Rapid Sand Casting Revolutionizing the Foundry Industry
Rapid sand casting is an innovative process in the foundry industry that combines traditional sand casting techniques with advanced technologies to produce high-quality metal components efficiently. This method has gained significant popularity due to its ability to reduce lead times and costs while ensuring precision and repeatability in manufacturing.
The fundamental principle of sand casting involves creating a mold from sand to hold molten metal until it solidifies. In rapid sand casting, the process is expedited using sophisticated techniques, such as 3D printing, computer-aided design (CAD), and automated machining. These technologies allow for quicker mold production, resulting in shorter production cycles and faster turnaround times for prototypes and end-use parts.
One of the primary advantages of rapid sand casting is its ability to facilitate the creation of complex geometries and intricate designs. Traditional sand casting often faces limitations in producing detailed features, but with the integration of 3D printing, manufacturers can create complex mold patterns that are often impossible or cost-prohibitive through conventional methods. This capability enables designers to push the boundaries of creativity while ensuring that the end product meets functional requirements.
Additionally, rapid sand casting offers significant material savings. In conventional casting processes, excess material is often required to ensure enough mass is present to create the final component. However, with rapid sand casting’s precision and accuracy, manufacturers can minimize waste, leading to a more sustainable production process. Furthermore, this method allows for the use of a wider variety of materials, including different metal alloys, enhancing the versatility of the casting process.
rapid sand casting
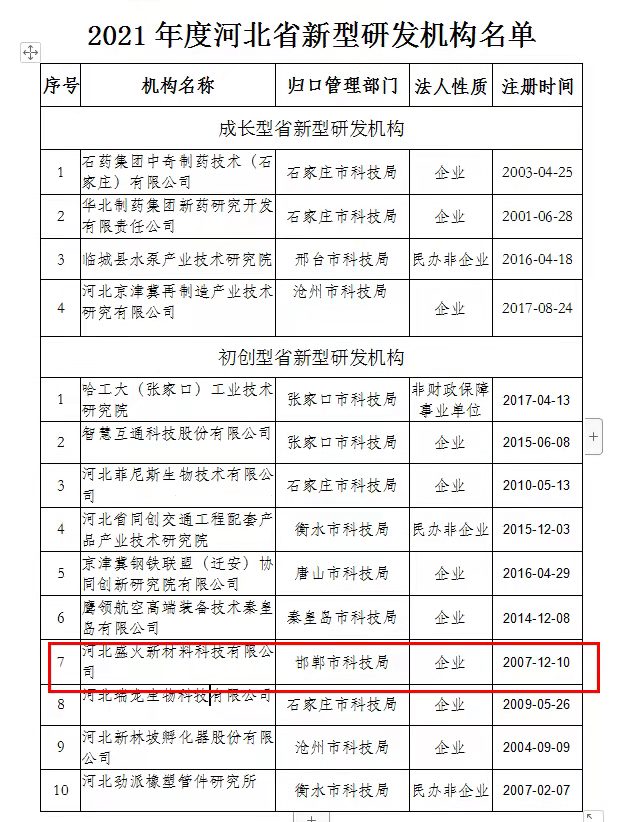
The speed at which components can be produced is another crucial advantage of rapid sand casting. In industries where time-to-market is critical, such as automotive and aerospace sectors, the ability to quickly produce high-quality prototypes and parts can provide a competitive edge. Traditional sand casting can involve long lead times due to mold creation and setup, but rapid methods can significantly compress these timelines, enabling businesses to respond to market demands swiftly.
Moreover, the application of digital technologies in rapid sand casting streamlines the entire workflow. From CAD modeling to simulation software that predicts how molten metal will flow into the mold, advancements in technology enhance the accuracy of the casting process. This symbiosis of design and manufacturing not only increases efficiency but also reduces the likelihood of defects in the final product.
However, while rapid sand casting presents numerous advantages, it is not without challenges. The initial investment in technology and training can be substantial, and there may be a learning curve as industries adopt these new methodologies. Moreover, maintaining quality control and ensuring consistent results in high-volume production requires stringent processes and standards.
In conclusion, rapid sand casting stands at the forefront of the foundry industry’s evolution. By merging traditional casting techniques with modern technology, manufacturers can achieve unprecedented efficiency, precision, and sustainability. As industries continue to embrace innovation, rapid sand casting is likely to play a critical role in shaping the future of manufacturing, enabling the production of high-quality, complex components more quickly and economically than ever before. With ongoing advancements, this method promises to be a game-changer, ensuring that manufacturers can keep pace with the demands of modern technology and market needs.
Post time:ຕ.ລ. . 06, 2024 09:23
Next:foundry sands