Steps of Sand Casting A Comprehensive Guide
Sand casting is one of the oldest and most widely used metal casting processes, particularly renowned for its versatility in producing complex shapes and sizes of metal objects. It involves the creation of a mold from a sand mixture and the subsequent pouring of molten metal into that mold to form the final product. This article outlines the essential steps involved in the sand casting process, providing a detailed understanding for those interested in metalworking and manufacturing techniques.
1. Pattern Making
The first step in sand casting is the creation of a pattern. A pattern is a replica of the final product, usually made of wood, metal, or plastic. It is essential for the pattern to be slightly larger than the final product to account for metal shrinkage as it cools. The complexity of the design influences the choice of materials for the pattern. For simple shapes, wood patterns are sufficient; however, for more complex designs, metal patterns are preferred for their durability and accuracy.
2. Mold Creation
Once the pattern is ready, the next step is to create a mold. This is achieved by placing the pattern in a mold box and surrounding it with a sand mixture, typically composed of silica sand, clay, and water. The mixture is compacted around the pattern to ensure fine details are captured. Two halves of the mold are usually made one for the top portion (cope) and another for the bottom (drag). After compaction, the mold halves are carefully separated, and the pattern is removed, leaving a cavity that reflects the desired shape of the final product.
3. Core Making
If the final casting requires internal cavities or complex geometries, cores are used. Cores are additional pieces made of sand that are placed inside the mold to create these internal features. Similar to the mold-making process, cores are composed of a sand mixture, and they are created separately before being inserted into the mold cavity before pouring the metal.
4
. Melting the Metalsteps of sand casting
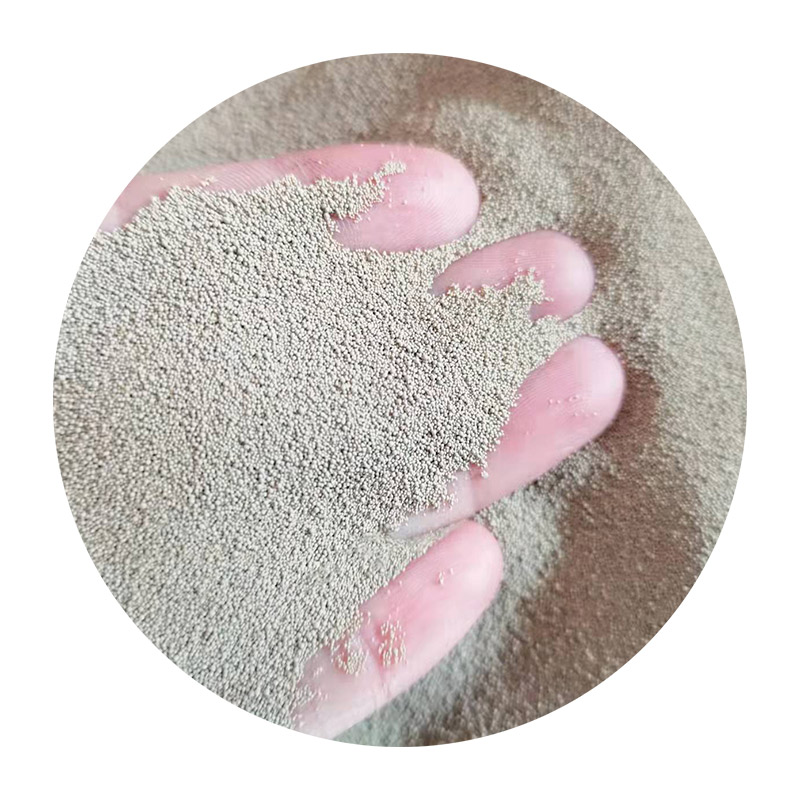
Once the mold is prepared and the cores are in place, the next step is to melt the metal. The choice of metal depends on the desired properties of the final product. Common metals used in sand casting include aluminum, iron, and bronze. The metal is melted in a furnace at the appropriate temperature, usually between 1,200°C to 1,600°C (2,192°F to 2,912°F), depending on the material.
5. Pouring
With the metal molten and the mold ready, the next step is pouring the molten metal into the mold cavity. This process must be performed swiftly yet carefully to ensure that the mold does not break or become misaligned. The pour should be done from a height that minimizes turbulence, allowing for a smooth flow of metal that prevents air pockets and ensures complete filling of the mold.
6. Cooling
After pouring, the metal needs time to cool and solidify. The cooling time varies depending on the metal type and the thickness of the casting. During this phase, the metal transitions from a liquid to a solid state, filling the mold cavity entirely.
7. Mold Removal and Finishing
Once the metal has cooled and solidified, the mold is removed. This often involves breaking apart the sand mold, which is designed to be reusable. After removal, the casting may require several finishing processes, such as trimming excess material, grinding, machining, or polishing, to achieve the desired surface finish and dimensional accuracy.
Conclusion
Sand casting is a time-tested method that excels in producing intricate shapes and large parts. Understanding the steps involved—from pattern making to mold removal and finishing—highlights the craftsmanship required in this traditional manufacturing process. The adaptability and cost-effectiveness of sand casting continue to make it a popular choice in various industries, from automotive to aerospace.
Post time:12월 . 30, 2024 12:11
Next:smooth 3d prints without sanding