The Difference Between Die Casting and Sand Casting
Casting is a fundamental manufacturing process that involves pouring liquid material into a mold to create solid objects. Two of the most common casting methods are die casting and sand casting. Each process has its unique characteristics, advantages, and limitations, making them suitable for different applications. Understanding the differences between these two methods is crucial for selecting the appropriate technique for a specific project.
Die Casting
Die casting is a precision casting process that uses high pressure to force molten metal into a rigid mold, or die. This method is primarily used for non-ferrous metals, such as aluminum, zinc, and magnesium. One of the most significant advantages of die casting is its ability to produce intricate shapes and smooth surfaces with tight tolerances. The dies are usually made from hardened steel or other durable materials and can last for thousands of cycles, making die casting suitable for mass production.
The die casting process begins with the creation of a mold, which consists of two halves. The halves are clamped together, and molten metal is injected into the mold cavity under high pressure. After the metal cools and solidifies, the mold is opened, and the finished part is ejected. This method allows for quick production runs and is particularly efficient for high-volume manufacturing, resulting in lower per-piece costs over time.
However, die casting also has its downsides. The initial cost of creating the molds can be high, making it less economical for small production runs or one-off prototypes. Additionally, the process is limited to certain materials, primarily non-ferrous metals, which can restrict its applications in some industries.
Sand Casting
difference between die casting and sand casting
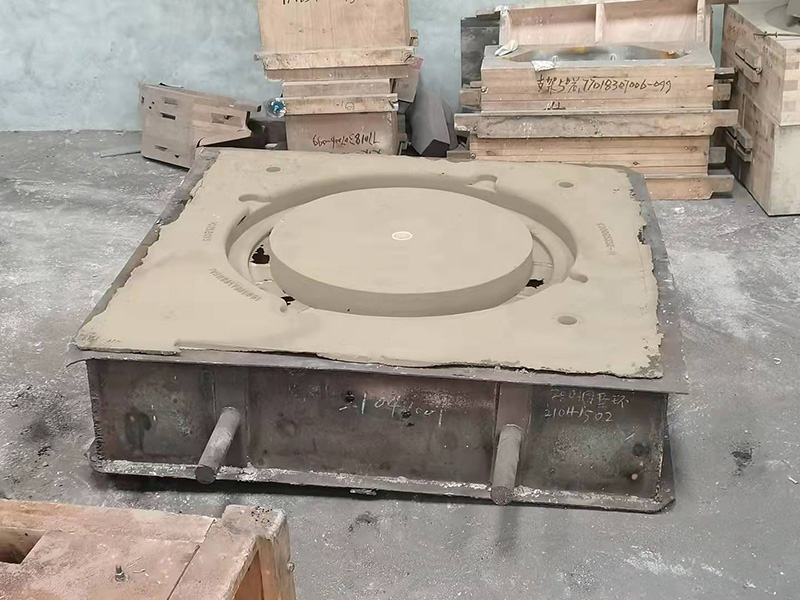
On the other hand, sand casting is a more traditional and versatile method that uses sand as the primary material to create molds. In this process, a mixture of sand, clay, and water is formed into a mold around a pattern, typically made of metal or plastic. Once the mold is created, molten metal is poured into the cavity and allowed to cool and solidify before the sand mold is removed to reveal the final product.
One of the key advantages of sand casting is its flexibility in terms of the types of metals that can be used, including ferrous and non-ferrous alloys. Additionally, sand casting can accommodate larger and more complex shapes than die casting, making it suitable for both small and large production runs. The initial setup costs are also lower for sand casting, making it an attractive option for prototype development and smaller quantities.
However, sand casting has its limitations. The surface finish is generally rougher compared to die casting, and the tolerances are not as tight, which can result in additional machining costs for some applications. The mold-making process itself can also be time-consuming, leading to longer lead times for production.
Conclusion
In summary, both die casting and sand casting offer valuable methods for manufacturing metal parts, each with its own set of advantages and disadvantages. Die casting excels in high-volume production with high precision and smooth finishes, making it ideal for consumer goods and automotive components. In contrast, sand casting provides greater flexibility in terms of materials and part size but may incur additional costs due to its rougher surface finish and longer setup times.
Choosing between die casting and sand casting ultimately depends on the specific requirements of the project, including production volume, material selection, and cost considerations. By understanding the differences between these two casting methods, manufacturers can make informed decisions that align with their production needs and objectives.
Post time:کانونی یەکەم . 31, 2024 05:59
Next:Exploring the Fundamentals of Sand Casting Techniques and Their Advantages in Manufacturing