What is Sand Casting?
Sand casting is one of the oldest and most widely used metal casting processes, primarily due to its versatility, cost-effectiveness, and the ability to produce complex shapes. This method involves the production of metal parts by pouring molten metal into a mold made of sand, which is then allowed to cool and solidify. The versatility of sand casting makes it applicable in various industries, ranging from automotive to aerospace, and even artistic applications.
The Sand Casting Process
The sand casting process can be broken down into several key steps
1. Pattern Creation The first step is to create a pattern, which is a replica of the final product. Patterns can be made from various materials, including wood, metal, or plastic. The pattern should be slightly oversized to account for contraction of the metal as it cools.
2. Mold Preparation The pattern is placed in a sand mixture, typically consisting of sand, clay, and moisture, to create the mold. The sand is packed tightly around the pattern, and once the mold is formed, it is removed from the pattern. This produces a cavity that reflects the shape of the pattern.
3. Core Making If the casting requires internal features or hollow sections, cores are created from a similar sand mixture. These cores are placed into the mold cavity during assembly and serve to form the internal geometries of the final product.
4. Mold Assembly The two halves of the mold (cope and drag) are assembled, and additional features such as vent holes and pouring gates are added to accommodate the flow of molten metal.
5. Metal Pouring The mold is then heated, and the metal is melted in a furnace before being poured into the mold cavity. It is critical to ensure that the metal is poured at the right temperature to avoid defects in the final cast.
6. Cooling After the mold is filled, it is allowed to cool, which can take anywhere from minutes to several hours, depending on the size of the casting and the metal used.
7. Mold Removal Once the metal has cooled and solidified, the sand mold is broken away to reveal the cast part. This is often done using vibration or mechanical means to minimize damage to the casting.
8. Finishing After the casting is removed, it may require additional finishing processes such as grinding, machining, or polishing to meet the desired specifications and surface finish.
Advantages of Sand Casting
what is a sand casting
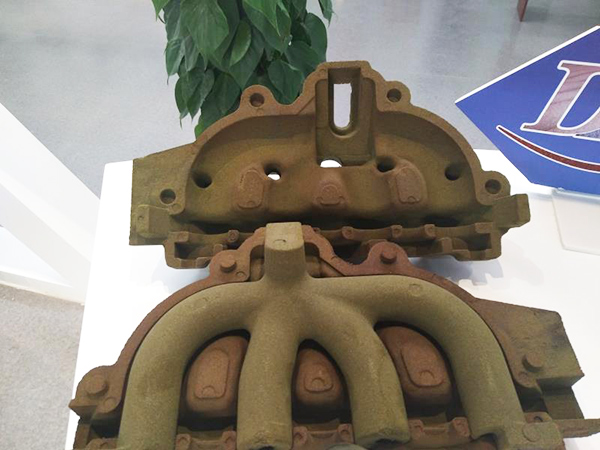
The use of sand casting comes with several advantages, which include
- Cost-Effectiveness Sand is a relatively inexpensive material, and the processes involved do not require expensive machinery, making it suitable for both small and large production runs
.- Flexibility Sand molds can be easily modified and made to accommodate different designs, making sand casting an excellent choice for custom or complex shapes.
- Variety of Materials A wide range of metals can be cast using sand casting techniques, including iron, steel, aluminum, and non-ferrous alloys, allowing for diverse applications.
- Large Part Capabilities Sand casting can produce large parts that are challenging or impossible to manufacture using other methods.
Disadvantages of Sand Casting
While sand casting offers several benefits, it also has its limitations
- Surface Finish The surface finish of sand-cast items may not be as smooth as those produced by other casting methods, and may require additional finishing steps.
- Dimensional Tolerances Sand casting typically has lower dimensional accuracy compared to other casting processes like investment casting or die casting, which might necessitate further machining.
- Labor-Intensive The process can be labor-intensive, particularly in manual operations where skilled workers are required to prepare molds and patterns.
Conclusion
Overall, sand casting is a proven and reliable casting method that continues to be widely used due to its flexibility and cost-effectiveness. Whether producing intricate designs for artistic projects or essential components for heavy machinery, sand casting remains an important technique in modern manufacturing. With ongoing advancements in materials and technologies, its role is likely to evolve, adapting to meet the ever-changing demands of various industries.
Post time:ພ.ຈ. . 10, 2024 07:15
Next:Exploring the Art and Techniques of Casting Sand in Metalworking