The Difference Between Die Casting and Sand Casting
When it comes to metal casting processes, die casting and sand casting are two of the most commonly used techniques in the manufacturing industry. Both methods are utilized to produce metal parts, but they differ significantly in terms of materials, processes, and applications. Understanding these differences is crucial for manufacturers when choosing the appropriate method for their projects.
Process Overview
Die casting is a process that involves forcing molten metal into a mold cavity under high pressure. The molds used in die casting are typically made from hardened steel and are designed to produce precise, complex shapes with smooth surfaces. The high-pressure injection helps eliminate porosity in the finished product, resulting in dense, high-quality components. Die casting is especially effective for manufacturing large quantities of parts quickly, often in production runs of thousands or even millions.
On the other hand, sand casting is a more traditional method that uses a mixture of sand and a binder to create a mold. This process involves creating a pattern of the desired part, which is then imbedded in the sand mixture. Once the mold is formed and the pattern removed, molten metal is poured into the cavity. Sand casting is generally slower and less precise than die casting, leading to rougher finishes and a higher likelihood of defects. However, it is more versatile in handling a wide range of metals, including iron, aluminum, and copper alloys.
Material Suitability
Die casting is primarily suited for non-ferrous metals such as aluminum, zinc, and magnesium. The high-pressure process used in die casting is ideal for these metals, which can flow easily into the mold and solidify rapidly. The ability to achieve thin-walled sections also makes die casting perfect for lightweight components needed in automotive and electronics industries.
Conversely, sand casting can accommodate ferrous and non-ferrous metals alike. It is often chosen for casting larger components or those that require specific metal types, such as cast iron and steel. Sand casting's flexibility also permits modifications and adaptations to the mold, making it easier to produce intricate designs, albeit with less consistency than die casting.
difference between die casting and sand casting
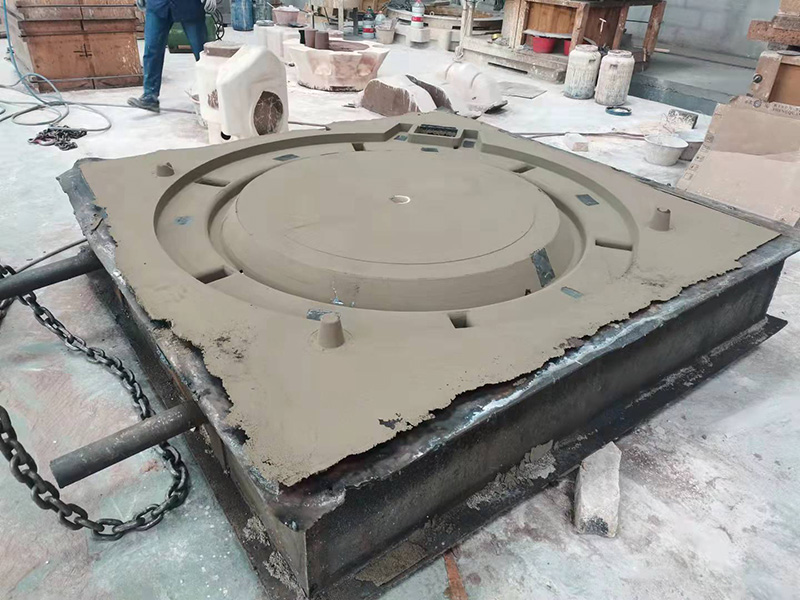
Surface Finish and Tolerances
The surface finish and tolerances achieved through die casting are generally superior to those obtained through sand casting. Die cast parts typically require little to no machining due to their high dimensional accuracy and smooth surface finish. This makes them ideal for applications where aesthetics and precision are critical, such as in consumer electronics and high-performance vehicles.
In contrast, sand cast parts usually exhibit a rougher texture, often necessitating additional machining to meet tighter tolerances and smoother finishes. Sand casting's surface imperfections can also lead to variances in the final product's performance, making it less suitable for applications requiring high precision.
Production Volume and Cost
Die casting is economically advantageous for large production volumes, as the initial setup costs for molds can be high. Once the molds are created, the cost per part significantly decreases with increased volume, making it an efficient choice for mass production. However, for low-volume production, the upfront investment in die casting tools may not be cost-effective.
Sand casting, in contrast, offers lower initial costs and is more suited for lower volume production runs. The simplicity of the mold-making process allows manufacturers to produce parts without extensive setup costs, thus being an attractive option for custom jobs or prototyping.
Conclusion
In summary, die casting and sand casting are distinct processes suited for varying manufacturing needs. Die casting excels in high production volumes and tight tolerances, making it ideal for intricate components of consumer products and automotive parts. Sand casting, with its versatility and lower setup costs, remains favorable for custom parts and larger components. Ultimately, the choice between these two methods hinges on project specifications, material requirements, production volume, and budget constraints. Understanding their differences enables manufacturers to select the best method to meet their needs effectively.
Post time:Dec . 19, 2024 13:05
Next:sand casting factory