Sand Casting of Cast Iron A Comprehensive Overview
Sand casting is one of the oldest and most widely used methods for metal casting, particularly in the production of cast iron components. This technique involves creating a mold from a mixture of sand, clay, and water to form a cavity that reflects the desired shape of the final product. Cast iron, known for its excellent castability, strength, and durability, is an ideal material for a variety of applications, making sand casting a popular choice across different industries.
The Sand Casting Process
The sand casting process begins with the creation of a pattern, typically made from wood, metal, or plastic, which replicates the desired object. This pattern is placed in a sand mixture, which is then compacted around it to create a mold. The sand mixture is typically composed of silica sand, a phenolic resin binder, and a catalyst, which helps improve the mold's strength and durability.
Once the mold halves are prepared, they are assembled and reinforced to ensure they can withstand the pouring of molten cast iron. After mixing the appropriate alloy of cast iron—often composed of iron, carbon, and silicon, with various trace elements for specific properties—the molten metal is poured into the cavity of the mold. This stage is critical; proper temperature management is essential to prevent defects such as shrinkage, porosity, or excessive oxidation.
After the molten metal has cooled and solidified, the mold is broken apart to reveal the cast part. The finishing stage involves cleaning the cast component, which may include processes like sandblasting or grinding to remove any remaining sand and excess material, ensuring a smooth surface finish.
Advantages of Sand Casting for Cast Iron
One of the primary advantages of sand casting is its versatility. It can produce complex shapes and sizes that might be difficult or costly to achieve through other manufacturing methods. This versatility is particularly beneficial when working with cast iron, as it allows engineers and designers to create intricate designs without significant alterations to existing tools or molds.
sand casting cast iron
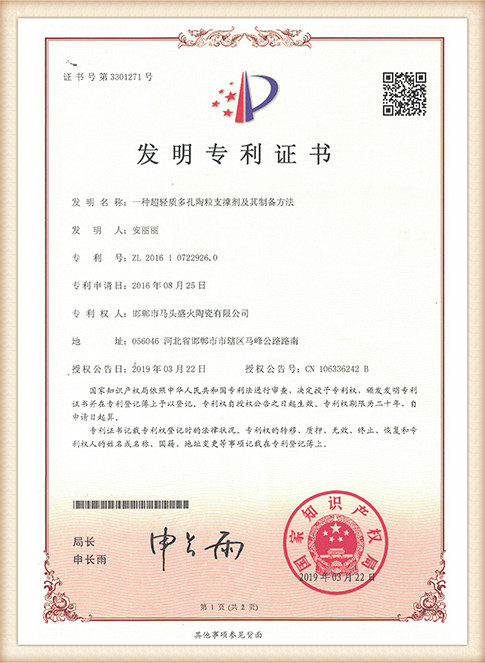
Another notable advantage of sand casting is the cost-effectiveness of the process. The materials required for sand molds are relatively inexpensive, and the process itself supports high production rates. Production runs can be scaled up or down based on demand without substantial equipment investment, making it an attractive option for both small and large production volumes.
Sand casting also offers excellent mechanical properties for cast iron products, such as high dimensional stability and good wear resistance. Depending on the alloy composition and the cooling rate after casting, engineers can tailor the cast iron's properties to meet specific requirements, whether that's increased hardness for wear applications or enhanced machinability for parts that require intricate final machining.
Limitations of Sand Casting
Despite its advantages, sand casting does come with some limitations. The surface finish of cast iron parts produced via sand casting may not be as smooth as those produced through die casting or investment casting methods, often requiring additional finishing processes. Furthermore, sand casting can be less efficient in producing high volumes of small, precise components due to its slower cycle times compared to other casting methods.
Additionally, the inherent porosity of cast iron produced by sand casting may affect the integrity of certain applications, especially in high-pressure environments. Engineers must assess the intended application carefully, considering factors like load, stress distribution, and environmental conditions to ensure the selected casting method aligns with operational requirements.
Conclusion
In conclusion, sand casting of cast iron remains a staple in manufacturing due to its versatility, cost-effectiveness, and ability to create complex shapes with desirable mechanical properties. As technology advances and more efficient sand casting techniques are developed, this method is expected to continue playing a crucial role in various industries, from automotive to heavy machinery. Understanding the nuances of the sand casting process and the characteristics of cast iron enables manufacturers to optimize production and performance, meeting the ever-evolving demands of modern engineering and design.
Post time:11월 . 20, 2024 20:23
Next:Мокрый песок 3D - печать