The Differences Between Sand Casting and Permanent Mold Casting
Casting is a fundamental manufacturing process that involves pouring molten material into a mold to create a desired shape. Among various casting methods, sand casting and permanent mold casting are two commonly used techniques, each with its own unique characteristics, advantages, and applications. Understanding the differences between these two processes can help manufacturers choose the right method for their specific needs.
Materials and Mold Composition
One of the primary differences between sand casting and permanent mold casting lies in the materials used for the molds. In sand casting, the mold is made from a mixture of sand, clay, and water, which allows for easy shaping and flexibility. This type of mold is typically single-use and can be formed into almost any shape, making it suitable for intricate designs. On the other hand, permanent mold casting utilizes molds made from metal, such as iron or steel. These molds are designed for multiple uses, providing greater durability and producing more consistent results over time.
Casting Process
The casting process also varies significantly between the two methods. Sand casting involves creating a mold by compacting sand around a pattern, which is then removed to leave a cavity for the molten metal. Once the mold is prepared, the molten metal is poured in. This process allows for a wide range of sizes and shapes but can take longer to prepare the mold compared to permanent mold casting.
In contrast, permanent mold casting operates on a different principle. The metal mold used in this method is pre-heated, and molten metal is poured directly into it. The use of metal molds allows for better heat retention and faster solidification of the cast material, resulting in shorter cycle times. This method is particularly advantageous for producing large quantities of smaller parts with high precision.
Surface Finish and Detail
difference between sand casting and permanent mold casting
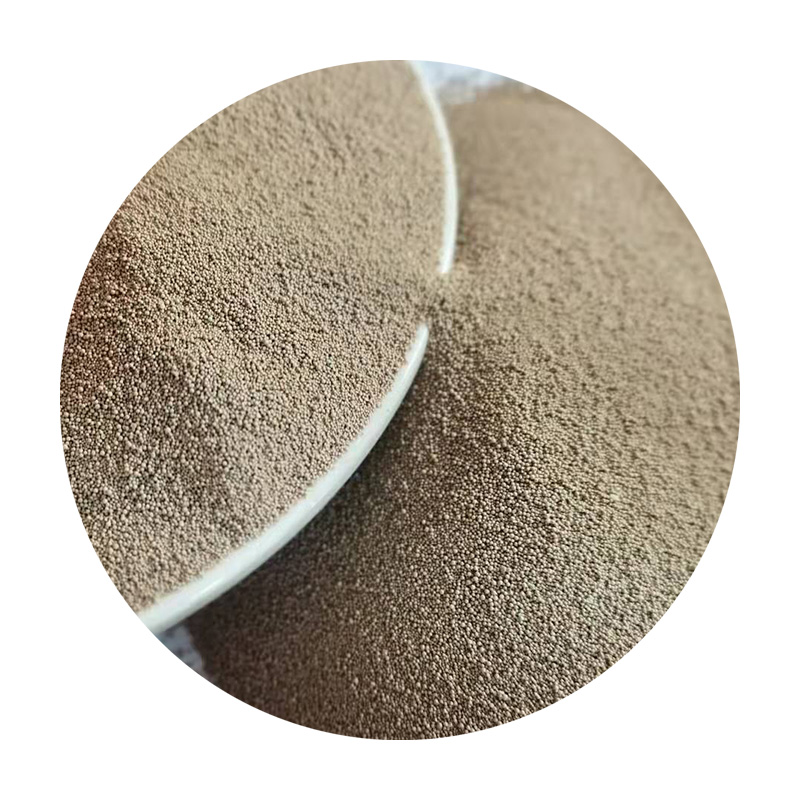
Another critical difference is the level of detail and surface finish that each method can achieve. Sand casting typically produces a rougher surface finish due to the nature of the sand used in the mold, which may require additional machining or finishing steps. However, the flexibility of the sand mold allows for the creation of complex geometries that might be challenging in other casting methods.
Permanent mold casting, on the other hand, tends to yield a smoother surface finish and higher dimensional accuracy. The metallic nature of the mold results in a finer detail and allows for tighter tolerances. This makes permanent mold casting particularly appealing for applications where aesthetics and precision are essential.
Cost and Production Volume
Cost considerations also differentiate the two methods. Sand casting is generally more cost-effective for low-volume production runs due to its relatively simple setup and processing. However, the costs can accumulate with higher production volumes because of the time required to create new molds.
Conversely, permanent mold casting is more economical for high-volume production. Although the initial costs for mold creation are higher due to the enduring materials used, the longevity of the molds and the reduced cycle times lead to lower per-part costs when producing large quantities.
Applications
Finally, the two methods cater to different applications within the manufacturing industry. Sand casting is widely used for large parts such as automotive engine blocks, pipes, and sculptures, where customization is critical. In contrast, permanent mold casting is commonly employed in the production of smaller components, such as transmission cases and brackets, where precision and repeatability are crucial.
In conclusion, both sand casting and permanent mold casting have their unique advantages and applications. The choice between these two methods hinges on factors such as production volume, desired surface finish, material properties, and cost considerations. By understanding their differences, manufacturers can make informed decisions to optimize their production processes.
Post time:ທ.ວ. . 30, 2024 23:21
Next:what is sand casting used for