Making Foundry Sand An Essential Process in Metal Casting
Foundry sand plays a pivotal role in the metal casting industry, serving as a crucial component in the creation of metal castings. The process of making foundry sand involves several stages, each essential to ensure high-quality output with optimal performance during casting. This article explores the importance of foundry sand, the materials used, and the steps involved in its production.
Foundry sand, primarily composed of silica, is selected for its ability to withstand high temperatures and its excellent flowability, which enhances mold-making. The most commonly used types of foundry sand include green sand, resin-coated sand, and investment casting sand. Green sand, made from a mixture of silica sand, clay, and water, is widely favored for its ability to form excellent molds. Its moisture content allows for the formation of compact molds that withstand the pouring of molten metal.
The first step in the production of foundry sand is the selection of raw materials. High-quality silica is essential as it dictates the strength and durability of the final product. The silica sand is usually mined from riverbanks or sand dunes and is then processed to remove impurities, ensuring a uniform particle size and improved characteristics. Geological surveys are conducted to identify suitable locations, as the quality of the sand directly affects casting quality.
After sourcing the raw material, the next step is washing and classifying the sand. The sand is screened to eliminate larger particles and debris, typically using mechanical shakers or vibrating screens. This process ensures that only the finest grains, which are crucial for molding, are utilized. The washing process also helps to remove clay and silt that might negatively impact the performance of the foundry sand during casting.
making foundry sand
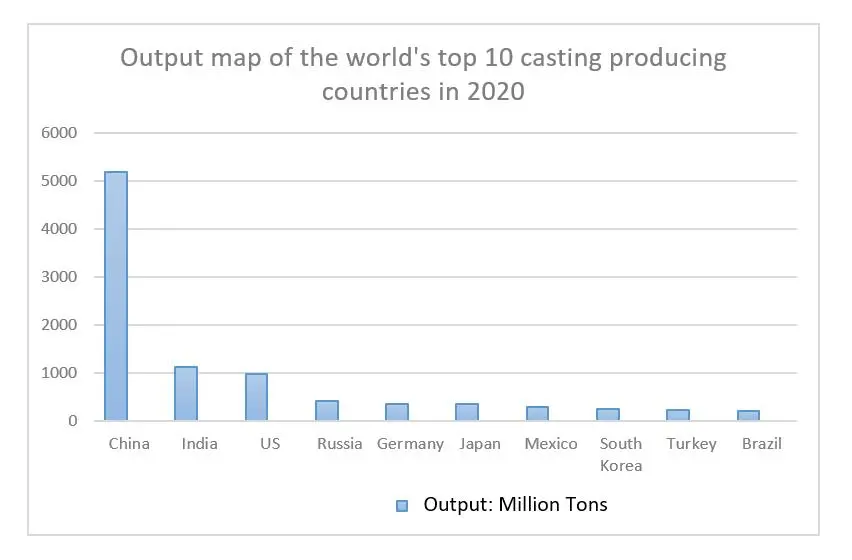
Once cleaned, the sand may undergo further processing depending on the type of foundry sand being produced. For green sand, a specific percentage of clay and water is added to the silica sand. The correct balance is critical, as it influences the sand's cohesiveness and workability. The mixture is then thoroughly blended to achieve uniform moisture content and consistency, ready for molding.
For resin-coated sand, the sand grains are coated with a thin layer of resin binder. This process usually involves mixing the sand with the resin and then curing it through heat, creating a strong bond between the particles. This type of sand is particularly useful for producing complex shapes and helps reduce the loss of detail during the cast.
Finally, quality control checks are paramount throughout the sand-making process. Advanced lab techniques are used to analyze grain size distribution, chemical composition, and thermal properties. This ensures that the final product meets the required specifications, providing an adequate medium for metal casting operations.
In conclusion, the process of making foundry sand is intricate and critical to the success of metal casting. With the right selection of materials and careful processing, manufacturers can produce high-quality foundry sand that ensures effective and precise mold creation, ultimately leading to superior castings. This underlines the importance of foundry sand in the metallurgy field and its impact on the overall performance of the casting process.
Post time:ພ.ຈ. . 19, 2024 19:38
Next:3d sand casting