The Convergence of 3D Printing and Sand Casting A Revolutionary Approach in Manufacturing
In recent years, the manufacturing industry has witnessed significant advancements due to the integration of modern technologies. Among these, 3D printing and sand casting have emerged as powerful methods that, when combined, can transform traditional manufacturing processes. This synergistic relationship not only enhances production efficiency but also opens new avenues for innovation and design flexibility.
3D printing, or additive manufacturing, is a process where digital models are transformed into three-dimensional objects layer by layer. This technology offers numerous advantages, including rapid prototyping, reduced material waste, and the ability to create complex geometries that would be impossible using conventional methods. On the other hand, sand casting is one of the oldest metal casting techniques, involving creating a mold from sand and pouring molten metal into it to form intricate metal parts.
The Convergence of 3D Printing and Sand Casting A Revolutionary Approach in Manufacturing
Moreover, the combination of these technologies allows for designs that were previously infeasible. With 3D printing, complex internal cooling channels or lightweight lattice structures can be incorporated into the mold design. This capacity not only enhances product performance but also leads to weight savings in the final cast component, making it suitable for industries such as aerospace and automotive, where weight reduction is critical.
3d printer sand casting
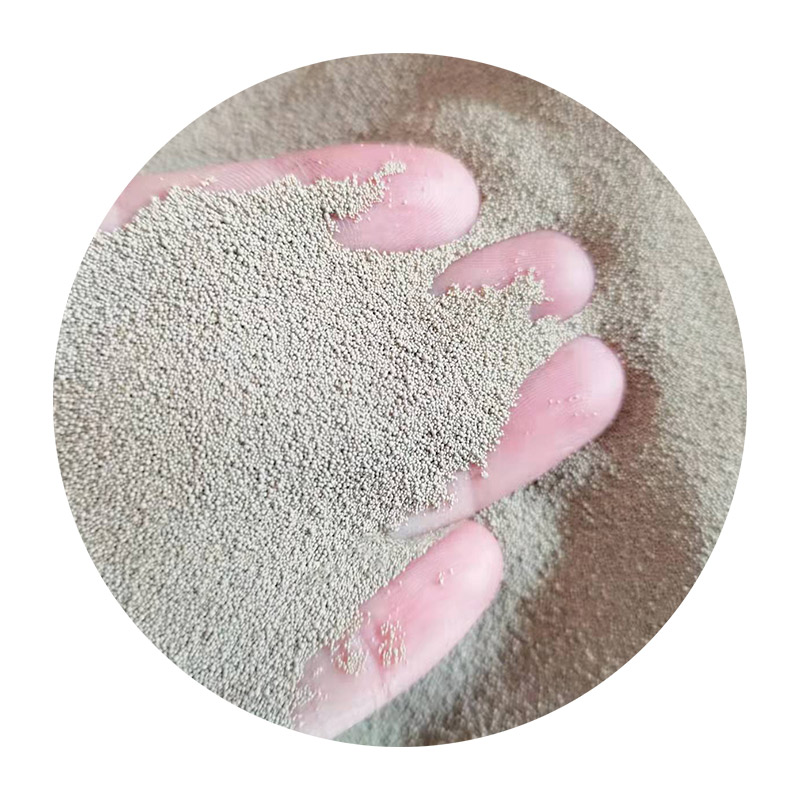
Additionally, the precision of 3D printing ensures that the molds produced are highly accurate, resulting in less rework and waste during the casting process. This level of precision is especially essential when dealing with high-value materials and components, as it increases the overall yield and reduces production costs.
Another significant advantage of combining 3D printing with sand casting is the potential for sustainability. Traditional sand casting often leads to a substantial amount of waste material. However, by employing 3D printing techniques, manufacturers can optimize the mold design to minimize the quantity of sand required, along with reducing the energy consumption associated with the casting process.
Despite these advantages, there are challenges to overcome. The cost of 3D printing equipment and materials can be high, and there might be a learning curve involved for manufacturers transitioning to this hybrid approach. Yet, as technology continues to advance, these barriers are likely to diminish.
In conclusion, the fusion of 3D printing and sand casting presents a transformative opportunity for the manufacturing sector. By leveraging the strengths of both methods, manufacturers can achieve greater efficiency, customization, and sustainability. As industries increasingly seek innovative solutions to meet the demands of modern production, this convergence is set to play a pivotal role in shaping the future of manufacturing. With continued research and development, the full potential of this combination will undoubtedly be realized, paving the way for a new era in industrial production.
Post time:ກ.ຍ. . 28, 2024 17:08
Next:Exploring the Benefits and Techniques of Casting Sand in Metalworking and Foundries