Types of Sand Casting Processes
Sand casting is one of the oldest and most versatile methods of metal forming. Due to its relatively low cost and ability to create complex geometries, it is widely used in various industries, from automotive to aerospace. The sand casting process involves creating a mold from sand, pouring liquid metal into the mold, and allowing it to solidify. This article explores the different types of sand casting processes and their specific applications.
1. Green Sand Casting
Green sand casting is perhaps the most traditional form of sand casting. This method uses a mixture of sand, clay, and water that retains moisture, allowing it to bond together. The green in green sand refers to the moisture content, not the color. This type of casting is easy to mold and is ideal for producing small to medium-sized components. The green sand process is advantageous due to its ability to produce intricate designs with a good surface finish. It is often utilized in the production of engine blocks, housings, and various machinery parts.
No-bake sand casting, also known as air-set sand casting, utilizes a mixture of sand and resin that hardens at room temperature. This eliminates the need for moisture, resulting in a more durable mold. The absence of moisture reduces defects caused by steam during metal pouring, contributing to a higher-quality finish. No-bake processes are favored for producing larger and more complex parts that require precise geometries, such as turbine housings and large engine components. Moreover, this method is highly adaptable, often used for both ferrous and non-ferrous alloys.
types of sand casting process
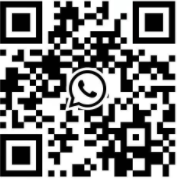
3. Lost Foam Casting
Lost foam casting is a more advanced sand casting process that eliminates traditional molds altogether. Instead, a foam pattern is coated with a refractory material and placed in sand. When molten metal is poured into the mold, it vaporizes the foam, leaving a cavity for the metal to fill. This method produces extremely detailed designs and is particularly useful for manufacturing complex shapes in a single step. Lost foam casting is increasingly popular in industries that necessitate lightweight components with high structural integrity, such as the aerospace sector.
4. Shell Casting
Shell casting combines the principles of sand casting with those of investment casting. In this process, a thin shell of sand is formed around a pattern, usually made of metal. The process begins by heating the pattern, which melts or hardens the resin-coated sand on it, creating a mold. After cooling, the shell is removed, and molten metal is poured in. Shell casting offers excellent surface finishes and tight tolerances, making it suitable for producing intricate parts found in the medical devices, automotive, and aerospace industries.
Conclusion
The world of sand casting is rich with various processes, each catering to specific needs and applications. From traditional green sand casting to advanced lost foam and shell casting methods, manufacturers can choose the process that best meets their requirements in terms of complexity, precision, and cost. As industries continue to evolve, so too will the technologies and techniques used in sand casting, paving the way for innovative applications and products in the future. Understanding these different processes can help engineers and designers make informed decisions that optimize both quality and efficiency in their casting operations.
Post time:ພ.ຈ. . 02, 2024 04:39
Next:sand casting price