Sand Printing Casting The Future of Manufacturing
In the realm of advanced manufacturing processes, sand printing casting emerges as a transformative technique that bridges traditional methods with innovative technology. This process integrates 3D printing with sand casting, offering numerous advantages that are reshaping the landscape of production in various industries, from automotive to aerospace.
Understanding Sand Printing Casting
At its core, sand printing casting involves the creation of a three-dimensional mold using sand as the primary material. Unlike conventional sand casting, where molds are shaped using traditional techniques, sand printing leverages cutting-edge 3D printing technology. A digital model is designed using computer-aided design (CAD) software, which is then transformed into a physical mold layer by layer through a sand printer. The printer deposits a binding agent that solidifies the sand particles, forming a precise mold that mirrors the specifications of the digital design.
Advantages of Sand Printing Casting
1. Customization and Design Flexibility One of the most significant advantages of sand printing casting is its ability to create highly complex geometries and intricate designs that would be impossible or prohibitively expensive with traditional methods. Designers can experiment with innovative shapes and internal structures, ultimately leading to optimized performance and reduced weight in manufactured components.
2. Reduced Lead Times The traditional sand casting process can be time-consuming, often involving multiple steps from pattern making to mold preparation. With sand printing, the entire mold can be produced directly from the digital file, significantly reducing lead times. This rapid prototyping capability allows for quicker iterations and faster time-to-market, which is crucial in today’s competitive environment.
sand printing casting
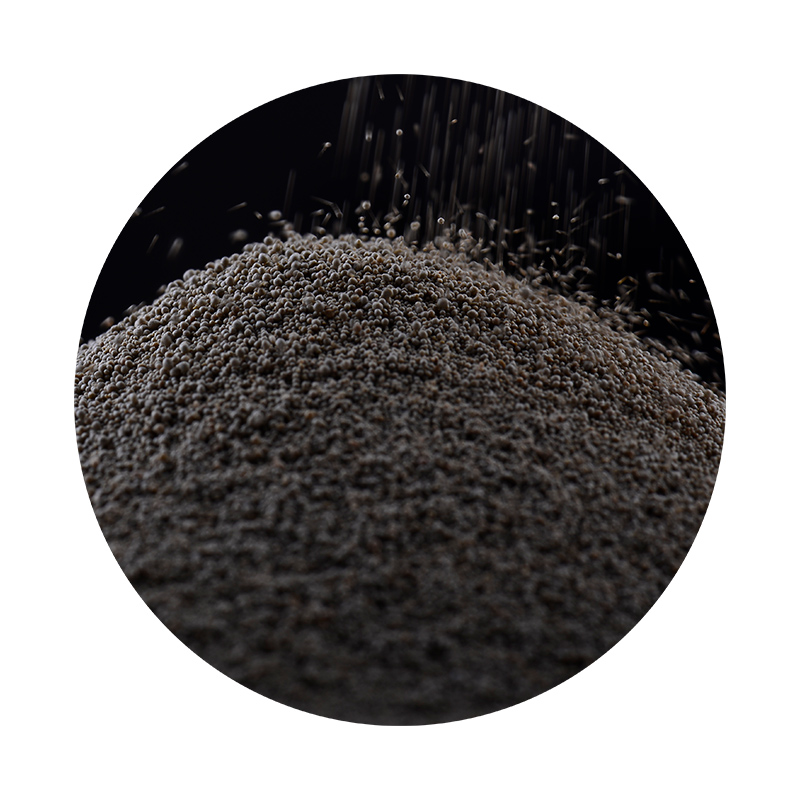
3. Material Efficiency Sand printing casting minimizes waste by using only the necessary amount of sand to create the mold. Traditional methods often result in excess material that must be recycled or discarded, whereas sand printing can optimize material usage, contributing to cost savings and sustainability.
4. Enhanced Accuracy and Surface Finish The precision of 3D printing technology allows for molds that have superior dimensional accuracy and a finer surface finish compared to traditional sand casting. This reduced need for post-processing not only saves time but also enhances the quality of the final product.
Applications Across Industries
The applications for sand printing casting are vast and varied. In the automotive industry, manufacturers can produce complex engine components that improve fuel efficiency and performance. Aerospace companies benefit from lightweight structures that enhance aircraft performance while reducing fuel consumption. Moreover, industries such as medical devices are finding value in the customization capabilities of sand printing, enabling the production of patient-specific implants and prosthetics.
Conclusion
As industries continue to evolve and demand for more efficient, customizable, and sustainable manufacturing solutions grows, sand printing casting stands out as a pivotal technology. By merging the longstanding tradition of sand casting with the innovative capabilities of 3D printing, manufacturers can achieve new heights in productivity, quality, and design. This cutting-edge approach not only meets the needs of modern-day production but also paves the way for a future where the boundaries of manufacturing are continually pushed. With ongoing advancements in materials and technology, the potential of sand printing casting is limited only by our imagination.
Post time:ຕ.ລ. . 14, 2024 14:57
Next:super sand bond g2