Physical Properties of Foundry Sand
Foundry sand is a critical material used in the metal casting process, serving as a mold material to form various shapes and structures. Its effectiveness largely derives from its physical properties, which must be carefully regulated to ensure that the casting process is efficient and produces high-quality products. Understanding these properties is fundamental for foundries that aim to optimize their operations and improve the performance of their molds.
Grain Size and Distribution
One of the primary physical properties of foundry sand is its grain size and distribution. The size of sand grains plays a significant role in determining the permeability of the mold, which is essential for the escape of gases generated during the casting process. Typically, foundry sand is composed of silica, and the ideal grain size ranges from 0.1 mm to 0.5 mm. A well-graded sand will have a variety of grain sizes that contribute to good compaction and strength while allowing adequate airflow. Poorly graded sand can lead to defects such as blowholes, which can compromise the integrity of the casted metal.
Shape and Sphericity
The shape of the sand grains also significantly impacts the mold's properties. Ideally, foundry sand should have a rounded or sub-rounded shape, which enhances its flowability and compaction characteristics. Angular grains can create interlocking structures that hinder the packing density of the mold, reducing its strength and increasing the likelihood of defects during casting. Sphericity, the measure of how closely the shape of a grain resembles a sphere, is another important aspect. Higher sphericity indicates better flowability and mold filling capabilities, contributing to smoother surfaces on the final castings.
Moisture Content
physical properties of foundry sand
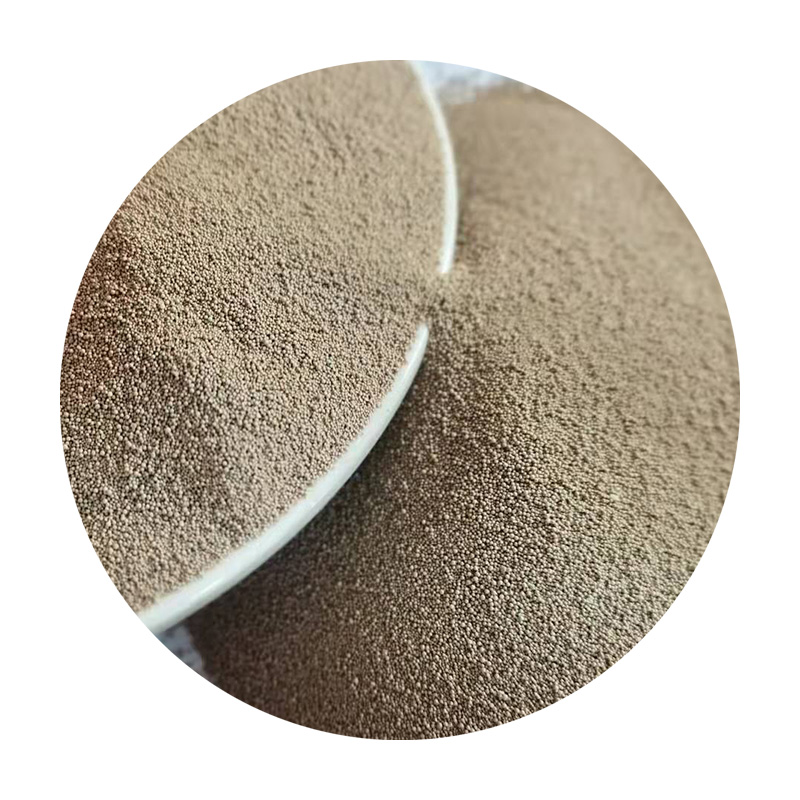
The moisture content in foundry sand is crucial for achieving the desired properties of the mold. Sand typically contains a certain amount of water, which aids in binding the grains together without compromising permeability. However, excessive moisture can lead to swelling and decreased sand strength, while insufficient moisture can result in poor mold integrity and increased gas emissions. Maintaining an optimal moisture level (usually between 2% to 6%) is key for ensuring that the mold has adequate strength while allowing gases to escape effectively.
Thermal Conductivity
Thermal conductivity is another vital physical property. Foundry sand must possess the ability to withstand high temperatures during metal pouring without degrading. Good thermal stability prevents the sand from breaking down, which can impact the surface finish of the casting. The ability of the sand to transfer heat efficiently also plays a role in controlling the cooling rate of the metal, which is crucial in obtaining desired mechanical properties in the final product.
Strength and Resilience
The strength and resilience of foundry sand are essential for maintaining the mold's integrity under the pressure of pouring molten metal. The sand must withstand mechanical stress and thermal shock without collapsing. Its compressive strength is a vital characteristic, influencing how well the mold can hold its shape throughout the casting process. In addition, resilience ensures that if the mold is subjected to sudden changes in temperature or pressure, it can return to its original form without permanent deformation.
Conclusion
In summary, the physical properties of foundry sand—grain size and distribution, shape and sphericity, moisture content, thermal conductivity, and strength—are critical factors that influence the quality and efficiency of the metal casting process. Understanding and optimizing these properties can lead to better mold performance, reduced casting defects, and ultimately, superior quality in the final metal products. Foundries that invest time and resources into evaluating and improving the characteristics of their sand will likely see enhanced production rates and reduced scrap rates, leading to overall operational success.
Post time:Nov . 27, 2024 10:17
Next:Benefits and Drawbacks of Sand Casting Processes for Manufacturing