Custom Sand Casting A Versatile Manufacturing Process
Custom sand casting is an age-old manufacturing process that has stood the test of time, continually evolving to meet the demands of modern industries. This method is renowned for its flexibility and ability to produce complex shapes that would be challenging to achieve through other manufacturing processes. It involves pouring molten metal into a sand mold that has been shaped to form the desired object, making it a popular choice for creating custom parts across various applications.
At its core, sand casting begins with the creation of a pattern that reflects the final product's dimensions and details. This pattern is usually made from a durable material such as metal or plastic, and its design incorporates allowances for shrinkage and finishing. Once the pattern is ready, it is used to create a sand mold. The mold is made by mixing sand with a binding agent, typically clay, and then pressing or packing it around the pattern. The result is a mold cavity that closely mimics the shape of the intended casting.
One of the significant advantages of custom sand casting is its ability to produce large and intricate components
. This technique can accommodate a wide range of materials, including iron, aluminum, bronze, and magnesium alloys, making it suitable for diverse industries such as automotive, aerospace, and machinery manufacturing. Whether it’s engine blocks, gears, or artistic sculptures, custom sand casting can deliver high precision and durability.Customization is at the heart of the sand casting process. Each project can be tailored to meet specific requirements concerning size, weight, complexity, and material properties. This adaptability allows manufacturers to respond quickly to unique customer needs. For instance, in the aerospace industry, lightweight components can be crafted using aluminum sand casting to enhance fuel efficiency without compromising strength.
custom sand casting
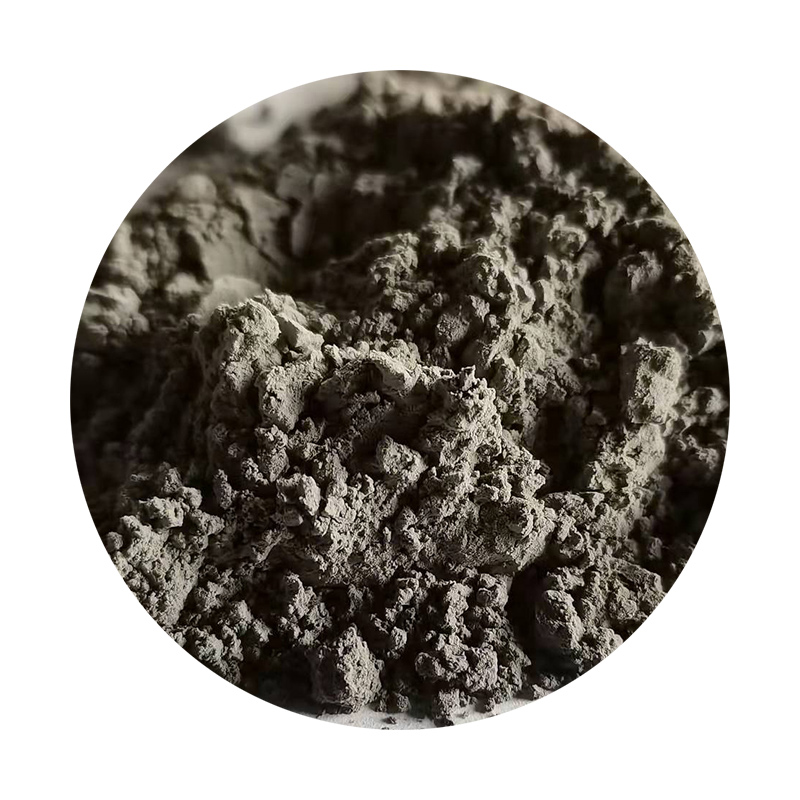
The process also provides an opportunity for intricate detailing and surface finishing. Once the castings are removed from the mold, they can undergo various finishing processes, such as grinding, machining, and polishing, to achieve the desired surface quality. This flexibility enables manufacturers to deliver products that meet rigorous standards and specifications.
Moreover, custom sand casting is often more cost-effective for low to medium production runs compared to more advanced methods like die casting. The initial investment for creating the sand molds is relatively low, making it an attractive option for startups and small businesses looking to prototype or produce parts.
However, there are challenges associated with sand casting. Variability in sand quality, moisture content, and mold-making techniques can lead to inconsistencies in the final product. Therefore, it is crucial for manufacturers to have stringent quality control measures in place to ensure that each casting meets the required standards.
In conclusion, custom sand casting remains a highly relevant and valuable manufacturing process in today’s industrial landscape. Its ability to produce intricate, durable parts tailored to specific needs, combined with its cost efficiency for smaller production runs, makes it a preferred choice for many businesses. As technology continues to advance, the sand casting process is likely to become even more refined, opening new possibilities for innovation and creativity in the world of manufacturing.
Post time:Rgs . 23, 2024 06:56
Next:sand casting advantages