Application of Sand Casting Process
Sand casting, one of the oldest and most widely used metal casting processes, plays a critical role in various industries due to its versatility and cost-effectiveness. This process involves creating a mold from sand to shape the molten metal into desired forms. Its applications span across numerous sectors, including automotive, aerospace, and industrial machinery, making it an essential technique in manufacturing.
Historical Background
The origins of sand casting can be traced back thousands of years, with evidence of its use in ancient civilizations such as Egypt and Mesopotamia. As technology evolved, so did the processes and materials used in sand casting. Today, the techniques have been refined to improve efficiency, precision, and quality, making sand casting an integral part of modern manufacturing.
Understanding the Sand Casting Process
The sand casting process consists of several key steps. It begins with pattern creation, where a replica of the desired object is made, typically from metal or plastic. This pattern is then embedded in a mixture of sand and binder material to create a mold. Once the mold is prepared, it is subjected to compaction to ensure strength and stability. After removing the pattern, molten metal is poured into the mold cavity. Once the metal cools and solidifies, the mold is broken apart to reveal the finished casting.
One of the advantages of sand casting is its adaptability to various shapes and sizes. The mold can be easily modified, making it suitable for both small batches and large production runs. Additionally, the process is capable of producing complex geometries that would be challenging to achieve with other casting methods.
Applications in Various Industries
1. Automotive Industry The automotive sector extensively utilizes sand casting for producing engine blocks, cylinder heads, and other critical components. The ability to cast intricate designs with strong materials allows manufacturers to enhance performance while reducing weight. Sand casting is especially valuable for developing prototype parts, enabling rapid iteration and testing.
2. Aerospace Industry In aerospace applications, where precision and reliability are paramount, sand casting provides a means to manufacture lightweight yet strong components such as turbine housings and structural elements. Various alloys can be cast to meet specific performance criteria, ensuring safety and efficiency in flight.
application of sand casting process
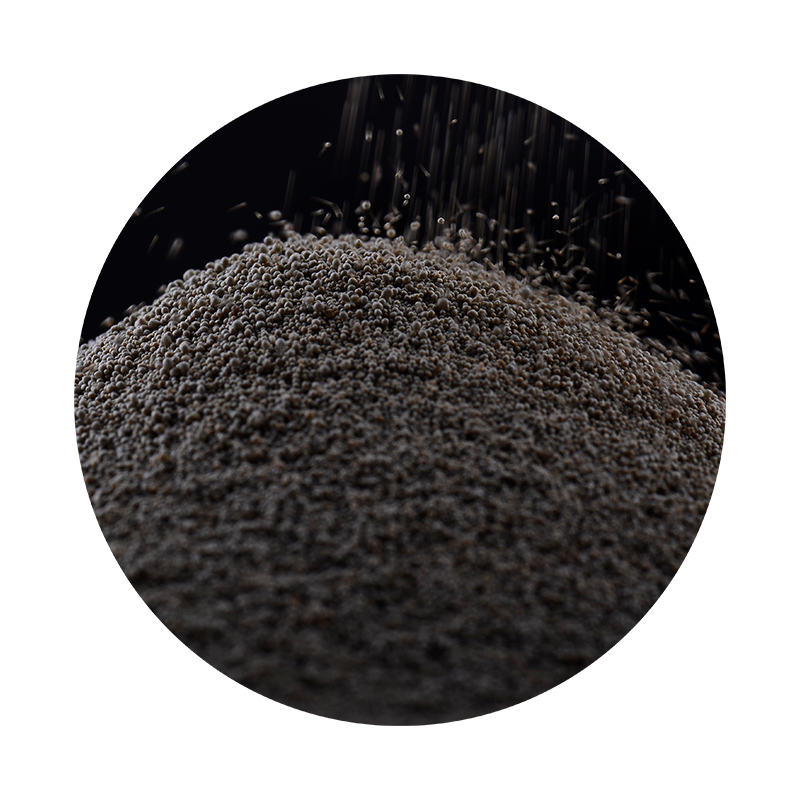
3. Industrial Machinery Sand casting is fundamental in fabricating components for industrial machines, including pumps, valves, and gearboxes. These parts often require high durability and resistance to wear, which sand casting can provide through the use of appropriate materials and treatments.
4. Art and Sculpture Beyond industrial applications, sand casting is also employed in the artistic domain for creating sculptures and decorative elements. Artists can leverage the flexibility of sand molds to produce unique designs that capture intricate details.
Advantages of Sand Casting
The sand casting process boasts numerous advantages that make it a popular choice among manufacturers. One of the most significant benefits is its cost-effectiveness; the materials used for sand casting are relatively inexpensive, and the process is efficient for both large and small production runs. Furthermore, sand molds can be reused multiple times, which reduces material waste.
Another key advantage is the ability to cast a wide variety of metals, including ferrous and non-ferrous alloys. This versatility allows manufacturers to select the most suitable material for their specific needs. Additionally, the sand casting process can accommodate large parts, which can be a challenge for other casting techniques.
Challenges and Future Trends
Despite its many advantages, sand casting also faces challenges, such as a lower surface finish compared to more advanced casting methods, which may require additional machining. Additionally, consistency in wall thickness and dimensional precision can be more difficult to achieve.
Looking toward the future, sand casting is likely to evolve with advancements in technology. Innovations such as 3D printing of sand molds and the use of automated processes promise to enhance efficiency and precision. Furthermore, as industries increasingly prioritize sustainability, the development of eco-friendly sand binders and recycling methods will broaden the application of sand casting while minimizing environmental impact.
Conclusion
In conclusion, sand casting remains a vital and versatile manufacturing process with a broad range of applications across various industries. Its cost-effectiveness, adaptability, and capacity for producing complex shapes make it an invaluable method for creating metal components. As technology progresses, sand casting is poised to evolve further, ensuring its relevance in the ever-changing landscape of manufacturing.
Post time:Spa . 13, 2024 06:20
Next:sand casting components