Lost Foam Casting Coating A Comprehensive Overview
Lost foam casting is a unique and efficient metal casting process that has gained considerable attention in various manufacturing sectors. This method allows for the production of complex shapes with a high degree of precision. One of the pivotal aspects of lost foam casting is the coating applied to the foam patterns. This article delves into the importance, materials, and methodologies involved in lost foam casting coating, highlighting its crucial role in the casting process.
The Basics of Lost Foam Casting
Lost foam casting (LFC) is an advanced technique where a foam pattern is used to create a mold. The process begins with the fabrication of a foam model that is then coated with a layer of refractory material. After the coating hardens, the foam is vaporized upon pouring the molten metal, thus leaving a cavity in the desired shape. This approach eliminates the need for traditional sand molds, allowing for more complex geometries and reducing machining time.
Importance of Coating in Lost Foam Casting
The coating serves several purposes in the lost foam casting process. Primarily, it provides a protective barrier between the foam pattern and the liquid metal, preventing the foam from contaminating the molten material and ensuring the integrity of the finished product. Additionally, the coating enhances the surface finish of the casting, leading to reduced post-casting machining requirements.
Moreover, the coating helps regulate the heat transfer during the metal pouring process. A well-designed coating can control the cooling rates, which is crucial in preventing defects such as cracking or warping in the final casting. Therefore, selecting the appropriate coating material and applying it effectively is paramount for the success of the lost foam casting operation.
Materials Used in Coatings
The choice of coating materials is vast and can significantly influence the overall performance of the lost foam casting process. Common materials used for coatings include
2. Binders Organic or inorganic binders may be incorporated to enhance adhesion between the coating and the foam pattern. Common binders include sodium silicate and various ceramic adhesives.
lost foam casting coating
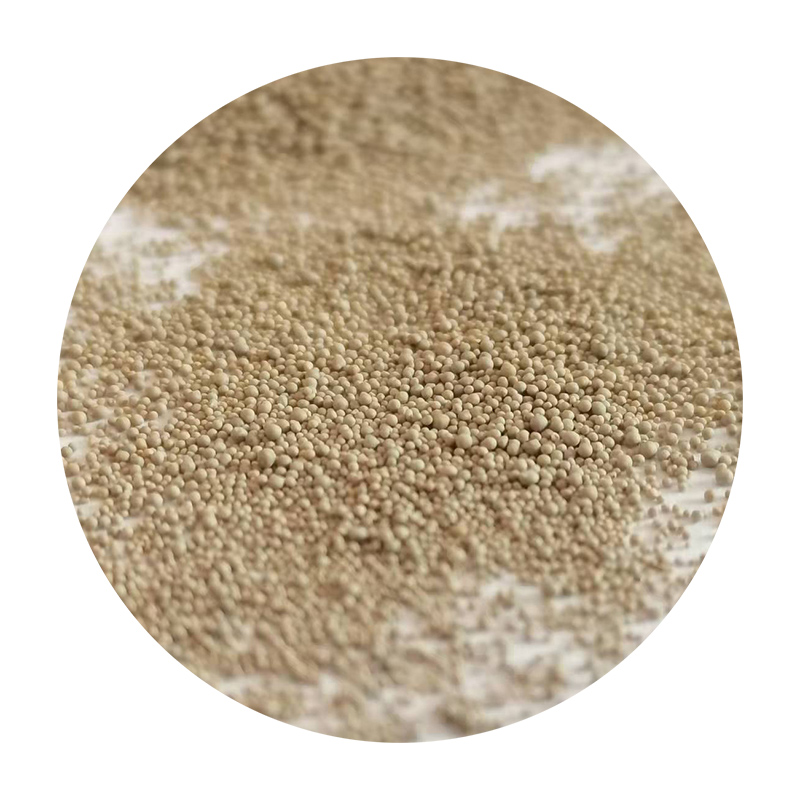
3. Additives To improve specific properties of the coating, various additives, such as colorants or agents that enhance thermal conductivity, might be added.
4. Aerospace and Automotive Grade Coatings In industries demanding high-performance materials, specialized coatings designed for aerospace or automotive applications are employed to meet stringent quality standards.
Coating Methodologies
The application of the coating can be performed using different methodologies, depending on the specific requirements of the casting process. Typical coating techniques include
1. Dipping The foam pattern is immersed in a slurry of the coating material, allowing for a uniform coating.
2. Spraying Using high-pressure spray equipment, a fine mist of coating is applied to the foam surface, which is particularly effective for achieving intricate details.
3. Brushing For smaller patterns or detailed areas, manual brushing can be employed, allowing for precise control over the coating thickness.
After application, the coated patterns need to be dried and cured to ensure stability before the casting process begins. Proper curing is essential to achieve the desired mechanical strength and thermal resistance of the coating.
Conclusion
Lost foam casting represents a revolutionary method in the casting industry, enabling manufacturers to produce intricate designs while maintaining high levels of efficiency and quality. The coating applied to foam patterns is a critical element in this process, influencing not only the success of the casting but also the quality of the final product. By understanding the materials, importance, and methodologies involved in lost foam casting coatings, manufacturers can optimize their processes to achieve better performance and superior outcomes in their production lines. As industries continue to evolve, advancements in coating technologies will play a crucial role in enhancing the capabilities of lost foam casting, furthering its adoption across various sectors.
Post time:ພ.ຈ. . 24, 2024 16:32
Next:Crafting Unique Creations with Sand and Cast Techniques for Artistic Expression