Sand Casting Alloys A Comprehensive Overview
Sand casting is one of the oldest and most versatile metal forming processes in manufacturing. It involves creating a mold from sand to pour molten metal into, producing various metal components. The choice of alloy for sand casting is critical, as it influences the properties of the final product, including strength, ductility, corrosion resistance, and performance under various conditions. In this article, we will explore the common alloys used in sand casting, their properties, applications, and considerations that engineers and manufacturers must take into account.
Common Alloys in Sand Casting
1. Aluminum Alloys Aluminum is a popular choice for sand casting due to its lightweight and excellent corrosion resistance. Common aluminum alloys used in sand casting include 356.0 and 319.0. These alloys are known for their good mechanical properties, excellent thermal conductivity, and ability to be anodized for enhanced surface protection. They are widely used in automotive components, aerospace parts, and consumer products.
2. Cast Iron Cast iron is another traditional material in sand casting, known for its high wear resistance and excellent machinability. The most common types include gray iron, ductile iron, and white iron. Gray iron offers superior castability and is often used in engine blocks and machine bases. Ductile iron, with its enhanced ductility and tensile strength, is favored for more demanding applications, such as in automotive parts and structural components.
3. Steel Alloys Steel is perhaps the most versatile metal for casting, offering a wide range of properties tailored to specific applications. Common steel alloys used in sand casting include carbon steel, tool steel, and stainless steel. Carbon steel castings are widely used in structural applications, while tool steel castings are ideal for manufacturing cutting tools and dies. Stainless steel castings, known for their excellent corrosion resistance, are commonly utilized in the food and medical industries.
4. Magnesium Alloys Magnesium alloys are gaining popularity in sand casting due to their high strength-to-weight ratio and good corrosion resistance. While more challenging to cast than aluminum, magnesium alloys such as AZ91D and AM60B are increasingly used in the automotive and aerospace sectors for parts requiring lightweight and high-performance characteristics.
Properties and Considerations
When selecting an alloy for sand casting, several properties must be considered, including
sand casting alloys
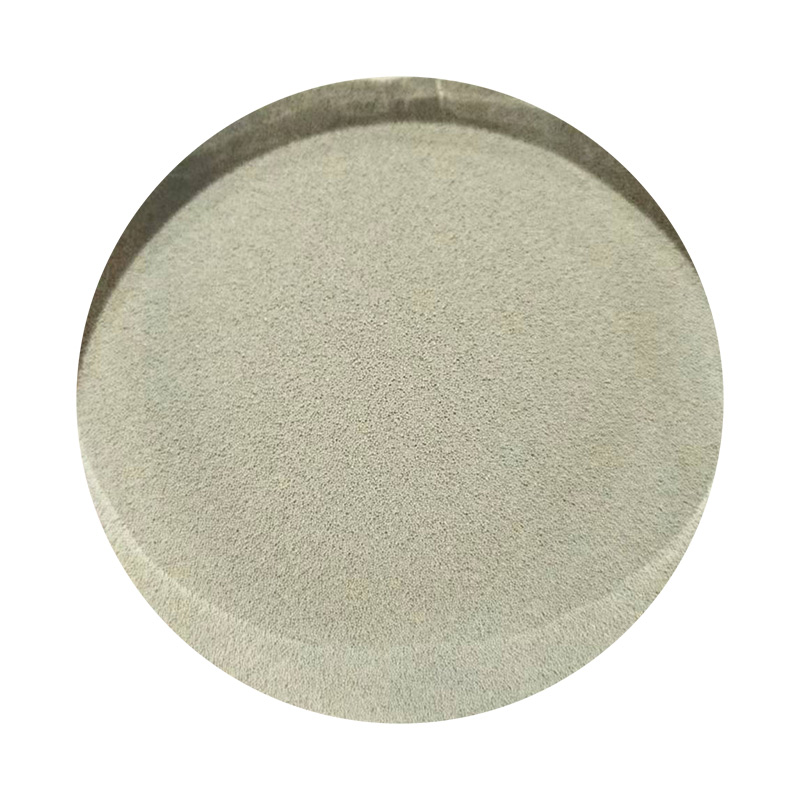
- Mechanical Properties The strength, ductility, toughness, and hardness of the alloy should align with the requirements of the application. For instance, while high-strength alloys are essential for load-bearing components, ductile alloys may be necessary for parts subjected to shock or impact.
- Corrosion Resistance Depending on the environment in which the part will operate, corrosion resistance may be a crucial factor. Alloys with low corrosion susceptibility, such as certain aluminum and stainless steel alloys, are ideal for outdoor or marine applications.
- Castability The ease with which an alloy can be cast influences manufacturing efficiency and costs. Alloys with good fluidity and low shrinkage rates are preferable to reduce defects and improve surface finish.
- Thermal Properties Thermal conductivity and expansion characteristics play crucial roles in the casting process and the performance of the final product, particularly in thermal management applications.
Applications
Sand casting alloys are used in a myriad of applications across various industries. Aluminum alloys are common in automotive and aerospace components, where weight savings are critical. Cast iron find use in heavy machinery, engine blocks, and pipe fittings. Steel alloys are employed in a range of tools, industrial parts, and structural applications. Magnesium alloys are increasingly being used in automotive and aerospace components, particularly where lightweight construction is necessary.
Conclusion
In conclusion, sand casting remains a vital manufacturing process, with a wide variety of alloys available to meet specific performance needs. Understanding the properties, advantages, and limitations of these alloys is essential for engineers and manufacturers to produce high-quality castings that meet stringent industry standards. Whether it's aluminum, cast iron, steel, or magnesium, the right choice of alloy can significantly impact the effectiveness and longevity of sand-cast components. As technology advances, the development of new alloys will undoubtedly open up even more possibilities for innovation in the world of sand casting.
Post time:ທ.ວ. . 05, 2024 22:53
Next:Different Types of Sand Employed in Sand Casting Processes