Sand Casting of Cast Iron An Overview
Sand casting is one of the most widely used manufacturing processes for producing metal parts, particularly cast iron. This method is favored for its versatility, cost-effectiveness, and ability to create complex shapes. In this article, we will explore the sand casting process, its advantages and challenges, as well as its application in the production of cast iron components.
The Sand Casting Process
The sand casting process begins with creating a mold from a mixture of sand, clay, and water. The sand is compacted around a pattern, typically made of metal or plastic, which shapes the final product. Once the mold halves are formed, the pattern is removed, leaving a cavity in the sand that represents the object to be cast.
Next, molten cast iron is poured into the mold cavity. Cast iron, known for its excellent fluidity, allows it to fill intricate details of the mold easily. As the iron cools and solidifies, it takes on the form of the mold. After cooling, the sand mold is broken apart, and the finished cast iron part is retrieved.
Advantages of Sand Casting
One of the primary advantages of sand casting is its versatility. It can produce large and complex parts with varying sizes, from small components to large industrial parts weighing several tons. Moreover, the sand molds can be reused for multiple castings, which contributes to lower manufacturing costs.
Another benefit is the ability to create intricate designs with a wide range of metal alloys. Cast iron is particularly well-suited for this process due to its high melting point and ability to withstand high thermal stress. Additionally, it exhibits excellent wear resistance and machinability, making it an ideal material for components such as engine blocks, pipes, and machinery parts.
sand casting cast iron
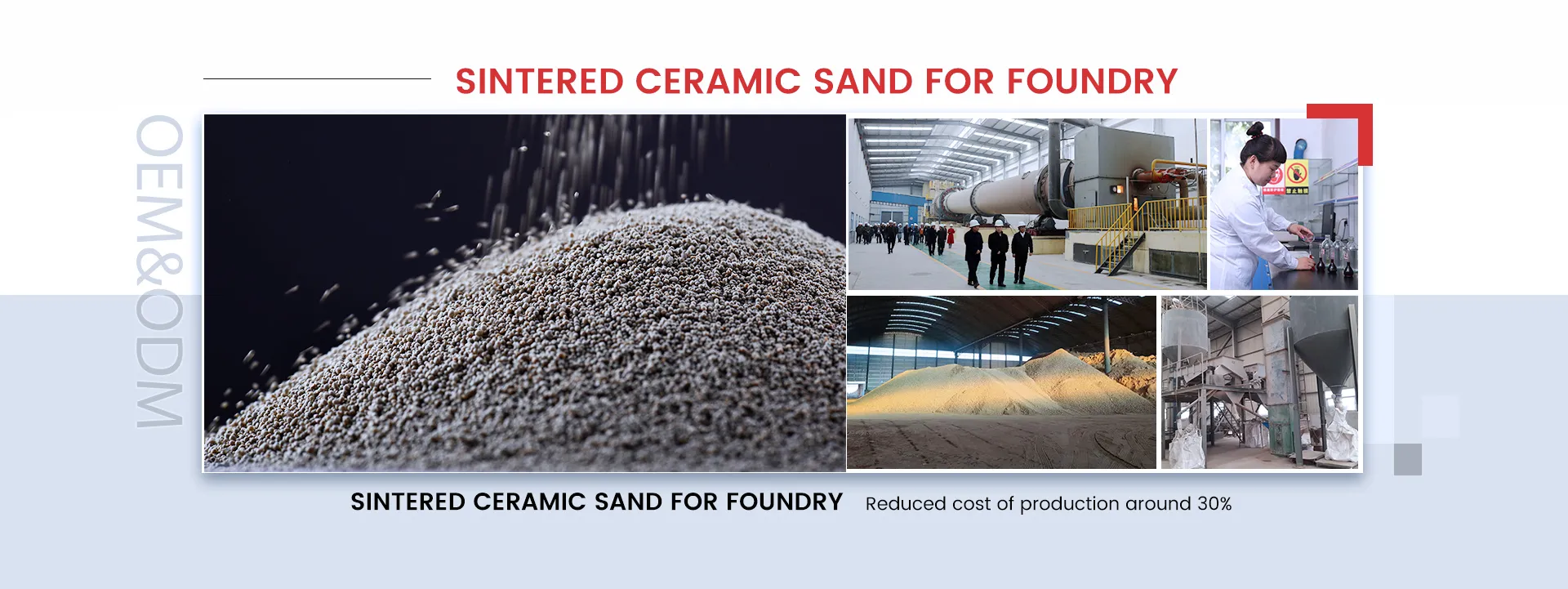
Challenges and Considerations
Despite its advantages, sand casting does come with its challenges. One significant issue is the porosity of the cast iron parts, which can affect the mechanical properties and surface finish. Furthermore, achieving tight tolerances and high dimensional accuracy can be difficult, requiring additional machining operations for precise parts.
Quality control during the sand casting process is crucial. Factors such as sand quality, moisture content, and temperature can significantly impact the final product. Manufacturers must implement strict quality assurance protocols to ensure that the cast iron components meet the required standards.
Applications of Sand Cast Iron
Sand casting is extensively used in various industries, including automotive, aerospace, and construction. Cast iron components produced through this method are commonly found in engines, exhaust manifolds, brake discs, and housing units. The durability and strength of cast iron make it a preferred choice for heavy-duty applications where performance and longevity are critical.
Conclusion
In summary, sand casting of cast iron is a fundamental manufacturing process that plays a vital role in producing a wide range of metal components. While it offers numerous advantages, careful consideration of challenges is essential for ensuring high-quality outputs. As technology advances, innovations in sand casting techniques will likely lead to improved efficiencies and enhanced capabilities, further solidifying its position in the manufacturing landscape.
Post time:ئیلول . 18, 2024 22:39
Next:Arena dorada