The Sand Casting Process An Overview
Sand casting, also known as sand molded casting, is one of the oldest and most versatile metal casting processes. It is extensively used for producing complex parts in various shapes and sizes across multiple industries, including automotive, aerospace, and artistic applications. The process is valued for its low cost, ease of setup, and adaptability to various alloy types.
The Basics of Sand Casting
At its core, sand casting involves creating a mold out of sand that serves as a cavity into which molten metal is poured
. The fundamental steps in the sand casting process include pattern making, mold preparation, pouring the metal, and finishing the cast part.1. Pattern Making The first step in the sand casting process involves creating a pattern, which is a replica of the final product. Patterns are typically made from materials like wood, metal, or plastic, and they are designed to be slightly larger than the final part to accommodate for metal shrinkage during cooling.
2. Mold Preparation Once the pattern is ready, the next step is to create the mold. This is done by compacting sand around the pattern to form a mold cavity. The sand used is often a mixture of silica sand, clay, and moisture to enhance its binding properties. The key is to achieve a consistency that allows the sand to maintain its shape while also being easy to remove after casting. The mold can be either a single piece (a single pattern) or a two-piece mold (a split pattern).
3. Metal Pouring After the mold is prepared, it is subjected to a quality check, and then molten metal is poured into the mold cavity. The temperature and composition of the molten metal are critical to ensuring the quality of the casting. Common metals used in sand casting include aluminum, iron, and bronze.
4. Cooling and Solidification Once the metal is poured, it is allowed to cool and solidify. The cooling time depends on the size and thickness of the casting. After the metal has cooled sufficiently, the mold is broken away, revealing the cast part.
describe sand casting process
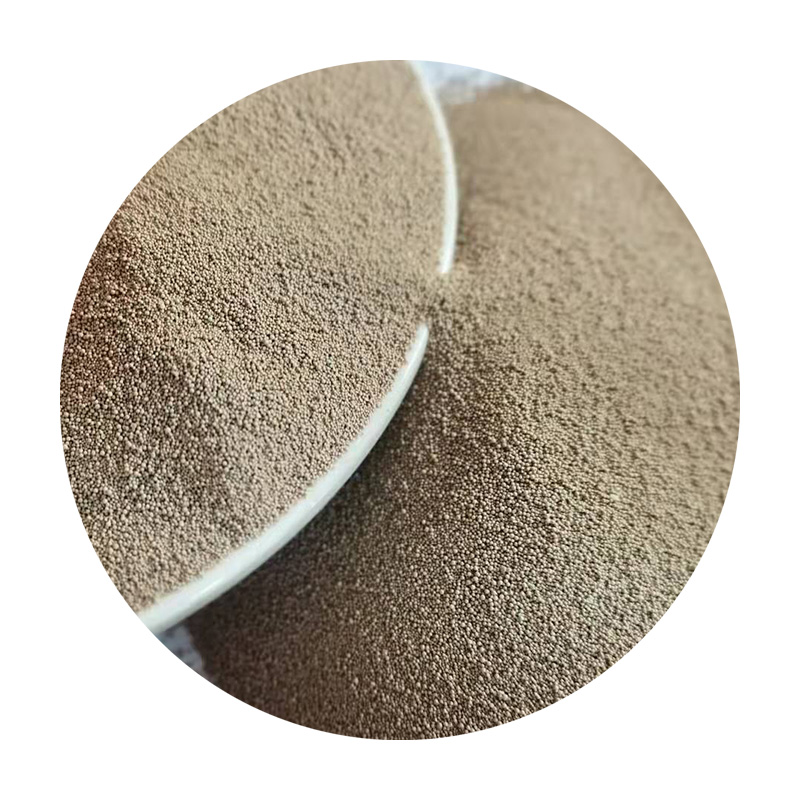
5. Finishing Touches The final step involves finishing the cast component, which may include processes such as cleaning, machining, or polishing. The goal is to achieve the desired surface finish and dimensional accuracy.
Advantages of Sand Casting
The sand casting process offers several advantages. Firstly, it is highly adaptable, allowing for the casting of complex shapes that are difficult to manufacture through other methods. Secondly, the materials required for sand casting are readily available and cost-effective, making it accessible for both small and large-scale productions. Additionally, sand molds can be reused, further reducing costs.
Applications of Sand Casting
Sand casting is used in various applications, from producing engine blocks and cylinder heads in the automotive industry to creating artistic sculptures in foundries. Its versatility makes it a preferred choice for both mass production and one-off custom pieces.
Conclusion
In summary, sand casting stands as a crucial process in the metalworking industry. Its affordability, versatility, and capability to produce intricate designs make it an invaluable method for manufacturers worldwide. As technology advances, the sand casting process continues to evolve, incorporating innovations that enhance efficiency and quality, securing its place as a timeless technique in metal casting.
Post time:Rgs . 24, 2024 15:41
Next:Versatile Applications of Cerabeads in Sand Industry for Enhanced Performance and Efficiency