Sand Preparation in Foundry An Essential Process for Quality Casting
The foundry industry relies heavily on the preparation of sand for casting processes. Sand preparation serves as a crucial step in ensuring the quality and efficiency of the casting operation. The key to successful metal casting lies in the properties of the sand, its mixture with binders, and the overall preparation techniques. This article delves into the importance of sand preparation, the types of sand used, the preparation process, and the innovations shaping the future of this vital step in the foundry.
Importance of Sand Preparation
Sand preparation is fundamental because it directly influences the final quality of castings. The characteristics of the prepared sand—such as its strength, permeability, and ability to retain moisture—play a significant role in the quality and precision of the cast product. Properly prepared sand ensures that molds can withstand the molten metal's pressure and heat, preventing defects in the casting process. Inadequate sand preparation can lead to a range of issues, including poor surface finish, dimensional inaccuracies, and internal defects in the final product.
Types of Sand Used in Foundries
Several types of sand are used in the foundry industry, each with unique properties tailored to specific casting needs. The most commonly used sands are
1. Silica Sand This is the most prevalent type due to its excellent properties, including high melting point and chemical stability. Silica sand is ideal for most metal casting processes.
2. Zircon Sand Known for its high thermal stability and low thermal expansion, zircon sand is often used in the casting of high-temperature metals.
3. Chromite Sand This type is favored for its high melting point and ability to resist heat distortion. It is particularly beneficial in the production of steel castings.
4. Nigerian Sand Often referred to as molding sand, it possesses a suitable grain shape and size, making it adaptable to various casting processes.
Each sand type requires specific preparation methods to enhance its performance in foundry applications.
Sand Preparation Process
sand preparation in foundry
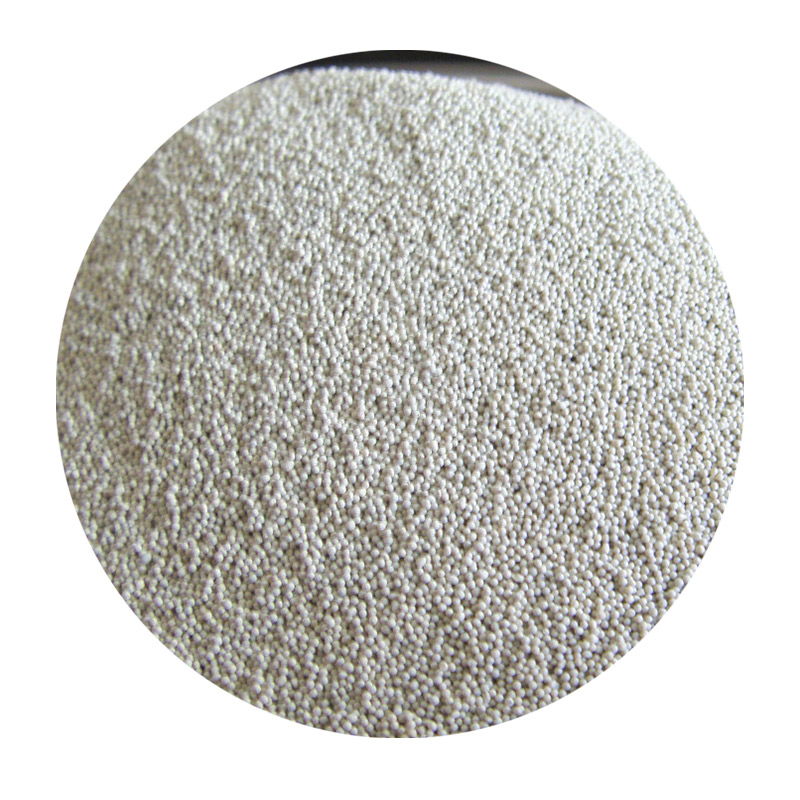
The sand preparation process encompasses several critical steps
1. Sand Reclamation Used sand from previous casting cycles is reclaimed to reduce waste and lower costs. It involves breaking down the used sand and separating impurities.
2. Sand Mixing Fresh and reclaimed sand are mixed in specific proportions. Binders, which help the sand maintain its shape during casting, are added to this mixture. The selection of binders depends on the casting requirements.
3. Moisture Control Maintaining the right moisture content is crucial for mold strength. Excess moisture can lead to mold collapse, while insufficient moisture may cause lack of adhesion and cracking.
4. Sand Testing Regular testing of sand is essential to ensure that its properties remain consistent. Various tests can be conducted to assess grain size, permeability, and bonding strength.
5. Final Preparation After testing, the sand is often screened and conditioned to ensure uniformity and optimal performance during the molding and casting processes.
Innovations in Sand Preparation
The foundry industry is witnessing a shift towards more sustainable and efficient sand preparation methods. Innovations in technology, such as automatic sand mixers and advanced sand reclamation systems, are streamlining the preparation process. The use of environmentally friendly binders is also on the rise, reducing the harmful emissions during casting.
Additionally, digital technologies and data analytics are being implemented to monitor sand properties in real-time, allowing for more precise adjustments to the preparation process. This not only improves the quality of the molds but also enhances efficiency and reduces waste.
Conclusion
In summary, sand preparation plays a pivotal role in the foundry industry. Understanding the various types of sand and the preparation process can significantly impact the quality of the final casting. With ongoing innovations and a focus on sustainability, the future of sand preparation in foundries looks promising. By embracing these advancements, foundries can improve their operations and produce higher-quality castings, ultimately driving growth in this essential industry.
Post time:تشرینی دووەم . 27, 2024 08:05
Next:Innovative Techniques in Lost Foam Casting Coating for Enhanced Mold Quality