Understanding Types of Sand Casting Processes
Sand casting is one of the oldest and most widely used metal casting techniques in manufacturing. It involves the creation of a mold made from sand, which is then filled with molten metal to produce a desired shape. This versatile process is favored for its adaptability to various metal types and simple setup. The sand casting process can vary based on several parameters, including the type of sand used, the method of molding, and the specific application. Here, we explore the primary types of sand casting processes.
1. Green Sand Casting
Green sand casting is the most traditional and commonly used method. In this process, a mixture of sand, clay, and water is used to create the mold. The term green refers to the moisture content in the mold, which remains unbaked and, hence, retains its natural state. This type of casting is ideal for producing a variety of parts, including automotive components and industrial machinery. The key advantage of green sand casting is its cost-effectiveness and the ability to create complex designs due to its excellent flowability. However, since the green sand is soft, it may not hold fine details as effectively as other methods.
2. Dry Sand Casting
In contrast to green sand casting, dry sand casting uses a mixture that is baked or dried before use. The sand is treated with a binding agent, and the molds are heated to eliminate moisture. This results in a more rigid mold that can withstand higher temperatures and produce finer details in the final casting. Dry sand casting is particularly useful for producing large, heavy components where strength and durability of the mold are crucial. Although it is more labor-intensive due to the additional steps required, the benefits often outweigh the costs in applications demanding precision.
types of sand casting process
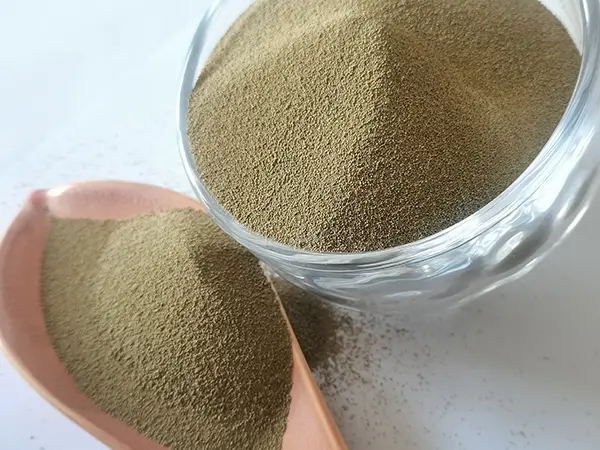
No-bake sand casting, also known as cold setting, involves a chemical binder instead of moisture to form the mold. This method does not require baking in an oven; instead, the sand is mixed with a resin-bonded binder, which cures at room temperature. No-bake processes are preferred for complex shapes and high-accuracy parts because the mold can be created more rapidly and with better dimensional control. This technique is particularly popular in applications that require high-strength castings, such as in aerospace and defense manufacturing.
4. Lost Foam Casting
Lost foam casting is a unique variation of sand casting where a foam model is used to create the mold. The foam is coated with a sand mixture, and when molten metal is poured in, it vaporizes the foam, leaving behind a cavity in the shape of the original model. This method allows for the creation of intricate geometries and internal features that would be challenging with traditional casting methods. Lost foam casting is often used in the automotive and machinery industries for producing complex parts that require high precision and surface finish.
5. Investment Casting (Sand-Casting Hybrid)
Though primarily known as a distinct process, investment casting can be considered a hybrid when using sand molds. Investment casting involves creating a wax or plastic pattern, which is then coated with a sand mixture. Once the mold hardens, the pattern is removed, and molten metal fills the cavity. This method is known for its excellent accuracy and surface finish, making it ideal for detailed components in industries such as jewelry and medical devices.
Conclusion
With various types of sand casting processes available, manufacturers can choose the method that best meets their needs based on factors such as precision, cost, and complexity of the desired part. As technology continues to advance, so do sand casting techniques, improving efficiency and expanding applications across industries. From green sand to lost foam methods, each type offers distinct advantages that cater to specific manufacturing challenges, ensuring sand casting remains a cornerstone of production in the metallurgical sector.
Post time:11월 . 20, 2024 05:02
Next:lost foam metal casting