Application of Sand Casting Process
Sand casting is one of the oldest and most widely used metal casting processes. This technique involves creating a mold from sand, which is then used to form metal parts through the pouring of molten metal into the cavity created by the mold. Its versatility and cost-effectiveness make it a popular choice in various industries, particularly in automotive, aerospace, and manufacturing sectors.
1. Historical Context and Development
The sand casting process dates back thousands of years, with evidence of its use in ancient Egypt and China. Over the centuries, the technique has evolved significantly, incorporating advancements in technology and materials. Despite these changes, the fundamental principle remains the same using sand to create a mold that can withstand the heat of molten metal.
2. Materials Used in Sand Casting
The primary material in sand casting is, unsurprisingly, sand. Typically, silica sand is used due to its desirable properties, such as high melting point and good flowability. Various binders, such as clay and resin, are mixed with the sand to hold the grains together and form a stable mold. The type of sand and binder used can significantly affect the quality of the final cast product, influencing factors like durability, surface finish, and dimensional accuracy.
3. Process Overview
The sand casting process begins with the production of a pattern, which is a replica of the final product. This pattern is often made of metal, plastic, or wood, and is then placed in a molding box filled with sand. The sand is compacted around the pattern, and once removed, it leaves an impression that serves as the mold.
application of sand casting process
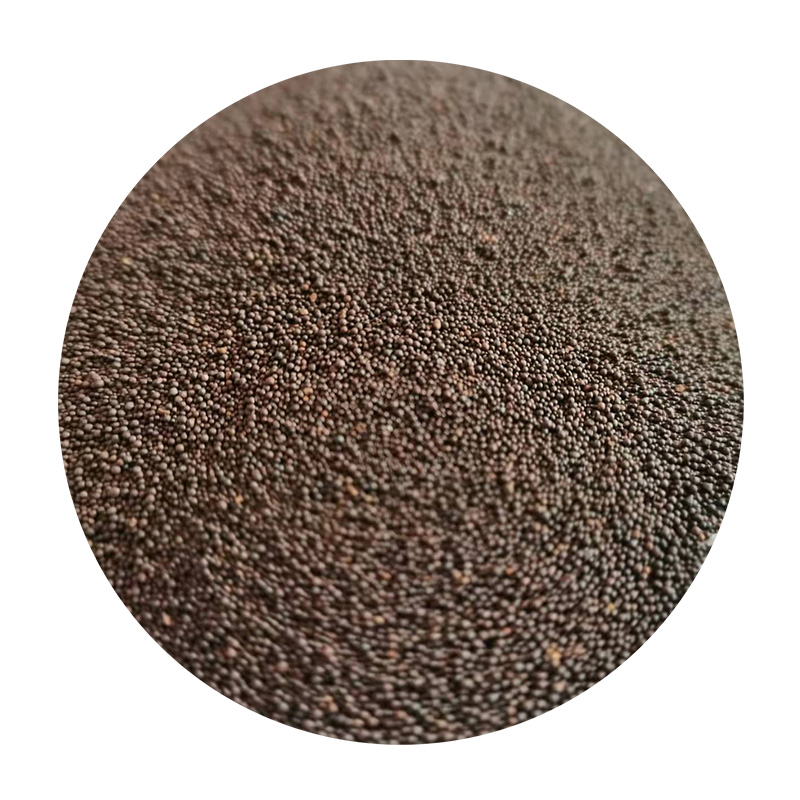
After the mold is prepared, molten metal, usually aluminum, iron, or bronze, is poured into the cavity. The metal fills the mold and, upon cooling, takes the shape of the pattern. After sufficient cooling, the sand mold is broken apart to reveal the cast part, which may require additional finishing processes like machining or painting to meet the desired specifications.
4. Advantages of Sand Casting
One of the main advantages of sand casting is its ability to produce complex shapes with minimal tooling. This feature allows manufacturers to create intricate designs that would be difficult or impossible to achieve with other casting methods. Additionally, sand casting is highly adaptable; it can be used for large production runs or smaller, custom orders.
Cost is another significant benefit. The materials required for sand casting are relatively inexpensive, and the process itself can be performed using basic equipment. This low barrier to entry makes sand casting an attractive option for startups and small manufacturers looking to minimize expenses.
5. Applications in Industry
Sand casting is prevalent in various industries. In the automotive sector, it is used to produce engine blocks, gearbox cases, and other critical components. Aerospace applications often involve creating parts that must withstand extreme conditions, requiring the precision and reliability that sand casting can offer. The manufacturing industry frequently employs sand casting for producing machine bases, housings, and other structural components.
In conclusion, sand casting remains an essential and practical manufacturing process due to its versatility, cost-effectiveness, and ability to produce complex shapes. As industries continue to evolve, the application of sand casting is likely to expand, reinforcing its significance in modern manufacturing practices.
Post time:Lap . 20, 2024 05:42
Next:should you sand 3d prints