The Art and Science of Sand Casting Foundries
Sand casting, a process that has been employed for centuries, is one of the most versatile and widely used methods in metal casting. It involves the creation of a metal component by pouring molten metal into a mold made from sand. Despite the emergence of advanced manufacturing techniques, sand casting remains indispensable due to its cost-effectiveness and capacity to produce intricately shaped components.
Understanding Sand Casting
The sand casting process begins with the preparation of the mold. A sand mixture, typically consisting of sand, clay, and water, is compacted around a pattern that represents the desired final product. Once the mold halves are prepared, the pattern is removed, leaving a hollow cavity that mirrors the shape of the object to be cast. The two halves of the mold are then reassembled, and molten metal is poured into the cavity.
After the metal cools and solidifies, the mold is broken away to reveal the cast object. The simplicity of this process allows for a wide range of metal types to be utilized, including aluminum, bronze, iron, and steel. This versatility in materials makes sand casting an ideal choice for various industries, including automotive, aerospace, and art.
Advantages of Sand Casting
One of the primary advantages of sand casting is its cost-effectiveness. The materials required to create sand molds are readily available and inexpensive, making it an attractive option for both large-scale production and small batch runs. Additionally, the sand can be reused multiple times, further reducing costs and waste.
Another significant benefit is the design flexibility offered by sand casting. Patterns can be made in virtually any shape, accommodating complex geometries that may be difficult or impossible to achieve with other casting methods. This is particularly important in industries where precision and custom components are essential.
Furthermore, sand casting allows for the production of large components that might be challenging to manufacture with other techniques. The ability to cast large parts, such as engine blocks or marine components, has positioned sand casting as a vital process in many manufacturing sectors.
sand casting foundries
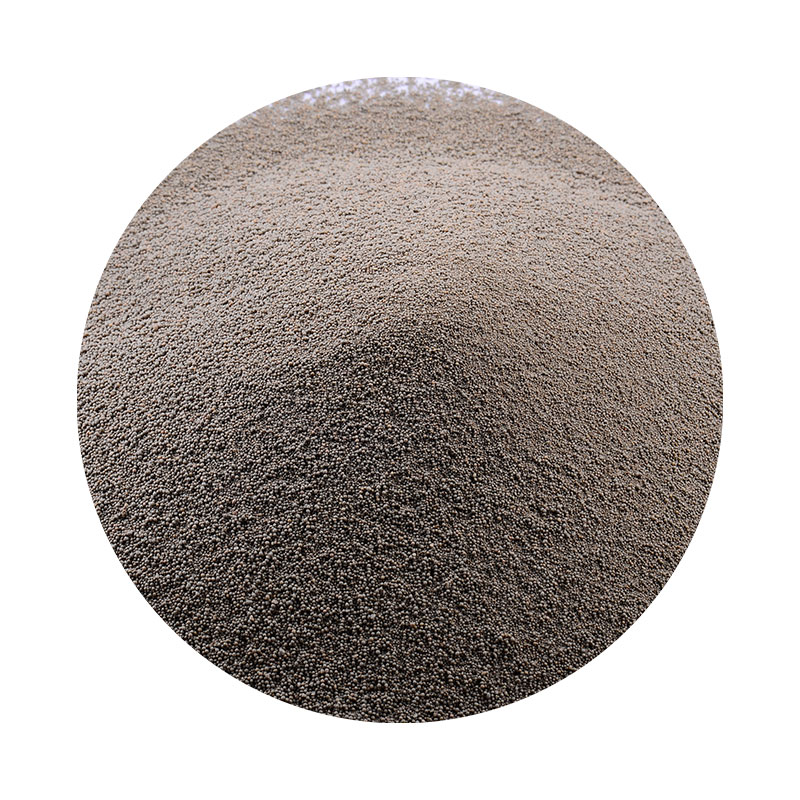
Challenges in Sand Casting
Despite its advantages, sand casting is not without its challenges. One of the most notable issues is the potential for defects in the final product, such as porosity, cold shuts, or sand inclusion. These defects can arise from various factors, including inadequate venting, improper temperature management, or inconsistencies in the sand mixture. To mitigate these risks, foundries invest in quality control measures and continuous process improvement.
Another challenge is the limited surface finish quality that can be achieved through sand casting. The rough texture of sand molds can lead to a final product that requires additional machining or finishing processes to meet the desired specifications. In applications where surface finish is critical, manufacturers must weigh the time and cost implications of secondary operations against the inherent benefits of sand casting.
Innovations in Sand Casting
As industries evolve, so do the techniques used in sand casting. Advances in technology, such as the implementation of 3D printing to create molds and patterns, have revolutionized the sand casting process. This innovation allows for rapid prototyping and the ability to produce more complex shapes with decreased lead times.
Moreover, the integration of computer simulations in the casting process has enhanced the prediction of mold behavior and metal flow, leading to improved designs and reduced defects. Foundries are continuously exploring new materials, such as environmentally friendly sand mixtures and binders, to enhance sustainability in manufacturing.
Conclusion
Sand casting foundries play a crucial role in the manufacturing landscape. Their ability to produce complex components at a low cost makes them a fundamental element in various industries. While challenges persist, ongoing innovations ensure that sand casting remains a relevant and vital technology. As the industry continues to adapt and evolve, the fusion of tradition and technology promises to keep sand casting at the forefront of metal manufacturing for years to come.
Post time:ທ.ວ. . 05, 2024 20:01
Next:Cast of Sandcastle Dreams 2014