Sand for Metal Casting An Essential Element in Foundry Practices
Metal casting is a manufacturing process that has been utilized for centuries, allowing artisans and industrialists alike to create complex shapes and designs. Among the multitude of techniques and materials in this field, sand plays a pivotal role as a molding medium that contributes significantly to the overall quality and efficiency of the casting process. This article explores the importance, types, and preparation of sand used in metal casting.
Importance of Sand in Metal Casting
Sand serves as the primary material in the production of molds, which are critical for shaping molten metal into desired forms. The characteristics of the sand impact the final product's surface finish, dimensional accuracy, and even the mold's ability to withstand high temperatures and pressures. To achieve optimal results in metal casting, it is imperative to select the right type of sand, as well as to understand its properties and behaviors during the casting process.
Types of Sand Used
The most common type of sand used in metal casting is silica sand, primarily due to its abundance and favorable properties. Silica sand provides excellent thermal stability, allowing it to withstand the high temperatures of molten metals. It is also relatively cost-effective and readily available.
However, other types of sand are also employed in specific cases. For example, zircon sand is known for its high melting point and is often used in applications where high-quality surface finishes are required. Similarly, chromite sand can be utilized for ferrous castings due to its low thermal expansion and good resistance to metal penetration.
sand for metal casting
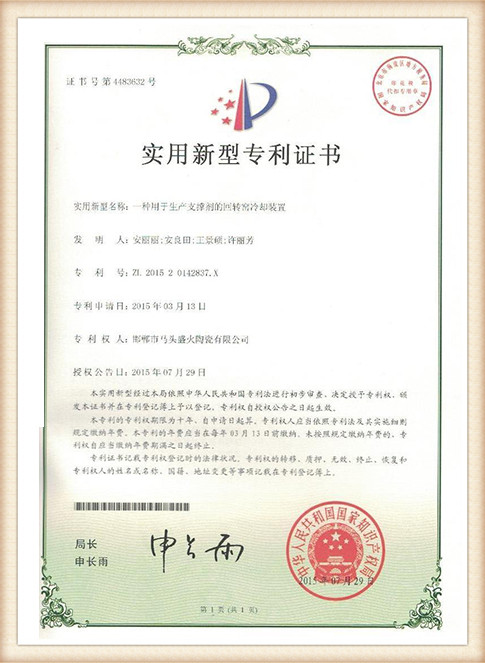
In addition to natural sands, synthetic sands are also gaining popularity. These engineered materials can be tailored to achieve specific physical and chemical properties, allowing for greater control over the casting process.
Preparation of Sand for Molding
The preparation of sand is a crucial step in the casting process. Fresh sand must be carefully mixed with binders and water to achieve the desired consistency. The binder helps to create a cohesive mold that can retain its shape during pouring. Common binders include clay, resin, and clay-bonded systems.
After mixing, sand is often subjected to a process called molding, where it is packed around a pattern to create a mold cavity. The packing density of the sand is vital; too loose can lead to structural weaknesses, while too tight can result in difficulty in removing the pattern.
Additionally, the reclamation of used sand is a common practice in modern foundries, allowing for environmental sustainability and cost-effectiveness. This process involves cleaning and reconditioning the sand for reuse, reducing waste and the need for new materials.
Conclusion
In the world of metal casting, sand serves as more than just a material; it is the foundation upon which quality molds are built. Understanding the types of sand, their properties, and the preparation methods is essential for successful casting operations. As technology evolves and the demand for precision casting increases, the role of sand in metal casting will undoubtedly continue to be a focus of innovation and research, ensuring its place as an indispensable component in the foundry industry.
Post time:تشرینی یەکەم . 06, 2024 06:47
Next:sand casting factory