Lost Foam Casting Materials An Innovative Approach to Metal Casting
Lost foam casting (LFC) is an advanced metal casting technique that utilizes a unique method of pattern creation and mold making. Unlike traditional sand casting, which employs a sand mold to form the shape of the final product, lost foam casting uses a foam pattern that is vaporized during the metal pouring process. This innovative method offers a range of benefits, particularly when it comes to the materials involved in the casting process. This article explores the various materials used in lost foam casting and their significance in achieving high-quality castings.
At the core of lost foam casting is the foam pattern, typically made from polystyrene or similar materials. Polystyrene foam is favored due to its lightweight nature, ease of shaping, and ability to be produced in complex geometries. The pattern is created by shaping the foam into the desired form, which is then coated with a thin layer of refractory material to create a mold. This coating not only protects the foam but also helps to create a smooth surface finish on the final casting.
One of the key advantages of using foam materials in lost foam casting is the elimination of draft angles that are commonly required in traditional sand mold designs. Since the foam pattern is vaporized, there is no need for additional draft, allowing for tighter tolerances and more intricate designs. This capability enables manufacturers to produce highly detailed parts that are typically challenging to achieve with other methods, thus expanding the design possibilities for engineers and designers.
In addition to polystyrene, other materials can be used for the foam patterns, such as polyurethane. Polyurethane is known for its durability and can withstand higher temperatures during the pouring process. This material choice allows for the creation of more robust patterns that can maintain their shape without deformation, further improving the accuracy and surface finish of the final casting.
lost foam casting materials
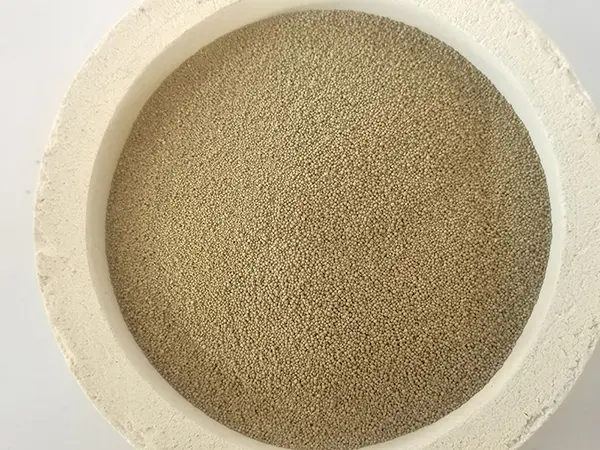
The choice of metal for the casting process is equally important and can vary based on the application. Common metals used in lost foam casting include aluminum, brass, and iron. Each of these metals has its properties that make them suitable for different applications. For instance, aluminum, with its lightweight and corrosion-resistant properties, is ideal for automotive components, while brass is often used for plumbing fittings and decorative items due to its aesthetic qualities.
Another crucial material aspect is the coating that is applied to the foam pattern. The coating, often made of a mixture of sand and a binding agent, serves multiple purposes it provides stability to the foam during casting, it enhances the finish of the casting by reducing surface imperfections, and it helps control the vaporization process of the foam, minimizing defects in the final product.
The environmental benefits of lost foam casting materials should also not be overlooked. The process generates less waste compared to traditional casting methods, as the patterns are made using expandable polystyrene that can be fully consumed during the casting process. Moreover, advancements in recycling methods for used foam materials are continuously being developed, further reducing the environmental impact of lost foam casting.
In conclusion, lost foam casting represents a significant advancement in the field of metal casting, with its unique use of foam materials allowing for complex designs, superior surface finishes, and reduced waste. As technology continues to evolve, the materials and methods associated with lost foam casting will undoubtedly improve, providing greater opportunities for innovation in manufacturing processes across various industries. Whether for small-scale production or large manufacturing applications, the benefits of lost foam casting materials are clear, solidifying its place in modern metal casting techniques.
Post time:ພ.ຈ. . 27, 2024 05:19
Next:Finding High-Quality Sand Casting Manufacturers for Your Production Needs