3D Printing for Sand Casting Revolutionizing the Foundry Industry
The foundry industry is witnessing a technological revolution, largely driven by the advent of 3D printing. Among the various applications of this innovative technology, 3D printing for sand casting stands out as a transformative approach. This method is redefining traditional sand casting processes, providing numerous advantages that enhance efficiency, reduce costs, and improve product quality.
Understanding Sand Casting
Sand casting is one of the oldest and most widely used manufacturing processes. It involves creating a mold from a mixture of sand and a binding agent. Traditionally, the mold is formed using patterns, which are typically made from metal, wood, or plastic. Once the mold is prepared, molten metal is poured into it, allowed to cool, and finally removed to reveal the cast part. While this process has been effective, it often involves lengthy lead times and high costs, particularly for pattern production.
The Rise of 3D Printing in Sand Casting
3D printing, also known as additive manufacturing, has gained considerable traction across various industries, including automotive, aerospace, and consumer goods. In the context of sand casting, 3D printing offers a unique solution the ability to create complex mold geometries directly from digital models. This is achieved by using a variety of 3D printing technologies, such as binder jetting, to produce sand molds with exceptional precision and detail.
Advantages of 3D Printed Sand Molds
1. Reduced Lead Times One of the most significant advantages of 3D printing for sand casting is the considerable reduction in lead times. Traditional pattern creation can take weeks or even months, depending on the complexity of the design. In contrast, 3D printing can produce sand molds in a matter of days or even hours. This allows manufacturers to respond quickly to market demands and shorten production cycles, a critical factor in today’s fast-paced industrial environment.
3d printing for sand casting
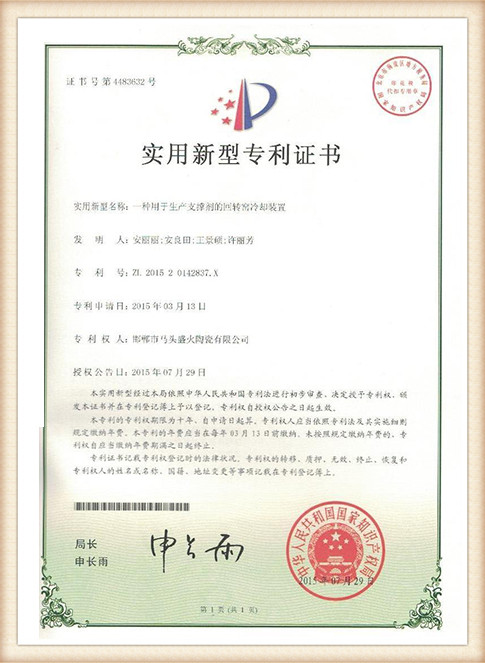
2. Design Freedom 3D printing breaks the traditional constraints associated with sand casting molds. Designers can create intricate shapes and internal geometries that would be impossible or prohibitively expensive to achieve using conventional methods. This capability opens up new avenues for innovation, enabling the production of lighter parts with enhanced performance characteristics.
3. Cost Efficiency While the initial investment in 3D printing technology can be significant, the reduction in material waste and the elimination of traditional tooling costs lead to substantial long-term savings. The additive nature of 3D printing means that molds are built layer by layer, resulting in less sand waste compared to traditional methods, where excess material is often discarded.
4. Customization and Low-Volume Production 3D printing is particularly beneficial for industries requiring customized or low-volume production runs. Traditional sand casting can be inefficient for small batches due to the high costs of creating molds. However, with 3D printing, molds can be created on-demand, allowing for flexibility in production without the need for significant investment in tooling.
5. Sustainability As industries lean toward more sustainable practices, 3D printing in sand casting offers environmental benefits. The use of environmentally friendly sand materials and the reduction of waste contribute to a smaller carbon footprint, aligning with global efforts toward sustainability in manufacturing.
Challenges and Future Outlook
Despite its numerous advantages, the adoption of 3D printing in sand casting is not without its challenges. The initial costs of 3D printing equipment and technology can be a barrier for some foundries. Additionally, there may be a learning curve for teams new to additive manufacturing processes.
However, as technology advances and becomes more accessible, these challenges are likely to diminish. The foundry industry is gradually embracing 3D printing as a mainstream manufacturing method, with ongoing research and development aimed at enhancing material properties and expanding capabilities.
In conclusion, 3D printing for sand casting is reshaping the future of the foundry industry by offering faster production times, cost-effective solutions, and unparalleled design freedom. As this technology continues to evolve, it promises to drive further innovations in manufacturing, ultimately leading to superior products and more responsive supply chains in various sectors. The integration of 3D printing in sand casting is not just a trend; it represents a significant leap forward in how we approach metal casting processes in the modern age.
Post time:تشرینی دووەم . 20, 2024 18:34
Next:odlewanie piasku na sprzedaż