The Art and Science of Sand Casting A Closer Look
Sand casting, also known as sand mold casting, is a metal casting process characterized by using sand as the primary molding material. This method is both ancient and modern, bridging the gap between traditional craftsmanship and contemporary manufacturing techniques. With roots dating back thousands of years, sand casting remains a vital fabrication technique used across various industries today, from automotive to aerospace.
The Sand Casting Process
The sand casting process begins with creating a pattern, which is a replica of the final product. Patterns can be crafted from different materials, including wood, metal, or plastic, and they are designed to produce a mold cavity that reflects the desired dimensions of the final item. The pattern is typically slightly oversized to accommodate the shrinkage of the metal upon cooling.
Once the pattern is prepared, it is used to create a mold. This involves placing the pattern in a molding box and surrounding it with a sand mixture. The sand used in casting is usually a combination of silica sand, a bonding agent (typically clay), and water, which helps bind the grains together. The mold is formed by compacting the sand around the pattern, creating a cavity that mirrors the shape of the pattern.
After the mold is formed and the pattern removed, it is time for pouring. Molten metal, which has been heated to its liquid state, is poured into the mold cavity through a system of channels designed to control the flow and prevent defects. The metal fills the mold, taking on the shape of the cavity created by the pattern.
The cooling process begins as the molten metal gradually solidifies. The cooling time varies depending on the type of metal being cast and the dimensions of the object. Once the metal has cooled and solidified completely, the mold is broken away, revealing the cast product. The final steps involve cleaning and finishing the cast piece, which may include removing any excess material, smoothing rough edges, and conducting inspections to ensure the quality of the casting.
Advantages of Sand Casting
youtube sand casting
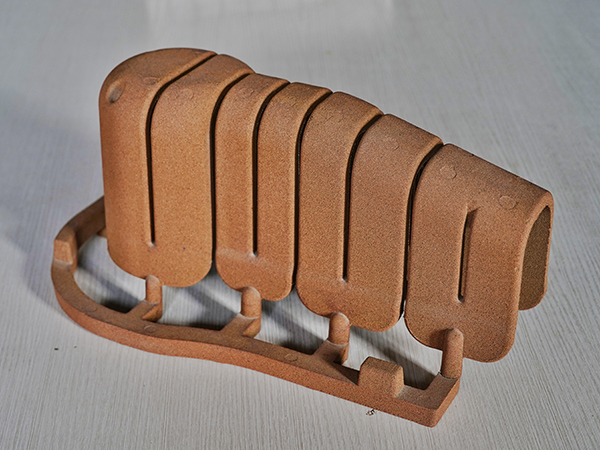
One of the primary advantages of sand casting is its versatility. This method can accommodate various metals, including aluminum, iron, and magnesium, allowing for the production of complex shapes that would be difficult or impossible to achieve with other methods. Furthermore, sand molds can be reused multiple times, making this process economically viable for both small runs and large productions.
Another significant benefit of sand casting is the ability to produce large parts. Many industries rely on sand casting for components that can weigh several tons, such as engine blocks or large industrial machinery parts. The flexibility of the sand casting process supports various production scales, from one-off prototypes to mass manufacturing, catering to diverse industrial needs.
Challenges and Considerations
Despite its many advantages, sand casting is not without challenges. The process can be susceptible to defects like sand inclusion, gas porosity, or dimensional inaccuracies. These issues can arise from factors such as improper mold preparation, inadequate pouring practices, or failure to properly control cooling rates.
Additionally, while the initial setup for sand casting may be relatively low-cost, high-quality production often requires skilled operators and precise control over the process. Innovations in technology, including computer-aided design (CAD) and advanced simulation techniques, are increasingly being employed to enhance the accuracy and efficiency of sand casting, significantly reducing the occurrence of defects.
Conclusion
Sand casting is a fascinating blend of art and science, embodying centuries of evolution in manufacturing. Its ability to produce intricate designs, coupled with a diverse range of metal options, makes it an enduring choice in modern production. While challenges remain, ongoing advancements in technology will continue to refine the sand casting process, ensuring its relevance and utility in various industries. As we look to the future, understanding the intricacies of sand casting not only preserves a crucial aspect of our industrial heritage but also fosters innovation in modern manufacturing practices.
Post time:Dec . 13, 2024 01:36
Next:3d print sand casting