Understanding the Sand Casting Process
Sand casting, one of the oldest and most versatile manufacturing processes, has been a staple method in the foundry industry for centuries. This method, known for its simplicity and adaptability, allows for the production of complex shapes and large components. As industries evolve, sand casting continues to play a pivotal role in the manufacturing of metal parts, owing to its effectiveness and cost-efficiency.
The Basics of Sand Casting
At its core, sand casting involves pouring molten metal into a mold created from sand. The process begins with forming a pattern, typically made of a material such as wood or metal, which represents the object to be cast. This pattern is then used to create a mold in compacted sand mixed with a binding agent. The resulting mold consists of two halves, which are joined together to form a cavity in the shape of the desired product.
The choice of sand is critical in the sand casting process. Green sand, a mixture of silica sand, clay, water, and other additives, is commonly used. This mixture provides good collapsibility and promotes easy handling. Other types of sand, like resin-bonded sand, offer enhanced strength and can yield finer details, making them ideal for particular applications.
The Sand Casting Process Steps
1. Pattern Creation The first step involves creating a pattern that reflects the final product. Patterns should account for shrinkage and other factors that could affect the finished dimensions.
2. Mold Preparation The pattern is placed in a sand mixture, which is then packed tightly around it. Once the sand sets, it forms a mold that has the negative shape of the pattern.
3. Core Creation For hollow sections, cores made from sand may be placed in the mold. These cores create internal features of the final casting.
4. Pouring After the mold is prepared, molten metal is poured into the cavity. The temperature and type of metal used depend on the specific requirements of the casting process.
sand casting processes
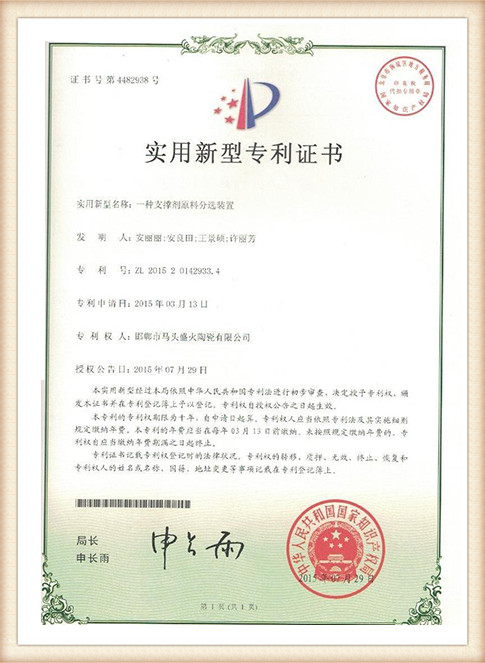
5. Cooling Once poured, the molten metal cools and solidifies inside the mold. The cooling time varies based on the metal's properties and the casting’s thickness.
6. Mold Removal and Finishing After sufficient cooling, the mold is broken open to retrieve the casting. The process often leaves behind flash or burrs that need to be removed through machining or grinding.
Advantages of Sand Casting
Sand casting offers numerous advantages. It accommodates a wide variety of metals, including aluminum, iron, and copper alloys. The process is notably flexible, enabling the production of castings of varying sizes and complexities—from small intricate components to large industrial parts. Moreover, sand casting can be cost-effective for low to medium production runs, as the patterns can be reused multiple times.
The process also supports quick turnaround times, making it suitable for prototyping and short production runs. Additionally, sand casting is environmentally friendly, as the materials used can often be recycled.
Applications of Sand Casting
The versatility of sand casting allows it to be used in various industries, including automotive, aerospace, construction, and art. Common applications range from engine blocks and transmission cases to intricate sculptures. The ability to produce both custom and standard parts makes sand casting an invaluable technique in modern manufacturing.
Conclusion
In summary, sand casting is a time-honored manufacturing process that remains relevant in today’s advanced technological landscape. Its advantages—in terms of versatility, cost-effectiveness, and ease of use—make it a preferred choice for many industry professionals. As manufacturing continues to adopt innovative technologies and practices, sand casting will undoubtedly evolve but will likely remain a fundamental technique for creating metal components for years to come.
Post time:12월 . 12, 2024 22:53
Next:what to sand resin with