What Type of Sand is Used for Sand Casting?
Sand casting is one of the oldest and most widely used metal casting processes. In this method, a mold is formed from sand, which is then used to shape molten metal into the desired object. The type of sand used in sand casting plays a crucial role in determining the quality of the final product. This article will explore the types of sand commonly used in sand casting, their properties, and why they are suitable for this process.
Types of Sand Used in Sand Casting
1. Silica Sand The most commonly used sand in sand casting is silica sand (SiO2). Its high melting point (around 1,600 degrees Celsius) makes it exceptionally resistant to heat. Silica sand grains have a suitable shape and size, which allows for easy compaction and creates a mold with excellent detail and surface finish. Additionally, silica sand is readily available and economical, making it the primary choice for many foundries.
2. Green Sand Green sand is a mixture of silica sand, clay, and water. This type of sand is called green because it is used in its moist state. The clay serves as a bonding agent and gives the mold its strength and ability to hold shape when the molten metal is poured in. The water content helps enhance the mold's strength while ensuring it does not dry out too quickly. Green sand is known for creating excellent surface finishes and is widely used in foundries for ferrous metals.
3. Resin Sand Resin sand, or chemically bonded sand, uses synthetic resins as a binding agent instead of clay. This type of sand provides superior mold strength and stability, which is extremely beneficial for complex shapes and intricate designs. Resin sand molds are often used for non-ferrous alloys and high-quality castings due to their excellent thermal and dimensional stability. While it tends to be more expensive than traditional green sand, the quality of the final product often justifies the added cost.
what type of sand is used for sand casting
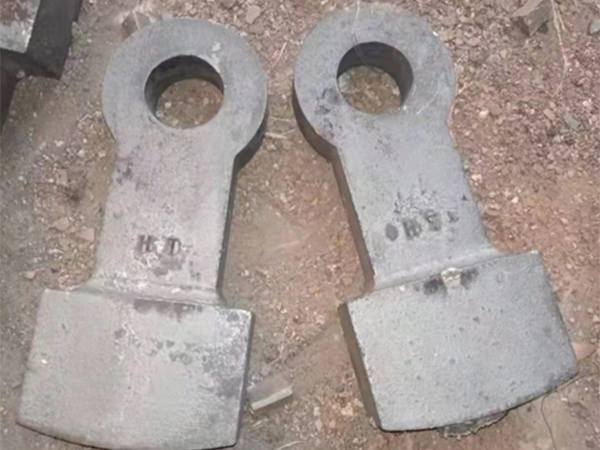
4. Shell Sand Shell sand, or shell mold casting sand, is made from a mixture of fine sand and a thermosetting resin. This mixture is applied to a heated pattern, causing the resin to bond the sand into a shell-like mold. This process results in molds that have high dimensional accuracy, fine surface finishes, and excellent thermal resistance. Shell sand is ideal for producing small-to-medium-sized parts with complex geometries, including those required in the automotive and aerospace industries.
5. Olive Sand Olive sand is a type of clay sand that contains significant amounts of olivine, a naturally occurring silicate mineral. This type of sand is particularly effective for casting high melting point alloys, such as titanium and nickel-based superalloys. Olive sand has a good thermal stability, can withstand high temperatures, and provides a smooth surface finish.
Conclusion
The choice of sand in the sand casting process is paramount to achieving high-quality castings. Each type of sand offers unique properties that contribute to mold strength, thermal resistance, detail retention, and surface finish. While silica sand remains the most widely used option due to its availability and cost-effectiveness, alternatives such as green sand, resin sand, shell sand, and olive sand exist to meet specific requirements of different applications.
When selecting the appropriate sand type, it is essential to consider factors such as the characteristics of the metal being cast, the complexity of the design, and the desired surface finish. Understanding these aspects can significantly influence the casting process's efficiency and effectiveness, ultimately leading to the successful production of high-quality metal parts.
Post time:Nov . 08, 2024 17:10
Next:3d printing for sand casting