Advantages and Disadvantages of the Sand Casting Process
Sand casting, one of the oldest and most versatile metal casting processes, has been widely utilized in various industries for producing metal parts. This process involves creating a mold from a sand mixture, into which molten metal is poured to solidify and form the desired shape. While sand casting has numerous advantages, it also comes with its share of disadvantages. Understanding both aspects is crucial for evaluating its suitability for specific applications.
Advantages of Sand Casting
1. Cost-Effective for Low-Volume Production One of the significant advantages of sand casting is its cost-effectiveness, especially for small to medium production volumes. The tooling required for sand casting, such as patterns and molds, is relatively inexpensive compared to processes like die casting, which requires high up-front costs for tooling. This makes sand casting an attractive option for prototypes and short runs.
2. Versatility in Material Use Sand casting is compatible with a wide variety of metals, including aluminum, brass, bronze, iron, and steel. This versatility allows manufacturers to tailor their casting processes according to specific material properties required for different applications, giving them the flexibility needed for diverse projects.
3. Ability to Produce Large Parts The sand casting process is particularly suited for creating large and complex shapes that would be challenging to achieve through other methods. The size and weight of the mold can be adapted easily without significant changes to the production process, making it ideal for industries such as aerospace, automotive, and heavy machinery, where large components are commonplace.
4. Excellent Dimensional Tolerances Although the surface finish of sand castings may not be as fine as that from other casting methods, the process can still achieve good dimensional tolerances. With precise control over the mold-making process and careful consideration of shrinkage during cooling, manufacturers can produce parts that closely match required specifications.
5. Environmental Considerations Many sand casting operations utilize recyclable materials, such as reclaimed sand. This not only reduces waste but also lowers the overall environmental impact of the casting process. The use of eco-friendly binders further enhances its sustainability profile.
advantages and disadvantages of sand casting process
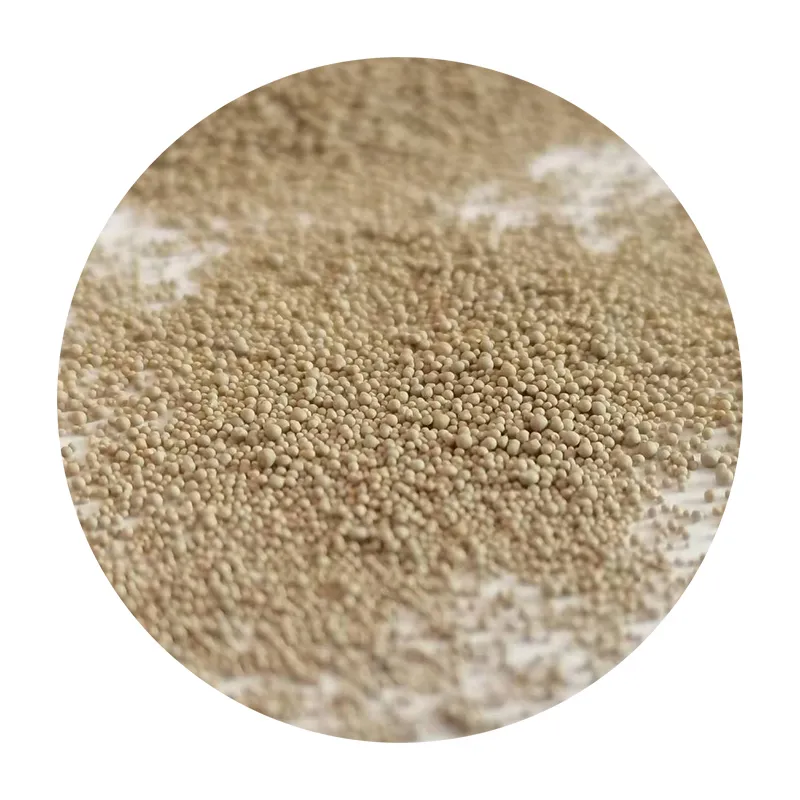
Disadvantages of Sand Casting
1. Lower Surface Finish Quality One of the most notable drawbacks of sand casting is the relatively rough surface finish it produces. The sand grains can leave marks on the casting, requiring additional machining or finishing processes to achieve the desired surface quality. This can increase production time and costs.
2. Longer Production Times Sand casting typically involves a longer lead time compared to other casting methods. The process of creating molds and patterns can be time-consuming, resulting in longer production cycles. For high-volume production, this may not be the most efficient choice, as faster methods like die casting may be preferable.
3. Labor-Intensive Process Sand casting can be labor-intensive, requiring skilled workers to handle various tasks, including mold preparation, metal pouring, and post-casting finishing. This reliance on skilled labor can lead to higher costs and potential variability in quality due to differences in workmanship.
4. Limited Detail and Complexity While sand casting can produce large and complex shapes, it may struggle with intricate designs that require fine details. Features such as sharp edges or thin sections may not be well-represented in sand castings, which can limit its applications in precision-engineering fields.
5. Environmental Concerns Related to Sand Despite its recyclable elements, sand casting still has environmental concerns. The extraction of silica sand can lead to habitat disruption and ecological impact. Additionally, the dust generated during the sand preparation process poses health risks to workers if not properly managed.
Conclusion
In summary, the sand casting process offers a mix of advantages and disadvantages that manufacturers must weigh when considering this method for their production needs. Its cost-effectiveness, versatility, and ability to handle large parts make it a valuable option for many industries. However, challenges such as surface finish quality, longer production times, and labor intensity highlight the importance of assessing specific project requirements and context. By understanding these factors, businesses can make informed decisions on whether sand casting aligns with their manufacturing goals.
Post time:Spa . 19, 2024 20:54
Next:Guldsand till salu