The Role of Sand Casting in Mass Production
Sand casting is a versatile and widely used manufacturing process that has been a staple in various industries for decades. This technique, which involves pouring molten metal into a sand mold to create complex shapes and components, has proven to be an effective method for mass production. As industries pursue faster and more efficient methods of production, sand casting occupies a significant place due to its numerous advantages and adaptability to different requirements.
The Process of Sand Casting
The sand casting process begins with the creation of a mold made from a mixture of sand, clay, and water. The sand is packed around a pattern, which is a replica of the final product. Once the mold is created, the pattern is removed, and the mold is prepped for pouring. Molten metal is then poured into the cavity of the mold and allowed to cool and solidify. After the metal has hardened, the sand mold is broken apart to reveal the finished casting.
One of the significant benefits of sand casting is its capability to produce intricate and complex shapes that would be difficult or impossible to create using other methods. The flexibility in mold creation allows for the production of large-scale components, small parts, and everything in between. This versatility makes sand casting suitable for various industries, including automotive, aerospace, and machinery.
Advantages of Sand Casting for Mass Production
1. Cost-Effectiveness One of the main advantages of sand casting is its cost-effectiveness, particularly for low to medium production runs. The materials used for molds, primarily sand, are relatively inexpensive, and the process itself does not require expensive equipment. This makes it an attractive option for companies looking to reduce production costs without sacrificing quality.
2. Material Versatility Sand casting is compatible with a wide range of metals, including aluminum, steel, iron, and copper alloys. This versatility allows manufacturers to select the best material for their specific application, meeting various mechanical properties and performance standards.
sand casting mass production
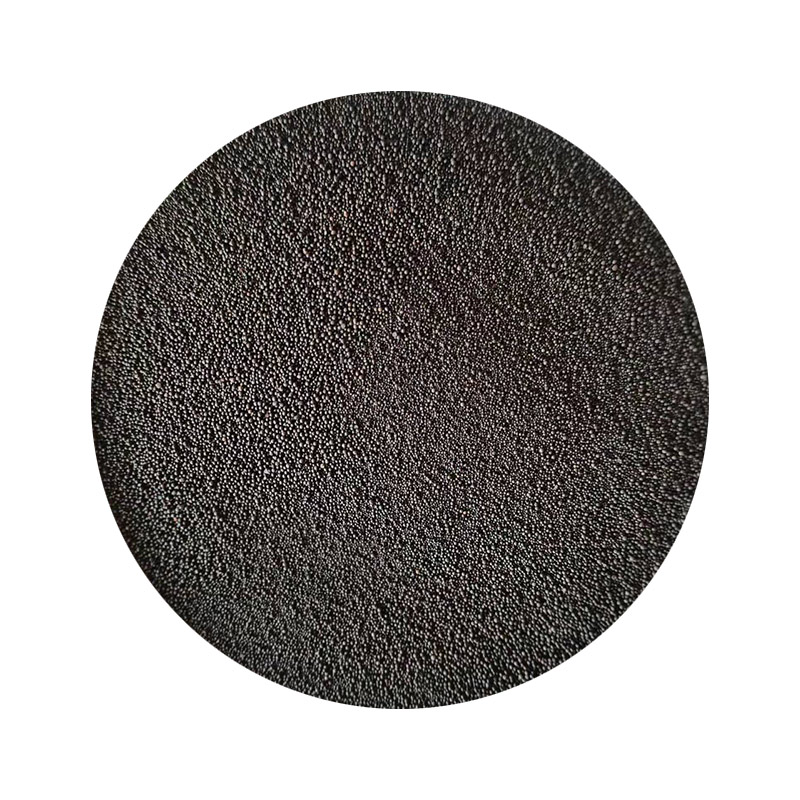
3. Scale of Production While sand casting is often associated with low and medium volume production, it is also capable of scaling up for mass production needs. Automation in the pouring process and improvements in mold-making technology have enabled foundries to produce larger quantities of castings with consistent quality.
4. Quick Turnaround The time required to create a sand mold is significantly shorter than that of other casting processes, particularly for complex shapes. This quick turnaround enables manufacturers to respond rapidly to market demands and reduces lead times for delivery.
5. Minimal Waste Sand casting generates less waste compared to other methods, as the sand used in molds can often be reclaimed and reused for multiple casting cycles. The efficient use of materials aligns with modern sustainability practices, appealing to manufacturers focused on reducing their environmental impact.
Challenges in Sand Casting
Despite its numerous advantages, sand casting does come with challenges. Quality control can be an issue, as defects such as sand inclusions, gas pockets, and dimensional inaccuracies can occur. To mitigate these issues, foundries must invest in advanced quality assurance measures and technologies that monitor the casting process closely.
In addition, while sand casting is versatile, it may have limitations in some specialized applications requiring extremely tight tolerances or surface finishes. In such cases, additional machining processes may be necessary, which can add to lead times and costs.
Conclusion
In conclusion, sand casting remains a vital method for mass production across various industries. Its cost-effectiveness, material versatility, and ability to create complex shapes make it an essential technique for manufacturers striving to meet the demands of modern production. As technological advancements continue to enhance the sand casting process, its role in mass production is likely to become even more prominent, providing innovative solutions to the ever-evolving challenges faced by engineers and manufacturers. By embracing both its strengths and addressing its challenges, industries can leverage sand casting to produce high-quality components efficiently and sustainably.
Post time:ຕ.ລ. . 13, 2024 02:31
Next:球状砂の特性と応用に関する研究の最新動向