Steps in Sand Casting A Comprehensive Overview
Sand casting, one of the oldest and most versatile metal casting processes, has evolved over centuries to become a reliable method for producing complex metal parts. Commonly used in industries such as automotive, aerospace, and manufacturing, sand casting offers several advantages, including cost-effectiveness, the ability to create large components, and compatibility with various metals. This article delves into the essential steps involved in the sand casting process, highlighting its significance and the attention to detail required at each stage.
Step 1 Pattern Making
The first step in sand casting is the creation of a pattern. A pattern is a replica of the final product that is made out of materials such as wood, metal, or plastic. It is essential that the pattern is slightly larger than the desired final product to account for metal shrinkage during cooling. The pattern can be a single piece or a series of pieces, depending on the complexity of the design. Often, patterns include additional features, such as locating pins or runners, to facilitate the casting process.
Step 2 Preparing the Mould
Once the pattern is prepared, it is used to create the mould. This is done by placing the pattern in a box (known as a flask) and packing it with a mixture of sand and a binding agent, typically clay or resin. This moulding sand must be well-graded to ensure that it holds shape when compressed around the pattern. After packing, the sand is compacted using mechanical or manual tools to achieve the required hardness and stability.
Step 3 Creating the Cores
For parts with hollow sections, cores are necessary. Cores are made from a similar sand mixture and are designed to create internal cavities within the casting. The cores need to be strategically placed within the mould and secured, as they will later hold molten metal in the desired shape.
Step 4 Assembling the Mould
Once the sand has been properly compacted around the pattern and the cores are set in place, the mould halves are assembled. This involves carefully removing the pattern and ensuring that the mould halves fit together perfectly to eliminate any gaps. Any additional features, such as gates and risers, which allow molten metal to enter the mould efficiently and manage gas escape, are also formed at this stage.
Step 5 Melting the Metal
steps in sand casting
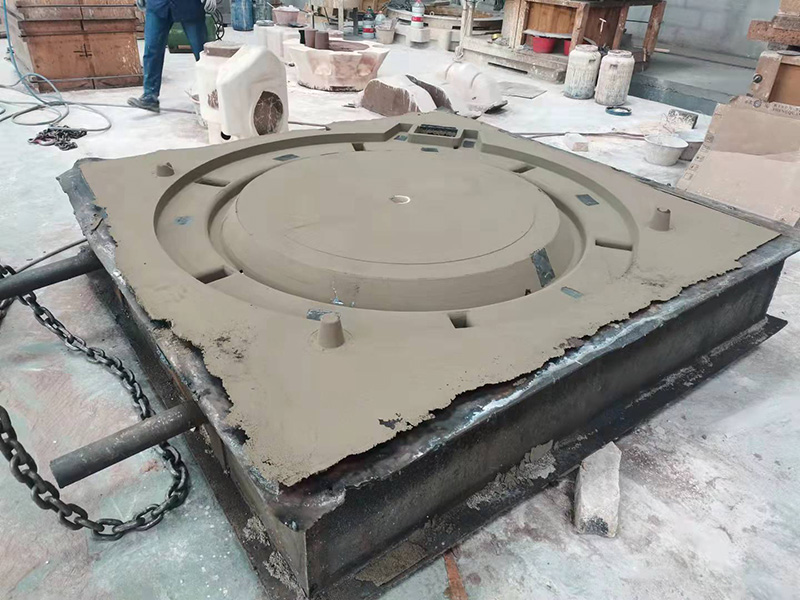
With the mould ready, the next step is to melt the metal that will be cast. This is usually done in a furnace, where materials such as aluminum, iron, or bronze are heated until they reach a liquid state. The choice of metal depends on the desired final properties of the part being produced.
Step 6 Pouring
When the metal is molten, it is poured into the prepared mould. This must be done carefully to avoid spillage, air inclusions, and other defects. Proper pouring techniques are vital to ensure that the metal fills all areas of the mould and that the temperature remains consistent to avoid premature solidification.
Step 7 Cooling and Solidification
After pouring, the molten metal is allowed to cool and solidify within the mould. The time required for this process varies depending on the metal type and the thickness of the section being cast. Proper cooling is crucial to achieving the desired mechanical properties and ensuring no internal stresses develop in the final product.
Step 8 Mould Removal
Once the metal has completely solidified, the mould is broken apart to reveal the casting. This process may involve shaking or vibrating the mould to allow for easy removal of the casting. Care must be taken to avoid damaging the intricate features of the cast part.
Step 9 Finishing
The final step in the sand casting process is finishing. This may include removing any excess sand, trimming, grinding, or machining to achieve the desired dimensions and surface finish. Additional treatments such as heat treatment may also be applied to enhance the physical properties of the metal.
Conclusion
The sand casting process is structured and multifaceted, offering a unique blend of simplicity and complexity. Understanding each step in the process is crucial for achieving high-quality castings that meet stringent industry standards. From pattern making to finishing, meticulous attention is necessary at every stage to ensure that the final product is robust, precise, and fit for its intended application. As industries continue to innovate, sand casting remains a preferred method for producing a wide range of metal components, demonstrating its enduring relevance in modern manufacturing.
Post time:تشرینی یەکەم . 13, 2024 12:55
Next:Crafting Sand for Foundry Applications and Its Importance in Metal Casting Industry