Exploring the Potential of 3D Sand Printing for Casting Applications
The advent of 3D printing technology has revolutionized various industries, and one area that has seen significant advancements is casting, particularly through the innovation of 3D sand printing. This method allows for the rapid production of high-quality sand molds and cores that are essential for metal casting processes. As industries strive for efficiency, cost-effectiveness, and sustainability, 3D sand printing emerges as a game-changer.
3D sand printing, also known as additive sand manufacturing, involves the layer-by-layer deposition of sand to create complex mold geometries directly from a computer-aided design (CAD) model. Traditional casting methods require extensive tooling and often involve multiple steps to create the molds. In contrast, 3D sand printing drastically reduces these steps, enabling manufacturers to produce intricate designs without the need for expensive and time-consuming tooling. This technology not only accelerates the production process but also allows for greater design flexibility and the ability to produce highly detailed components.
Exploring the Potential of 3D Sand Printing for Casting Applications
Furthermore, 3D sand printing has notable environmental advantages. Traditional casting processes often generate a significant amount of waste material. By utilizing sand that can be recycled and reused, 3D sand printing minimizes waste and contributes to more sustainable manufacturing practices. The reduction in the need for metal-consuming tooling also means less material is wasted during the production of molds, thus lowering the overall environmental footprint of the casting process.
3d sand printing casting
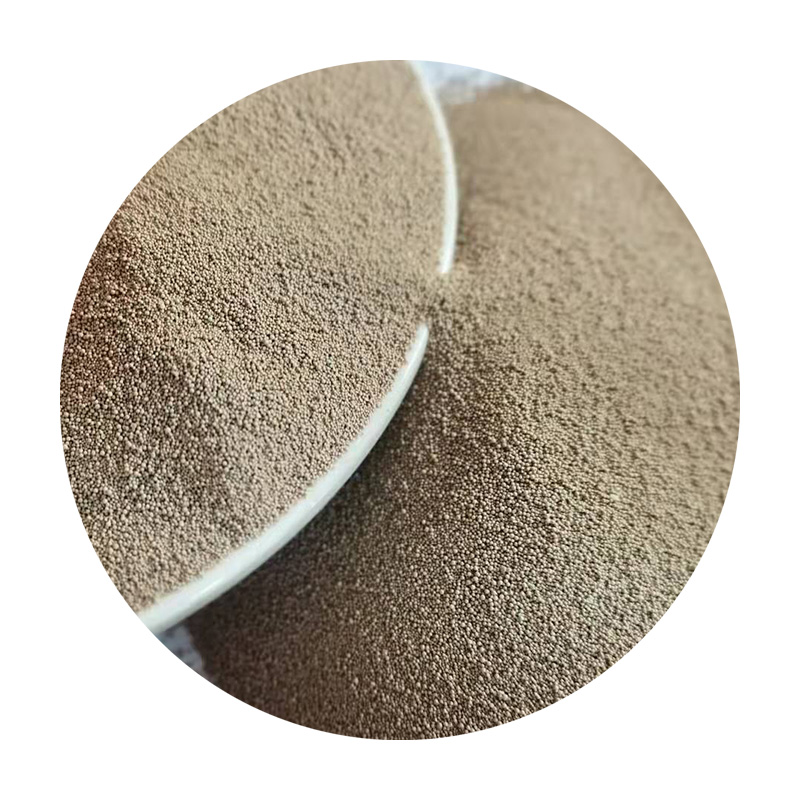
Another noteworthy aspect of 3D sand printing is its compatibility with a variety of sand types and binding agents. This versatility means that manufacturers can choose the appropriate materials for their specific application, whether it requires high strength, heat resistance, or other specialized properties. As a result, 3D sand printing offers tailored solutions that can meet the demanding requirements of various industries.
Despite its myriad advantages, 3D sand printing is not without challenges. The technology is still relatively new, and as such, it can be more expensive than traditional methods when considering the upfront investment in machinery and training. Additionally, not all designs are well-suited for 3D printing, as intricate designs may require post-processing or adjustments to ensure successful casting.
However, as the technology matures and adoption increases, these challenges are likely to become manageable. With ongoing research and development, improvements in materials science, and advancements in printing methodologies, the cost-effectiveness and capabilities of 3D sand printing for casting are expected to improve.
In conclusion, 3D sand printing represents a transformative force in the field of casting. Its ability to reduce lead times, minimize waste, and enhance design flexibility positions it as a pivotal technology for modern manufacturing. As industries continue to embrace digital transformation and seek more sustainable practices, 3D sand printing is poised to play an increasingly important role in the future of casting. With its numerous benefits and evolving capabilities, 3D sand printing is not just a trend but a significant leap towards the future of efficient and innovative manufacturing.
Post time:Lap . 05, 2024 00:13
Next:how to sand ceramic