The Role of Ceramsite Foundry Sand in Modern Casting Processes
Ceramsite foundry sand, a type of engineered material, has gained significant attention in the foundry industry for its unique properties and advantages over traditional sand materials. This innovative product is manufactured from ceramic aggregates and offers a variety of benefits, making it an increasingly popular choice for casting processes.
Foundry sand is typically used in the production of metal castings, where it forms a mold that provides the necessary support for molten metal. The primary challenge with using traditional silica sand is its susceptibility to thermal expansion, which can lead to defects in the final product. In contrast, ceramsite foundry sand exhibits superior thermal stability and low thermal expansion, significantly reducing the risk of casting defects such as warping and cracking.
One of the most prominent benefits of ceramsite foundry sand is its improved flowability. The spherical shape of ceramsite particles allows for better packing density and enhances the sand's ability to fill complex mold geometries. This characteristic is particularly important in demanding applications where intricate designs are required. The result is a higher-quality finish on the castings produced, minimizing the need for extensive post-processing.
ceramsite foundry sand
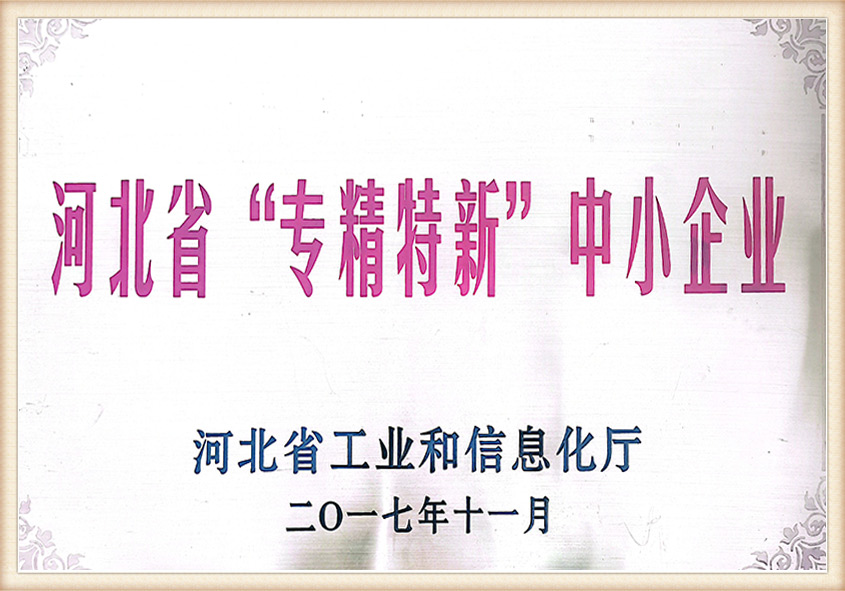
Moreover, ceramsite foundry sand is known for its excellent strength and durability. When mixed with binders, it forms molds that withstand the intense pressures and temperatures of the casting process. This strength translates into longer mold life, reducing the frequency of mold replacements and consequently lowering production costs. Additionally, the durability of ceramsite sand contributes to fewer defects during casting, further enhancing its appeal for manufacturers.
Environmental considerations are another crucial aspect of ceramsite foundry sand. Traditional silica sands often pose environmental challenges related to mining, dust emissions, and waste disposal. In contrast, ceramsite foundry sand is often produced from recycled materials, making it a more sustainable choice. Using recycled raw materials not only minimizes waste but also reduces the carbon footprint associated with the production of new sand, aligning with the growing emphasis on sustainability in industrial practices.
The production of ceramsite foundry sand involves a controlled manufacturing process that ensures consistent quality and performance. This consistency is vital for foundries looking to maintain high standards in their casting operations. Furthermore, the adaptability of ceramsite sand to various binding systems and casting techniques makes it a versatile option for different types of metal alloys and applications.
In conclusion, ceramsite foundry sand presents a modern solution for the challenges faced in traditional foundry practices. Its exceptional properties, such as thermal stability, flowability, strength, and environmental friendliness, position it as a leading choice for manufacturers seeking to improve efficiency and quality in their casting processes. As the foundry industry continues to evolve, the adoption of materials like ceramsite foundry sand will likely play a pivotal role in driving innovation and sustainable practices forward.
Post time:تشرینی یەکەم . 18, 2024 10:33
Next:Essential Materials Utilized in the Sand Casting Process for Metal Production