer goods. Cooking utensils, such as skillets and pots, are often made from cast iron, favored for its heat retention and cooking properties. The classic cast iron skillet remains a staple in many kitchens, showcasing how sand casting translates into functional, high-quality consumer products.
Moreover, garden ornaments and furniture cast from aluminum or iron benefit from the durability and aesthetic appeal that sand casting provides. The potential for intricate designs and various finishes means that these products not only serve functional purposes but also enhance the visual environments in which they are placed.
Conclusion
Sand casting remains a fundamental and invaluable manufacturing process across numerous industries. Its ability to produce complex shapes and large components at a relatively low cost ensures its continued relevance. From heavy-duty automotive parts to artistic sculptures, the versatility of sand casting demonstrates its essential role in modern manufacturing and design. As technology advances, the potential applications and improvements in sand casting techniques will likely expand, further solidifying its importance in various fields.
Post time:Gru . 19, 2024 10:57
Next:sand cast industries