The Resin Sand Casting Process An Overview
Resin sand casting is an advanced method of metal casting that utilizes a mixture of resin and sand to create molds. This process has gained popularity in various industrial applications due to its ability to produce high-quality, intricate parts with excellent surface finishes. In this article, we will explore the resin sand casting process, its advantages, applications, and future developments.
Process Overview
1. Pattern Creation The first step in the resin sand casting process involves creating a pattern of the part to be cast. This pattern can be made from various materials, including metal, plastic, or wood, and is typically designed to be slightly larger than the final product to account for shrinkage during cooling.
2. Sand Preparation The next stage involves the preparation of the sand mixture. In resin sand casting, silica sand is combined with a liquid resin binder. The choice of resin is crucial, as it impacts the strength and flexibility of the final mold. The mixture is then cured using a hardener, which activates the resin and solidifies the sand.
3. Mold Creation Once the sand mixture is prepared, it is packed around the pattern within a molding box. The sand is compressed tightly to ensure a sturdy mold. After packing, the mold is heated to facilitate the curing process, solidifying the sand-resin mixture into a rigid form.
4. Core Making (if necessary) For parts requiring internal cavities or complex geometries, cores made from the same sand-resin mixture are created separately. Cores are inserted into the mold before pouring the liquid metal to form the inner shapes of the cast part.
5. Metal Pouring With the mold ready, molten metal is poured into the cavity created by the pattern and cores. The choice of metal can vary widely, including aluminum, iron, and bronze, depending on the required properties of the finished product.
6. Cooling and Solidification After the molten metal is poured, it is allowed to cool and solidify. The cooling time will vary based on the metal used and the thickness of the casting. Once sufficiently cooled, the mold is broken apart to reveal the cast part.
7. Finishing Operations The final stage involves cleaning and finishing the cast part. This may include processes such as grinding, sandblasting, or machining to achieve the required dimensions and surface quality.
resin sand casting process
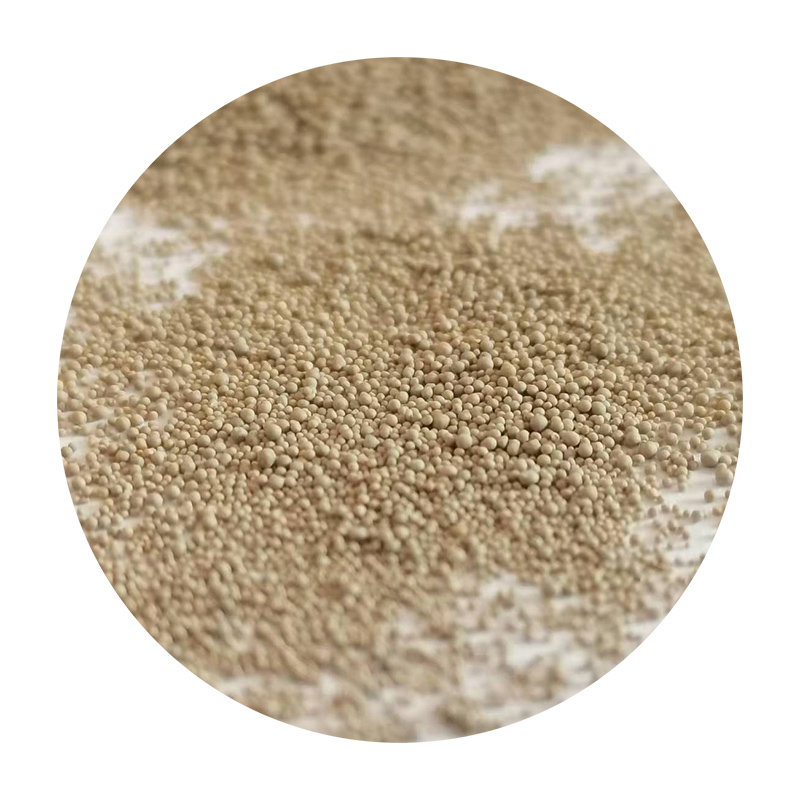
Advantages of Resin Sand Casting
Resin sand casting offers several advantages over traditional sand casting methods. One of the most significant benefits is the ability to produce detailed and complex shapes with excellent dimensional accuracy. The resin binder provides greater strength to the sand mold, allowing for sharper edges and finer details.
Another advantage is the surface finish quality. Parts produced using resin sand casting typically exhibit smoother surfaces, reducing the need for extensive post-processing. Additionally, the process allows for the rapid production of molds, making it suitable for prototyping and small production runs.
Applications
Resin sand casting is widely used in various industries, including automotive, aerospace, and machinery manufacturing. It is particularly well-suited for producing components such as engine blocks, transmission housings, and intricate machine parts. The ability to create complex geometries makes it an attractive option for industries requiring customized solutions.
Future Directions
The resin sand casting process continues to evolve, with advancements in materials and technologies enhancing its capabilities. Research is focused on developing new types of resins that are more environmentally friendly and have improved performance characteristics. Additionally, the integration of digital tools and simulation software is streamlining the design and production processes, allowing for greater efficiency and reduced lead times.
Innovations such as 3D printing are also beginning to influence the resin sand casting industry, enabling the creation of more intricate patterns and cores. As these technologies develop, resin sand casting is likely to become even more versatile and valuable in the manufacturing landscape.
Conclusion
In conclusion, the resin sand casting process presents a powerful method for producing high-quality metal parts with intricate designs. Its advantages in terms of accuracy, surface finish, and production speed make it a preferred choice in various industries. As technology progresses, the future of resin sand casting looks promising, with continual improvements expected to enhance its efficiency and sustainability in manufacturing.
Post time:12월 . 13, 2024 20:35
Next:sanding 3d print