The Steps of Sand Casting
Sand casting is a widely used manufacturing process that allows for the creation of intricate metal parts and components. It is favored due to its flexibility, cost-effectiveness, and ability to produce complex shapes. In this article, we will explore the detailed steps involved in sand casting, from preparation through to finishing.
1. Pattern Making
The first step in the sand casting process is the creation of a pattern. The pattern is a replica of the final product and is usually made from materials like wood, metal, or plastic. Patterns can be solid or hollow, based on the requirements of the final casting. The choice of material for the pattern influence not only the cost but also the durability and the precision of the final product. The pattern is designed with allowances for shrinkage, which occurs when the metal cools and solidifies.
2. Prepare the Molding Sand
Once the pattern is ready, the next step involves preparing the molding sand. Sand casting sand is typically a mixture of silica sand, clay, and water. The sand must have the appropriate characteristics for successful mold creation, including good permeability, plasticity, and the ability to retain its shape. The preparation of molding sand includes mixing raw materials, ensuring the right moisture content, and achieving the desired grain size.
3
. Flask AssemblyThe next phase involves assembling the flask, which is a container that holds the molding sand. The flask consists of two halves the cope (top part) and the drag (bottom part). The pattern is placed inside the drag half of the flask, and sand is packed around it to create a mold. When the mold is complete, the cope is placed on top.
4. Molding
The molding process begins with the packing of sand around the pattern. A sufficient amount of sand must be tightly packed to ensure it can hold its shape when the pattern is removed. Once the sand is in place, the pattern is carefully removed, leaving a cavity that corresponds to the shape of the final part. The two halves of the mold are then joined together, ensuring they align correctly and creating the necessary passages for pouring the molten metal.
steps of sand casting
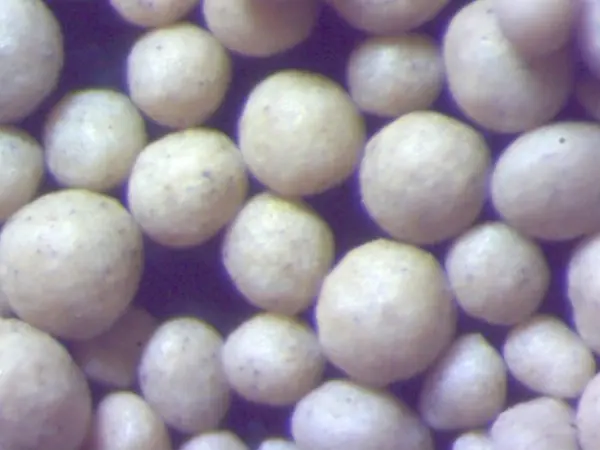
5. Pouring the Molten Metal
After the mold is prepared, the next step is to heat the desired metal until it reaches a molten state. Common metals used in sand casting include aluminum, iron, bronze, and brass. Once the metal is molten, it is poured into the mold through the gating system, which includes sprues and runners that direct the flow of metal. It’s crucial to pour the metal at a steady pace to prevent trapping air or creating turbulence, which could lead to defects in the final casting.
6. Cooling and Solidification
Once the mold is filled, the molten metal begins to cool and solidify. The cooling time varies depending on the size and thickness of the casting being produced. It is important to allow sufficient time for the casting to solidify fully; premature removal from the mold can result in deformities. Generally, solidification occurs from the outside of the mold inwards, and the cooling process needs to be controlled to avoid thermal stress.
7. Mold Removal and Finishing
After the metal has cooled and solidified, the sand mold is broken away to reveal the casting. This is often done by shaking or vibrating the mold, allowing easy disassembly. The casting may have surface imperfections, such as sand residue or rough edges, which require finishing operations. Techniques such as grinding, sandblasting, or machining can be employed to achieve the desired surface finish and dimensional accuracy.
8. Quality Control
Finally, the last step of the sand casting process is quality control. The finished parts are inspected for consistency, dimension accuracy, and compliance with specifications. Quality control can involve visual inspections, dimensional checks, or non-destructive testing methods to identify internal defects. Ensuring quality at this stage is critical, as it guarantees that the final product meets the requirements for its intended application.
Conclusion
Sand casting is a versatile and effective method for producing metal parts with intricate shapes. The steps involved, from pattern making to quality control, highlight the complexity and craftsmanship required in this manufacturing process. As technology advances, the sand casting process continues to evolve, employing new techniques and materials to improve efficiency and quality in metal casting. Whether for small-scale projects or large industrial applications, sand casting remains a cornerstone of metalworking and manufacturing industries.
Post time:تشرینی یەکەم . 13, 2024 12:03
Next:High-Quality Casting Sand for Precision Metal Fabrication Applications