Why Sand Casting is Preferred A Comprehensive Overview
Sand casting, a fundamental manufacturing process, has stood the test of time as one of the most widely used methods for producing metal parts. The reasons for its enduring popularity are numerous and diverse, making it the process of choice in various industries. This article explores the key advantages of sand casting and why it remains a preferred manufacturing method.
1. Cost-Effectiveness
One of the most significant advantages of sand casting is its cost-effectiveness. The materials required for sand casting, particularly silica sand, are abundant and relatively inexpensive. Additionally, the cost of the molds made from sand is lower compared to other casting methods such as die casting or investment casting. This makes sand casting an economical choice, especially for producing large and heavy components.
2. Versatility in Materials
Sand casting is compatible with a wide range of metals and alloys, including aluminum, brass, bronze, and iron. This versatility allows manufacturers to choose the most suitable material for their specific application. Furthermore, the ability to cast a variety of alloys helps industries address specific performance requirements, such as corrosion resistance or high tensile strength.
3. Scale of Production
Sand casting is particularly advantageous for low to medium production runs. It can efficiently produce small batches of parts, which is ideal for custom or prototype components. Although it may not be as efficient for mass production compared to processes like die casting, sand casting's flexibility allows manufacturers to quickly adapt to changing design requirements without significant lead time.
4. Ability to Create Complex Shapes
Another significant benefit of sand casting is its capability to create complex shapes and intricate designs. The sand mold can be easily shaped to accommodate various geometries, which is particularly useful for components that have elaborate patterns or internal cavities. This eliminates the need for extensive machining processes, simplifying production and reducing costs.
why sand casting is preferred
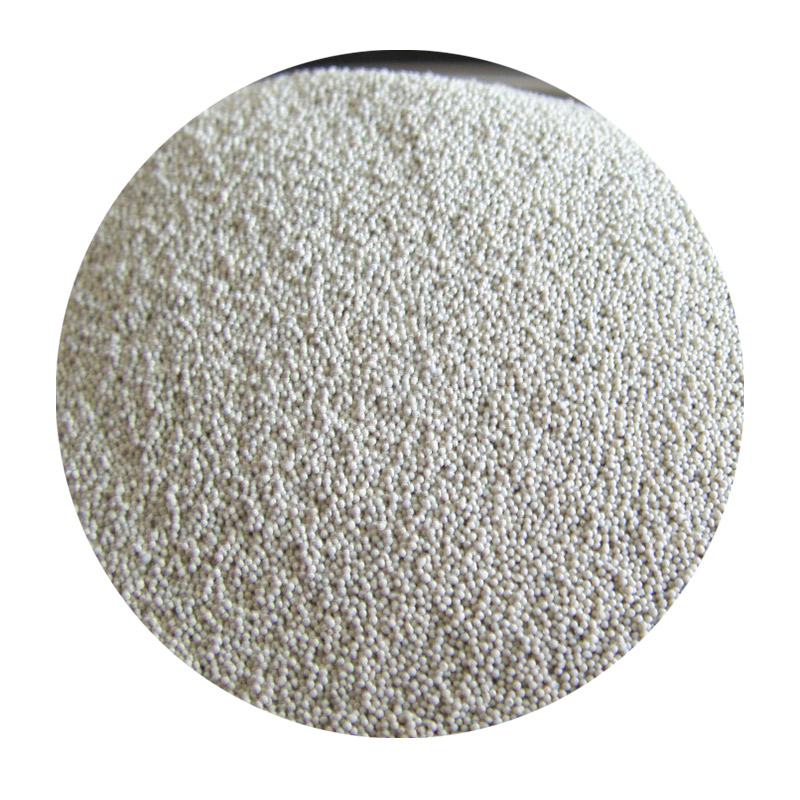
5. Excellent Surface Finish and Tolerances
While sand casting may not offer the same fine surface finish as some other methods, advancements in techniques and materials have significantly improved the outcomes. Modern sand casting processes can achieve surface finishes that meet industry standards and tolerances, making it suitable for a wide array of applications. Additionally, the use of special sands and binders can enhance the mold's surface quality, further refining the final product.
6. Environmental Benefits
Sand casting is relatively environmentally friendly compared to many other casting methods. The sand used in the process can be reused multiple times, reducing waste and the need for new materials. Additionally, most of the by-products generated during sand casting can be recycled or repurposed, thus contributing to more sustainable manufacturing practices.
7. Accessibility and Simplicity of Setup
Setting up a sand casting operation is generally simpler and requires less specialized equipment than alternative methods. This accessibility enables smaller manufacturers and hobbyists to adopt sand casting with minimal investment, promoting innovation and craft skills. The straightforward nature of the process also allows for quicker turnaround times from design to production.
8. Low Heat Treatment Costs
Parts produced through sand casting often require less extensive heat treatment compared to those made with other methods. The solidification process of metal in the sand mold can help mitigate stresses and defects, allowing for a more reliable final product with fewer post-processing steps. This translates to both time and cost savings for manufacturers.
Conclusion
In summary, sand casting's preference in the manufacturing industry stems from its economic viability, versatility, and ability to produce complex shapes. The technique offers significant advantages in terms of material compatibility, production scale, surface finish, and environmental sustainability. As technology advances, the sand casting process continues to evolve, making it an enduring and reliable choice for manufacturers worldwide. Whether for prototyping, custom parts, or low-volume production, sand casting remains a cornerstone of metalworking and manufacturing, demonstrating its unmatched adaptability and efficiency in meeting diverse industrial needs.
Post time:1월 . 02, 2025 16:39
Next:Odlewanie suchego piasku