Understanding Sand Casting Definition and Process
Sand casting is one of the oldest and most widely used metal casting processes. As a versatile and economical method, it allows for the production of complex metal parts and components with relatively low tooling costs. In this article, we will explore the definition of sand casting, its process, advantages, and some common applications.
Definition of Sand Casting
Sand casting, also referred to as sand mold casting, is a metal casting process where molten metal is poured into a mold made from sand. The mold is created by compacting sand around a pattern, which is a replica of the object to be cast. The sand is typically mixed with a binding agent to improve strength and durability. Once the mold is formed and the pattern is removed, the cavity left behind is filled with molten metal, which cools and solidifies to take the shape of the original pattern.
The Sand Casting Process
The sand casting process consists of several key steps
1. Pattern Making The initial step involves creating a pattern, usually made from metal, plastic, or wood, that mirrors the final product. The pattern is slightly larger than the desired final piece to account for shrinkage during cooling.
2. Mold Creation Once the pattern is ready, it is placed in a flask, and sand mixed with a binder is packed around it. The packing must be uniform and dense to provide sufficient support to the mold. After the sand sets, the pattern is removed, leaving a cavity in the shape of the desired object.
3. Core Making For hollow parts, cores made of sand and binder may be used. These cores are inserted into the mold to form internal features.
4. Pouring The next step involves melting the metal — typically iron, aluminum, or magnesium — and pouring it into the mold cavity. This is a critical stage where the temperature and timing are crucial to avoid defects in the final product.
5. Cooling After pouring, the molten metal is allowed to cool and solidify. The cooling time depends on the size and complexity of the casting.
sand casting definition
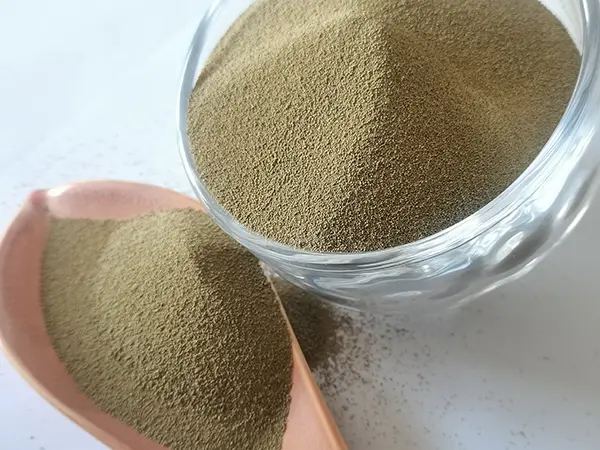
6. Mold Removal Once the metal has solidified, the mold is broken apart to retrieve the final casting. Any remaining sand is cleaned off to reveal the finished piece.
7. Finishing The final step may involve various finishing processes, such as grinding, machining, or polishing, to achieve the desired surface finish and dimensional accuracy.
Advantages of Sand Casting
Sand casting offers several advantages over other manufacturing processes
- Cost-Effective The materials used, particularly sand, are inexpensive, and the process does not require extensive tooling investments.
- Versatility Sand casting can accommodate a wide range of metals and alloys, as well as varying sizes and shapes.
- Complex Geometries This process is capable of producing complex shapes and intricate designs that would be difficult or impossible to achieve with other methods.
- Large Production Volumes Sand casting is suitable for both small-scale and large-scale production runs, making it ideal for various industries.
Applications of Sand Casting
Sand casting is utilized across many sectors, including automotive, aerospace, construction, and manufacturing. Common applications include engine blocks, cylinder heads, and valvetrain components in the automotive industry, as well as various structural components in buildings and machinery.
In conclusion, sand casting is a fundamental manufacturing process that combines simplicity with versatility, making it an enduring choice in metal fabrication. Its ability to produce intricate designs at a low cost ensures that it will remain a prominent method in the industry for years to come. Understanding the definition and intricacies of sand casting can provide valuable insights for engineers, designers, and manufacturers alike.
Post time:12월 . 30, 2024 21:34
Next:foundry sand for sale