Sand Casting Procedure A Comprehensive Overview
Sand casting is one of the oldest and most widely used metal casting methods, known for its versatility and cost-effectiveness. This process involves creating a mold from sand and then pouring molten metal into that mold to create various metal parts or components. Understanding the sand casting procedure is essential for engineers and manufacturers looking to produce complex shapes with excellent surface finishes. This article provides a detailed overview of the sand casting process.
1. Design and Pattern Creation
The sand casting procedure begins with the design of the product and the creation of a pattern. The pattern is a replica of the final product, typically made from materials such as wood, metal, or plastic. The design should account for factors such as shrinkage, draft angles, and finishing allowances. Patterns are often made slightly larger than the final piece, as metals generally contract as they cool.
2. Selecting the Sand
The choice of sand is critical. The most commonly used sand for casting is silica sand, valued for its grain size and shape. The sand is mixed with a binder to enhance its cohesiveness. Common binders include clay and chemical binders, which help retain the sand's shape during the molding process. The sand mixture is often prepared to a specific moisture content to achieve the required strength.
3. Molding Process
The molding process involves creating a mold cavity in which the molten metal will be poured. The pattern is placed in a flask, a type of frame that holds the sand. Sand is then packed around the pattern to form the mold. This can be done manually or using automated processes. Once the sand is compacted, the pattern is removed, leaving a negative impression or mold cavity.
Two main types of molds are used in sand casting green sand molds, made from a mixture of sand and water, and dry sand molds, which use a baked sand mixture. Green sand molds allow for better flow of molten metal and are easier to produce, while dry sand molds offer better dimensional stability and a finer surface finish.
sand casting procedure
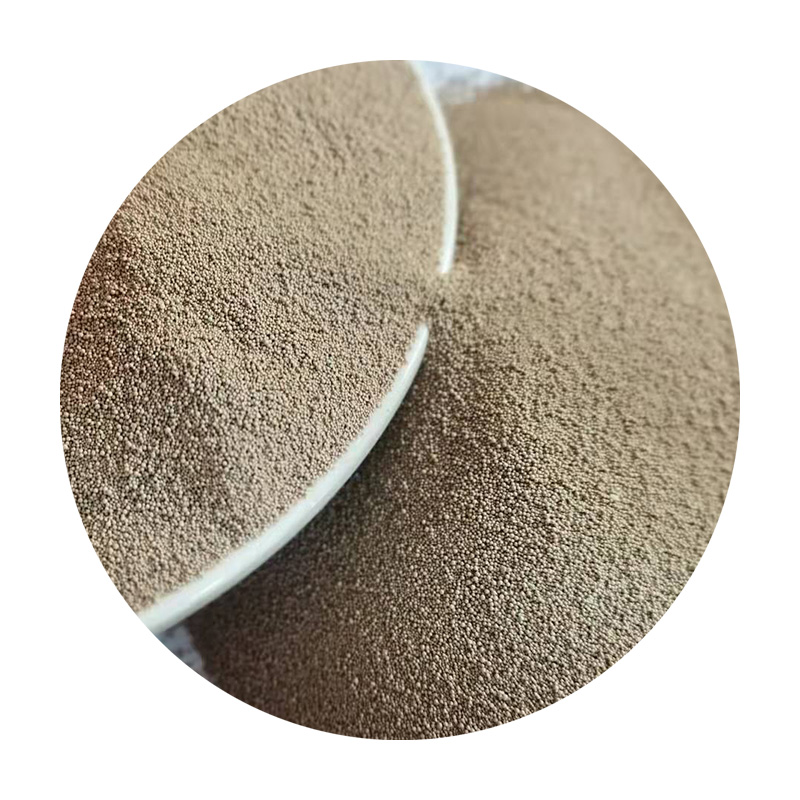
For complex designs that include internal cavities, cores are created. Cores are made from sand or other materials and are placed in the mold before the molten metal is poured. Cores provide additional features to the casting, such as internal passages and shapes that cannot be achieved using the mold alone.
5. Melting and Pouring
Once the mold is prepared, the next step is melting the metal. The type of metal used can vary widely, with aluminum, cast iron, and bronze being common choices. The metal is melted in a furnace, reaching temperatures that allow it to flow freely. Once melted, the metal is carefully poured into the mold cavity through a gate system designed to control the flow of the metal and minimize turbulence. Proper pouring techniques are essential to prevent defects such as air pockets or uneven cooling.
6. Cooling and Solidification
After pouring, the metal will begin to cool and solidify. The cooling time will depend on the thickness of the casting and the type of metal used. As the metal cools, it contracts. Once fully solidified, the mold is broken away, usually by hand or with mechanical tools. The result is a rough casting that may require further processing.
7. Finishing Operations
The final step in the sand casting procedure involves finishing operations to achieve the desired surface quality and dimensions. This may include processes such as
- Sand blasting to smooth the surface. - Machining to refine the dimensions and improve accuracy. - Welding for assembly of multi-part castings.
Conclusion
The sand casting procedure is a vital manufacturing process known for its flexibility and ability to produce complex shapes economically. By understanding each step of the process—from pattern creation to finishing operations—manufacturers can ensure higher quality castings, reduce defects, and improve overall efficiency. As technology advances, innovations in sand casting continue to enhance its capabilities, paving the way for even more sophisticated applications in various industries.
Post time:11월 . 25, 2024 14:21
Next:foundry sand pdf