The sand foundry process, a cornerstone in the manufacturing industry, is crucial for producing metal castings that meet the diverse needs of various sectors, including automotive, aerospace, and machinery. This method utilizes sand as the primary molding material and is favored for its cost-effectiveness, flexibility, and ability to form intricate shapes.
At the heart of the sand foundry process is the creation of a mold. The process begins with a pattern, which is a replica of the final casting. Patterns are typically made from metal, plastic, or wood. The pattern is placed within a mold box, which is then filled with a mixture of sand and a binder material that helps the sand grains adhere to each other. Once the sand is compacted around the pattern, the mold is formed. This compacting can be done manually or with machines, depending on the scale of production and the complexity of the design.
After the mold has been formed, it's time for the pattern to be removed. This is done carefully to avoid damaging the mold. The next step involves creating a cavity where molten metal will be poured. This is achieved by removing the pattern from the mold. At this stage, various techniques are used to ensure that the mold retains its integrity and can withstand the heat and pressure of the molten metal.
The next critical step in the sand foundry process is melting the metal
. This is typically conducted in a furnace, where the metal is heated to its melting point and then poured into the mold created from the sand. The careful management of temperature and timing is essential to ensure that the metal fills the mold completely and evenly, thus preventing defects in the final product.sand foundry process
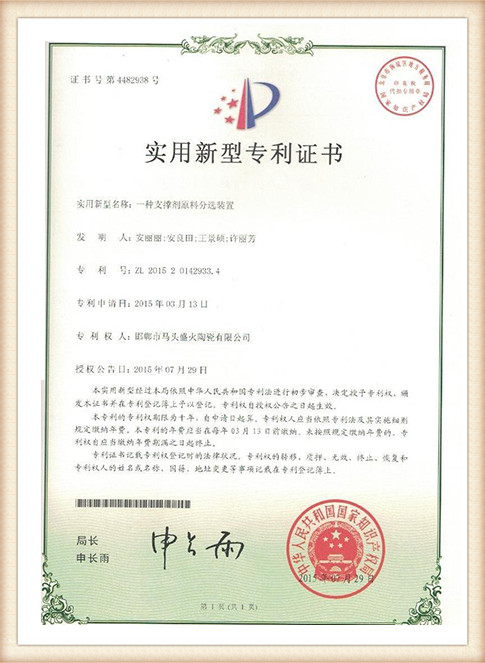
Once the metal has cooled and solidified, the mold is broken apart to retrieve the casting. This process can involve shaking or blowing away the sand that formed the mold. The resulting casting often requires further processing, such as grinding, machining, or polishing, to achieve the desired finish and dimensions.
One of the most significant advantages of the sand foundry process is its versatility. It can accommodate a wide range of metals, including aluminum, iron, and bronze, making it ideal for producing both small and large components. Additionally, advancements in technology, such as 3D printing, are enhancing the sand foundry process, allowing for even greater design complexity and efficiency.
In conclusion, the sand foundry process is an essential manufacturing technique that plays a vital role in producing high-quality metal castings. Its adaptability, efficiency, and capacity for precision make it a preferred choice in many industries, ensuring it remains a fundamental aspect of modern manufacturing.
Post time:ئیلول . 23, 2024 22:09
Next:Exploring the Benefits and Applications of Resin Bound Sand in Modern Construction