Understanding Resin Sand Pros and Cons for Modern Foundry Applications
In the ever-evolving field of foundry technology, one material that has gained significant traction in recent years is resin sand. This innovative sand casting material offers numerous advantages over traditional sand and is becoming an indispensable component for manufacturers seeking to produce high-quality metal castings. By understanding the characteristics, benefits, and potential drawbacks of resin sand, foundry operators can make informed decisions that enhance the efficiency and quality of their production processes.
What is Resin Sand?
Resin sand is a type of sand mix where the conventional silica sand is coated with a thermosetting resin, often combined with a hardener. This mixture allows for the creation of molds that can withstand higher temperatures and maintain their shape during the casting process. The resin acts as a binder, offering enhanced strength compared to traditional green sand mixtures, which are primarily held together by moisture and clay.
Key Advantages of Resin Sand
1. High Dimensional Accuracy One of the most significant benefits of using resin sand is its ability to create molds with high dimensional accuracy. The excellent detailing provided by resin-based molds is crucial for producing intricate components in various applications, from automotive to aerospace.
2. Smooth Surface Finish Castings produced using resin sand tend to have a superior surface finish. This minimizes the need for extensive post-processing techniques, thereby reducing production times and costs. The smoother finish also enhances the aesthetic appeal of the final product.
3. Reduced Gas Creation Traditional sand casting methods often lead to gas inclusions in the metal due to moisture in the sand. Since resin sand cures through a chemical reaction rather than moisture evaporation, it significantly reduces the likelihood of gas-related defects, resulting in higher quality castings.
4. Better Thermal Stability Resin sand molds can withstand higher pouring temperatures without breaking down. This allows foundries to work with a broader range of metals, including those with higher melting points. Consequently, manufacturers can diversify their product offerings.
resin sand
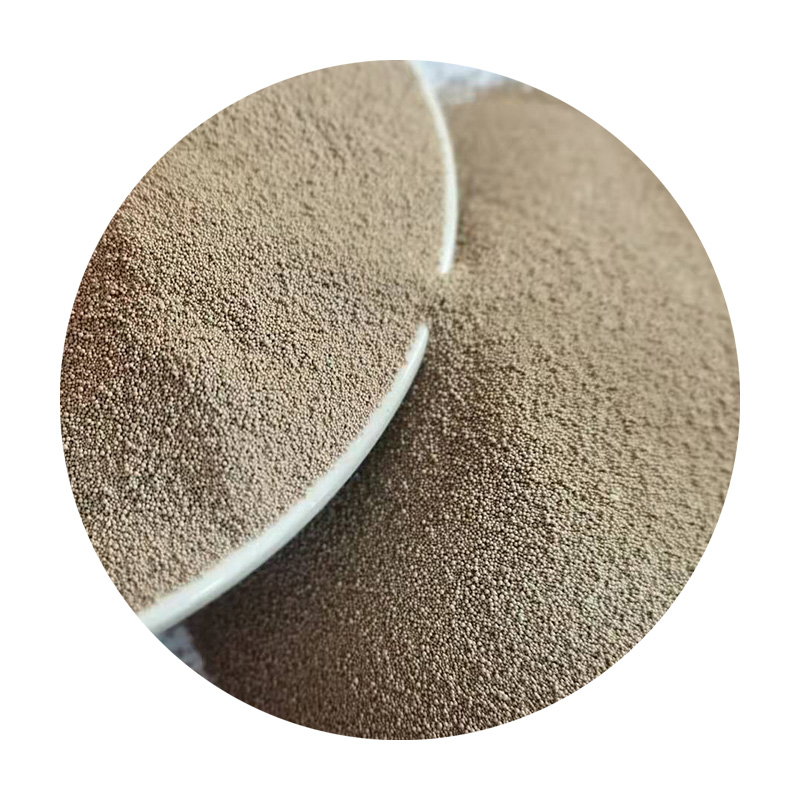
5. Reusability Unlike green sand, which degrades after each use, resin sand molds can be reused multiple times. This not only helps in maintaining production efficiency but also lowers material costs over time.
Potential Drawbacks of Resin Sand
Despite its many advantages, resin sand is not without its challenges.
1. Cost Consideration The initial material and setup costs for resin sand can be higher compared to traditional sand systems. This may be a barrier for smaller foundries or those with limited budgets looking to adopt new technologies.
2. Handling and Storage Resin sand requires careful handling and appropriate storage conditions to prevent premature hardening. This demands more attention from operators compared to conventional sand, potentially increasing labor inputs.
3. Environmental Concerns The use of synthetic resins does raise environmental issues. The disposal of used resin sand can be complicated, and improper disposal can lead to pollution. Therefore, foundries must establish environmentally responsible practices when using resin sand.
4. Heat Sensitivity Although resin sand has superior thermal stability, prolonged exposure to high temperatures can lead to degradation of the resin. This can impact mold strength and casting integrity if not properly managed.
Conclusion
Resin sand represents a significant advancement in foundry materials, providing numerous advantages such as high dimensional accuracy, smooth surface finish, and reduced gas creation. While it does present challenges, such as higher initial costs and environmental considerations, the benefits often outweigh these drawbacks for many applications. As industries continue to evolve and demand higher quality castings, the adoption of resin sand is likely to increase, paving the way for innovative manufacturing solutions in the foundry sector. By understanding both its strengths and limitations, foundries can make strategic choices that leverage resin sand to enhance their production capabilities.
Post time:ພ.ຈ. . 17, 2024 14:20
Next:sand used in foundry