Types of Sand Casting Processes
Sand casting, a century-old process, remains one of the most widely utilized methods in metal casting due to its versatility, cost-effectiveness, and capability to produce large and complex parts. This article will explore the various types of sand casting processes, highlighting their unique characteristics and applications.
1. Green Sand Casting
Green sand casting is the most traditional and commonly used method in the sand casting-based production. It utilizes a mixture of sand, clay, and water to create molds. The term green refers to the fact that the mold is not dried when molten metal is poured into it. This method offers excellent flexibility and can produce intricate shapes. Additionally, green sand is easy to work with and offers good thermal conductivity. However, it may not be suitable for extremely high-precision parts due to the potential for deformation during the cooling process. Green sand casting is often seen in the automotive and aerospace industries, where it is used to manufacture components like engine blocks and brackets.
Unlike green sand casting, dry sand casting employs a mold that is dried in an oven before pouring the metal. This process enhances the strength and dimensional accuracy of the mold, allowing for higher precision in the final product. Dry sand molds can withstand higher temperatures, making them suitable for casting metals with higher melting points, such as steel and iron. This method is particularly beneficial for high-volume production runs where consistency and precision are crucial. The automotive and machinery sectors frequently utilize dry sand casting to produce complex shapes that demand high-performance standards.
3. Air Set Sand Casting
types of sand casting process
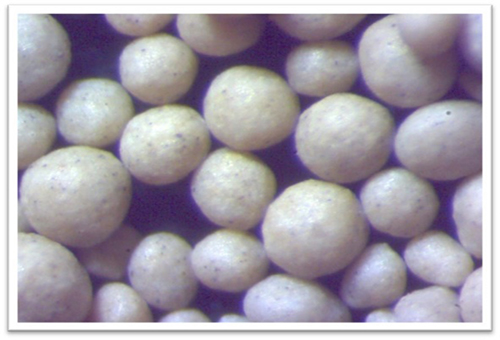
Air set sand casting differs from both green and dry sand casting methods as it uses a resin binder to solidify the mixture instead of clay and water. This process allows the sand to harden at room temperature, creating durable molds capable of reproducing intricate designs. One of the primary advantages of air set sand casting is the elimination of moisture, which reduces the risk of defects associated with steam or gas evolution during the casting process. This method achieves superior surface finish and dimensional accuracy, making it ideal for applications in the aerospace, medical, and high-end consumer goods industries.
4. Shell Mold Casting
Shell mold casting is a variation of sand casting that utilizes a thin shell of sand, bonded by a thermosetting resin, to form the mold. This technique results in precise dimensions and a smooth surface finish, which can reduce or eliminate the need for further machining. Shell molds can be produced quickly, enhancing turnaround times for manufacturing. This method is often used for small to medium-sized components where high accuracy and a good surface finish are required, such as in the production of complex automotive parts and intricate tools.
5. Investment Casting (Lost-Wax Process)
Though not strictly a sand casting process, investment casting is another method that involves the pouring of metal into a mold that has been formed using a wax model. Once the mold is established, the wax is melted away, leaving a cavity into which molten metal is poured. This process allows for extreme precision and intricate details, making it suitable for components that require strict tolerances. Investment casting is widely used in industries such as aerospace, medical devices, and jewelry manufacturing.
Conclusion
In conclusion, the variety of sand casting processes available provides options tailored to different manufacturing needs. From the traditional green sand casting to the specialized investment casting, each method has its strengths and applications. The ongoing evolution of sand casting technologies continues to expand the possibilities for engineers and manufacturers, ensuring its relevance in modern production. Understanding these methods allows for better decision-making when selecting the appropriate casting technique for specific projects, contributing to improved efficiency and quality in metal fabrication.
Post time:تشرینی دووەم . 08, 2024 11:23
Next:Exploring Techniques for Low Volume Sand Casting in Metal Fabrication