The Significance of Foundry Sand in Metal Casting
Foundry sand, an essential component in the metal casting industry, plays a pivotal role in producing high-quality cast parts. This specialized sand is primarily used to create molds for melting metal and shaping it into desired forms. Its unique properties, such as thermal stability, low expansion rate, and excellent permeability, make it the preferred material for foundries worldwide.
One of the primary types of foundry sand is silica sand, which is composed mainly of silicon dioxide (SiO2). Its granular structure and consistent grain size contribute to its effectiveness in mold making. When heated, silica sand retains its shape and structural integrity, allowing it to withstand the extreme temperatures encountered during the metal pouring process. This property is crucial, as it ensures that the molds maintain their form and provide accurate dimensions for the final product.
In addition to silica sand, other materials like olivine, zircon, and chromite are also used, depending on the specific requirements of the casting process. For example, olivine sand, which has a higher melting point, is suitable for casting ferrous metals, while zircon sand’s low thermal expansion makes it ideal for precision molds.
foundry sand
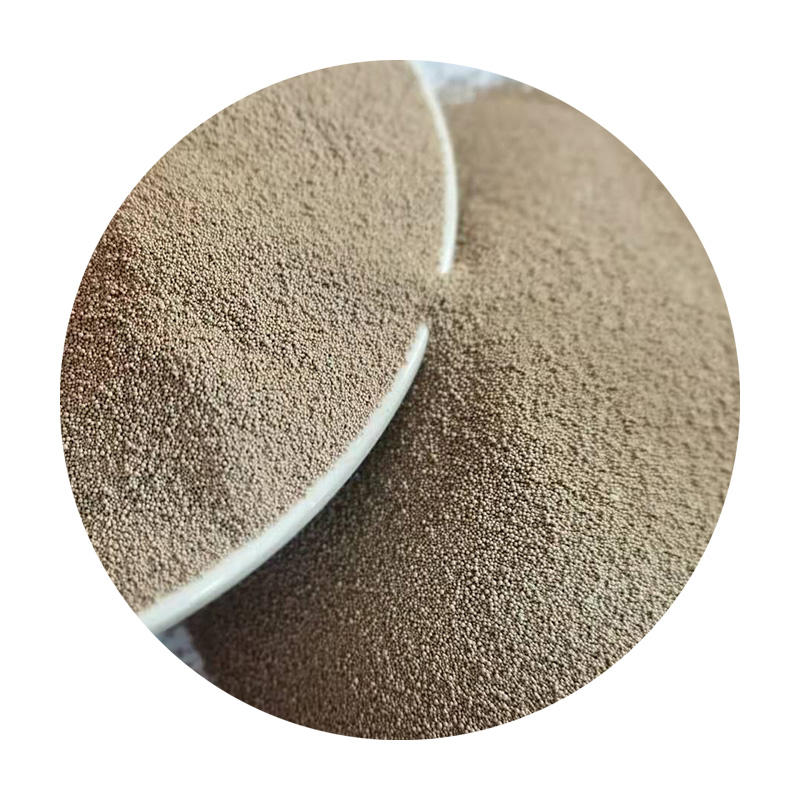
The molding process often involves mixing foundry sand with binders to enhance its cohesiveness and strength
. These binders can be synthetic or natural and are used to create a stable mold that can endure the pouring of molten metal. The choice of binder significantly influences the quality of the cast and the efficiency of the molding process.Foundry sand is not just a material but also an essential factor in achieving optimal casting performance. The right mixture can lead to improved surface finishes, reduced scrap rates, and increased production efficiency. Additionally, the use of reclaimed foundry sand is gaining traction as foundries seek more sustainable practices. Reclamation processes allow for the recycling of sand from previous castings, thus reducing waste and the need for new raw materials. This sustainable approach not only benefits the environment but also lowers operational costs.
Despite its advantages, the foundry sand industry faces challenges, particularly regarding environmental concerns. The disposal of spent foundry sand can lead to issues if not managed properly, as it may contain pollutants from the metal casting process. Consequently, regulations and best practices are being developed to mitigate these risks and promote the safe use of foundry sand in various applications.
In conclusion, foundry sand remains a critical material in the metal casting industry, vital for producing quality castings with precision and efficiency. As advancements in technology and materials science continue to evolve, the applications and sustainability of foundry sand will likely expand, ensuring its place in future manufacturing processes.
Post time:ກ.ຍ. . 28, 2024 08:43
Next:Exploring the Types of Sand Utilized in Sand Casting Processes