The Difference Between Sand Casting and Investment Casting
Casting is a fundamental manufacturing process used to create metal parts by pouring molten metal into a mold. Two common methods of casting are sand casting and investment casting, each with its own distinct processes, advantages, and applications. This article aims to highlight the primary differences between these two methods, helping manufacturers, engineers, and hobbyists choose the right casting technique for their specific needs.
Process Overview
Sand Casting In sand casting, a mold is created by compacting sand around a pattern, which is usually made of metal or wood. Once the pattern is removed, the mold consists of two halves that hold the cavity into which molten metal is poured. After the metal solidifies, the sand mold is broken apart to retrieve the cast part. This method is generally more cost-effective and suitable for larger castings and lower volume production, given that the process is relatively quick and requires less specialized equipment.
Investment Casting Also known as lost-wax casting, investment casting involves creating a wax pattern of the part to be cast. This wax pattern is coated with a ceramic material, and once the coating solidifies, the wax is melted away, leaving a precise mold. The molten metal is then poured into this mold. Investment casting produces parts with superior dimensional accuracy and surface finishes compared to sand casting, making it ideal for intricate designs and high-precision applications.
Material Considerations
One of the significant differences between sand casting and investment casting is the type of materials that can be used. Sand casting is versatile and can accommodate a wide range of metals, including aluminum, bronze, and iron. Its ability to handle larger quantities of metal makes it suitable for fabricating heavy parts.
On the other hand, investment casting is primarily used for producing non-ferrous metals, such as stainless steel and brass. This method excels in creating complex geometries that have thin walls and detailed features, which can be challenging with sand casting. As a result, investment casting is often favored in industries like aerospace and medical devices where precision and reliability are critical.
Surface Finish and Tolerances
difference between sand casting and investment casting
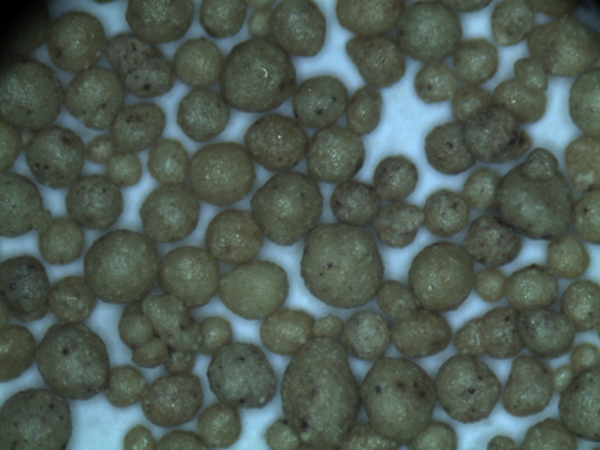
When it comes to surface finish and tolerances, investment casting has a clear advantage. The ceramic shell used in investment casting results in a much smoother surface finish compared to sand casting, which typically requires additional machining or finishing to achieve the desired quality. Furthermore, investment casting can maintain tighter tolerances, often within ±0.5% of the dimensional specifications, while sand casting tolerances can be greater due to the nature of the sand mold.
Production Volumes and Costs
Sand casting is generally more economical for low to medium production volumes. The reusable nature of sand molds can help reduce costs, although the molds are typically not as durable as those used in investment casting. For larger production runs, however, investment casting can become more cost-effective because of its reduced need for secondary operations and its capability for greater automation.
In contrast, investment casting typically has a higher initial cost due to the complexity of creating the ceramic shell and the use of wax patterns. However, the benefits of precision and reduced post-processing can justify these costs in high-volume applications.
Applications
The differences between sand casting and investment casting also reflect their respective applications. Sand casting is often employed in industries requiring large and robust components, such as automotive, construction equipment, and heavy machinery. It is an ideal choice for components such as engine blocks, frames, and pipes.
Investment casting, with its precision and complex capabilities, is widely used in sectors such as aerospace, where parts must meet stringent reliability standards, and in the jewelry industry for creating intricate designs. Medical device manufacturers also lean towards investment casting for producing components like surgical instruments or implantable devices that require high precision.
Conclusion
In summary, both sand casting and investment casting have their unique strengths and weaknesses. The choice between them largely depends on the specific requirements of the project, including material type, complexity, desired finish, production volume, and cost considerations. Understanding how these methods differ will empower manufacturers to select the most suitable casting technique for their applications, ensuring quality and efficiency in production.
Post time:کانونی یەکەم . 21, 2024 09:19
Next:Resin Bonded Sand Casting Techniques and Applications for Improved Foundry Processes