The Art and Science of Sand Casting
Sand casting, a time-honored metal casting technique, has been around for centuries, playing a crucial role in the manufacturing of various metal components. Its adaptability, cost-effectiveness, and relatively simple process make it a favored choice among engineers and manufacturers for producing intricate shapes in a range of materials, particularly aluminum, iron, and bronze.
The Process of Sand Casting
The sand casting process consists of several key steps pattern making, molding, pouring, and finishing. Each of these stages is essential to ensure the final product meets the required specifications.
1. Pattern Making The first step involves creating a pattern, which is a replica of the object to be cast. Patterns can be made from various materials, including wood, metal, or plastic. The design of the pattern must account for shrinkage, as metals typically contract as they cool. This stage is critical because even minor errors in the pattern can result in significant flaws in the finished cast.
2. Molding Once the pattern is ready, it is used to form a mold from a mixture of sand and a binding agent. This mixture is compacted around the pattern, creating a negative impression. The sand used in this process is often coated with clay or other binders to enhance its ability to hold shape. Once the mold is set, the pattern is removed, leaving a cavity into which the molten metal will be poured.
3. Pouring At this stage, the selected metal is heated until it reaches a molten state. The metal is then carefully poured into the mold cavity through a gate system designed to channel the flow. The pouring temperature and speed are essential metrics, as improper pouring can lead to defects such as air pockets and incomplete fills within the mold.
4. Cooling and Finishing After the metal has been poured, it is left to cool and solidify. This process can take several hours, depending on the size and thickness of the casting. Once cooled, the mold is broken apart to reveal the cast part. The final product often requires additional finishing processes, such as grinding, sanding, or machining, to remove any imperfections and achieve the desired surface finish.
Advantages of Sand Casting
sand cast
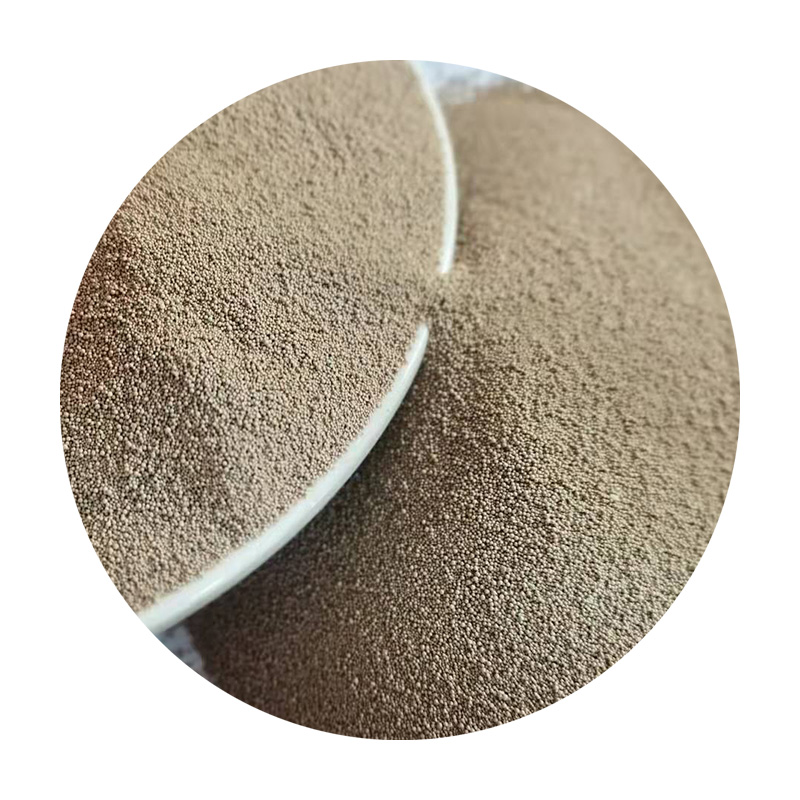
Sand casting offers numerous benefits that contribute to its continued popularity in manufacturing
- Cost-Effectiveness Sand casting is generally less expensive than other casting methods, especially for small production runs. The materials required, such as sand and binders, are relatively inexpensive, and since patterns can be reused, costs per unit decrease with higher production volumes.
- Flexibility in Design Sand casting allows for a high degree of design flexibility. Complex shapes, including internal cavities and undercuts, can be achieved with relative ease. This makes it a suitable choice for a wide range of applications, from automotive components to decorative art pieces.
- Material Versatility Many different metals can be cast using sand casting, making it a versatile option for various industries. It is particularly popular for casting ferrous and non-ferrous metals, each with their unique properties suited for specific applications.
Applications of Sand Casting
Sand casting is used across multiple industries, including automotive, aerospace, and art. In the automotive sector, components such as engine blocks, transmission housings, and various brackets are commonly produced using this technique. In aerospace, lightweight and high-strength components are designed using advanced alloys, while in the art world, sculptors and artisans use sand casting to create intricate sculptures and jewelry.
Conclusion
The enduring appeal of sand casting lies in its blend of simplicity and effectiveness. As technology advances and new materials emerge, sand casting continues to adapt, allowing for innovations that enhance quality and efficiency. Whether producing high-performance components for aircraft or creating beautiful art, the sand casting process remains a vital component of modern manufacturing. With its rich history and ongoing relevance, sand casting truly exemplifies the fusion of art and science in industrial processes.
Post time:کانونی یەکەم . 11, 2024 09:07
Next:Key Components of the Sand Casting Process and Their Roles in Manufacturing