The Difference Between Sand Casting and Permanent Mold Casting
Casting is a fundamental manufacturing process that involves pouring a liquid material into a mold to create a desired shape. Two common methods of casting include sand casting and permanent mold casting, each with its unique features, advantages, and applications. Understanding the differences between these two methods is essential for selecting the appropriate casting technique for specific projects.
1. Definition and Materials
Sand casting involves the use of a mold made from a mixture of sand and a binding agent. The sand is shaped to form a cavity that represents the final product. Once the mold is created, molten metal is poured into the cavity, allowed to cool, and then removed, leaving behind a cast object. Sand casting is versatile and can accommodate a wide range of metals, including iron, aluminum, and bronze.
In contrast, permanent mold casting utilizes molds made from metal, typically steel or iron, which can withstand repeated use. The molds are designed to be more durable and provide a smooth surface finish compared to sand molds. This method is often used for non-ferrous metals, such as aluminum and magnesium, due to their lower melting points.
2. Process Differences
The casting process for sand casting involves several steps creating the pattern, making the mold, pouring the metal, and finishing the final product
. The patterns are often made from wood or plastic and must be slightly larger than the final object to accommodate for metal contraction during cooling.Permanent mold casting, on the other hand, requires a more sophisticated setup. The metal molds are preheated to help facilitate better metal flow and reduce cooling time. After pouring, the metal is allowed to cool in the mold and is typically removed after a shorter duration compared to sand casting. This results in faster production cycles and higher productivity.
difference between sand casting and permanent mold casting
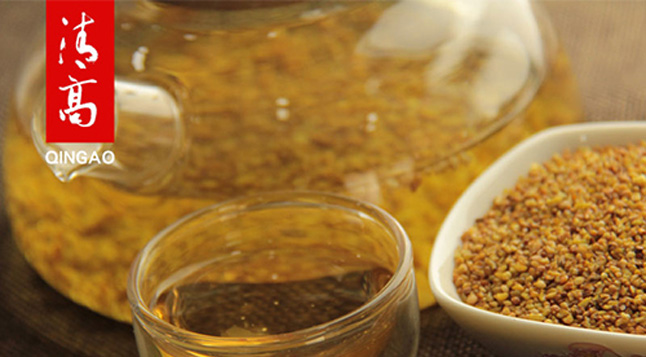
3. Tolerance and Surface Finish
One of the significant differences between sand casting and permanent mold casting lies in the tolerances and surface finish of the final products. Sand casting generally has a coarser surface finish and lower dimensional accuracy due to the nature of sand molds. The resulting castings may require additional machining or finishing processes to achieve the desired tolerances and surface quality.
In contrast, permanent mold casting provides a superior surface finish and tighter tolerances since the metal molds can be accurately machined and polished. This eliminates or reduces the need for post-casting operations, making it an attractive choice for high-precision applications.
4. Production Volume
Sand casting is highly adaptable and can be used for low to medium production volumes. It excels in producing complex shapes and allows for the casting of large components. However, each sand mold is typically single-use, which can be less cost-effective for high production runs.
Permanent mold casting is better suited for high-volume production, as the metal molds are reusable and can produce a large number of identical parts efficiently. The initial investment in metal molds can be high, but the cost per unit decreases significantly with mass production, making it a viable option for manufacturers producing large quantities of parts.
5. Conclusion
In summary, sand casting and permanent mold casting are two distinct casting methods, each with its advantages and constraints. Sand casting offers flexibility, complexity, and adaptability, making it a suitable choice for various applications, especially in low to medium volumes. On the other hand, permanent mold casting provides higher precision, better surface finish, and is more efficient for high-volume production. The choice between the two methods ultimately depends on the specific requirements of the project, including material, production volume, and desired tolerances. Understanding these differences can lead to more informed decisions in the casting process, ensuring optimal manufacturing outcomes.
Post time:ئاب . 14, 2024 19:52
Next:Innovative Techniques in Lost Foam Casting for Enhanced Precision and Efficiency in Metal Fabrication