Understanding Sand Casting An Essential Process in Manufacturing
Sand casting is a widely used metal casting process that involves creating a mold from sand, into which molten metal is poured to create various metal components. This technique is particularly favored in the manufacturing industry for its versatility, cost-effectiveness, and ability to produce complex geometries.
The Sand Casting Process
The sand casting process begins with the creation of a pattern, which is a replica of the object to be cast. Patterns can be made from various materials, including wood, metal, or plastic, depending on the precision and durability required. Once the pattern is ready, it is used to create a mold, typically composed of a mixture of sand and a binding agent, which gives it the necessary strength to hold its shape when the molten metal is poured in.
The mold is formed in two halves, allowing for easy removal of the pattern once the mold is complete. After the pattern is embedded in the sand mixture, the sand is compacted around it. Once the two halves of the mold are assembled, the next step involves creating a cavity within the mold, which will ultimately shape the cast metal component.
Advantages of Sand Casting
One of the primary reasons for the widespread use of sand casting in factories is its affordability. Sand is abundant and inexpensive, leading to lower production costs when compared to other casting methods. Additionally, sand casting allows for the manufacturing of large components, making it an ideal choice for industries such as automotive, aerospace, and heavy machinery.
sand casting factory
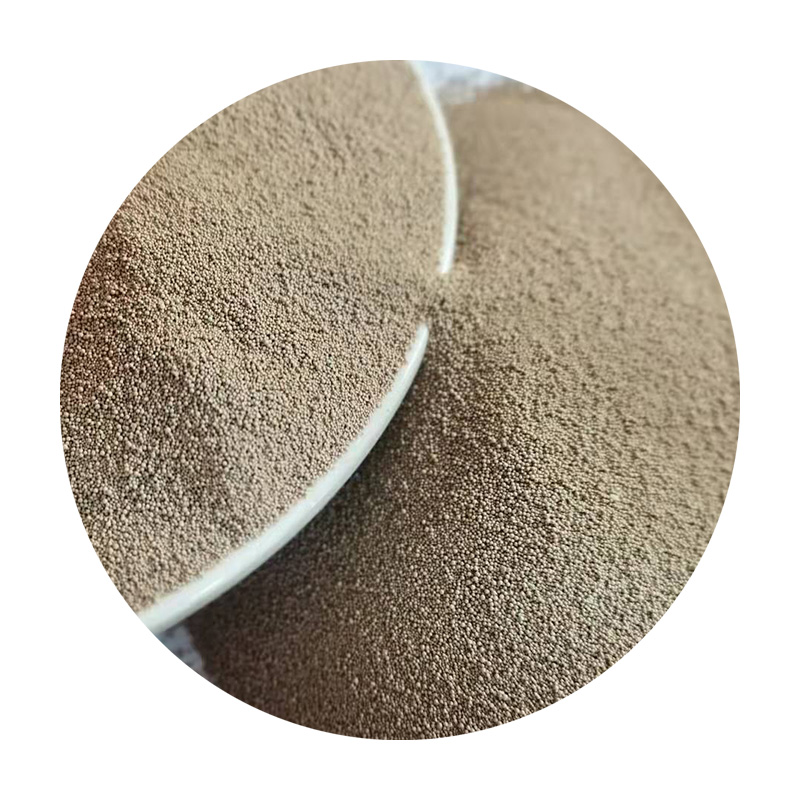
Another significant advantage of sand casting is its ability to accommodate a wide range of metal materials. Common metals used in sand casting include aluminum, iron, and magnesium, allowing manufacturers to select the most suitable material for their products. Moreover, sand casting is particularly advantageous for producing intricate designs and large parts that may be difficult to create through other methods.
Environmental Considerations
With growing environmental awareness, many sand casting factories are adopting more sustainable practices. The use of recycled sand, which can be reused multiple times, significantly reduces waste and environmental impact. Additionally, advancements in technology have improved the efficiency of the sand casting process, leading to lower energy consumption and reduced emissions.
Modern Innovations
Recent innovations in sand casting technology have made the process more efficient and accurate. For instance, the introduction of computer-aided design (CAD) and computer-aided manufacturing (CAM) has revolutionized pattern making and mold design. These technologies allow manufacturers to create highly precise patterns and molds, increasing the overall quality of the castings. Furthermore, advancements in automated machinery have streamlined the sand casting process, reducing labor costs and lead times.
Conclusion
In summary, sand casting remains a vital process in the manufacturing industry due to its numerous advantages, including cost-effectiveness, versatility, and the ability to produce large and complex components. As technology continues to evolve, sand casting factories are poised to enhance their capabilities while adopting more sustainable practices. With its rich history and promising future, sand casting is set to remain an essential method in the production of metal components for various industries worldwide. Whether it’s creating intricate automotive parts or robust aerospace components, sand casting continues to play a crucial role in meeting the demands of modern manufacturing.
Post time:تشرینی دووەم . 07, 2024 21:35
Next:Super Sand Wonders Create, Shape, and Play with Magical Sand Creations