Understanding the Metal Sand Casting Process
Metal sand casting is one of the most versatile and widely used manufacturing processes for creating metal components. This method is favored for its ability to produce complex shapes and sizes that can be economically and efficiently manufactured. In this article, we will explore the metal sand casting process in detail, highlighting its stages, advantages, and applications.
The Sand Casting Process
The sand casting process involves several key steps, each critical to producing a high-quality metal part. The process generally begins with creating a mold from sand, which forms the negative impression of the desired part.
1. Pattern Making The first step in the sand casting process is the creation of the pattern. The pattern is a replica of the final part and is typically made from materials like wood, metal, or plastic. It is slightly larger than the final product to allow for shrinkage during cooling.
2. Mold Preparation Once the pattern is ready, it is used to form the mold. The most common type of sand used in sand casting is green sand, a mixture of sand, clay, and moisture. The pattern is pressed into the sand to create a mold cavity. This process can be done manually or with machines, depending on the complexity and quantity of the parts needed.
3. Core Placement For parts that require internal features or hollow sections, cores made from sand are created and placed in the mold. These cores are essential for shaping internal cavities of the final product.
4. Melting Metal In the next phase, the chosen metal—such as aluminum, iron, or bronze—is melted in a furnace. The molten metal must reach a specific temperature depending on its composition, which ensures proper flow into the mold.
5. Pouring After the metal has reached the proper temperature, it is poured into the mold. This step must be carried out carefully to avoid defects such as air pockets or uneven filling.
6. Cooling Once the mold is filled, the metal is allowed to cool and solidify. The cooling rate is critical, as it affects the properties of the final product. After sufficient cooling, the mold is broken to reveal the cast piece.
7. Finishing Following the removal from the mold, the casting undergoes finishing processes, including trimming, grinding, and machining to achieve the desired dimensions and surface finish.
metal sand casting process
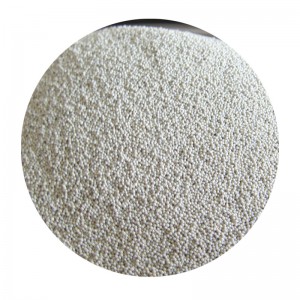
Advantages of Sand Casting
Metal sand casting boasts several advantages, making it a preferred choice compared to other manufacturing methods.
- Cost-effectiveness Sand casting requires low initial setup costs, allowing for economical production, especially for low to medium volumes. - Versatility This method is compatible with a wide range of metals and allows for the creation of complex geometries that would be difficult or impossible to achieve through other processes.
- Large Size Capabilities Sand casting can accommodate large parts, making it suitable for heavy machinery components, automotive parts, and more.
- Customization Since patterns can be easily modified, sand casting allows for tailored solutions to meet specific requirements.
Applications of Metal Sand Casting
The applications of metal sand casting span across various industries, including automotive, aerospace, construction, and art. In the automotive sector, sand casting is often used for engine blocks, transmission cases, and various other components due to its ability to produce intricate designs.
In the aerospace industry, precision cast parts are essential for aircraft components where performance and reliability are critical. Furthermore, sand casting is used in manufacturing tools, fixtures, and valves in the construction and plumbing sectors.
Conclusion
The sand casting process is a time-tested method that offers an effective solution for manufacturing metal components. Its ability to produce complex and large parts at a relatively low cost makes it an attractive option for many industries. As technology advances, innovations in sand casting processes are continually improving efficiency and product quality, making it an integral part of modern manufacturing practices. Whether creating everyday products or specialized parts, metal sand casting remains a vital component of the industrial landscape.
Post time:کانونی یەکەم . 12, 2024 15:52
Next:Sand Casting Process for Durable Stainless Steel Parts and Components