The Importance of Resin Sand in Modern Foundry Practices
Resin sand, a crucial material in foundry operations, has gained significant attention in recent years due to its outstanding properties and versatile applications. This advanced sandcasting process has become a go-to choice for manufacturers aiming to produce high-quality metal castings with improved efficiency and lower production costs. In this article, we will delve into the composition, advantages, and applications of resin sand in the foundry industry.
Understanding Resin Sand
At its core, resin sand is a mixture of silica sand and a resin binder, typically phenolic resin or furan resin. The unique combination of these materials results in a sand that offers superior strength, excellent dimensional accuracy, and a smooth surface finish. Resin sand can be used in various casting processes, including shell molding, CO2 process, and no-bake process. The versatility of resin sand allows it to meet a wide range of casting needs, from automotive components to intricate art pieces.
Advantages of Resin Sand
1. High Strength One of the standout features of resin sand is its exceptional strength. The resin binder forms a strong bond with the silica sand, creating a durable mold that can withstand the pressures of molten metal pouring. This strength translates to reduced mold breakage during handling and allows for the casting of complex geometries.
2. Superior Surface Finish Resin sand molds often produce castings with a smoother surface compared to those made from traditional sand processes. This is particularly beneficial for industries that require components with minimal post-casting finishing work, such as the automotive and aerospace sectors. A smoother finish reduces the need for additional machining, saving both time and costs.
3. Dimensional Accuracy The precise characteristics of resin sand enable manufacturers to achieve tight tolerances in their castings. This level of accuracy is critical in high-performance applications where even minor deviations can lead to failure or suboptimal performance.
4. Reduced Environmental Impact Traditional foundry processes often involve high volumes of sand waste and require extensive reclamation efforts. With resin sand, the reduction in waste is significant, as the resin binds the sand particles together, minimizing the amount of sand lost during the casting process. Moreover, many modern resin systems are developed to be more environmentally friendly, aligning with global sustainability efforts.
resin sand
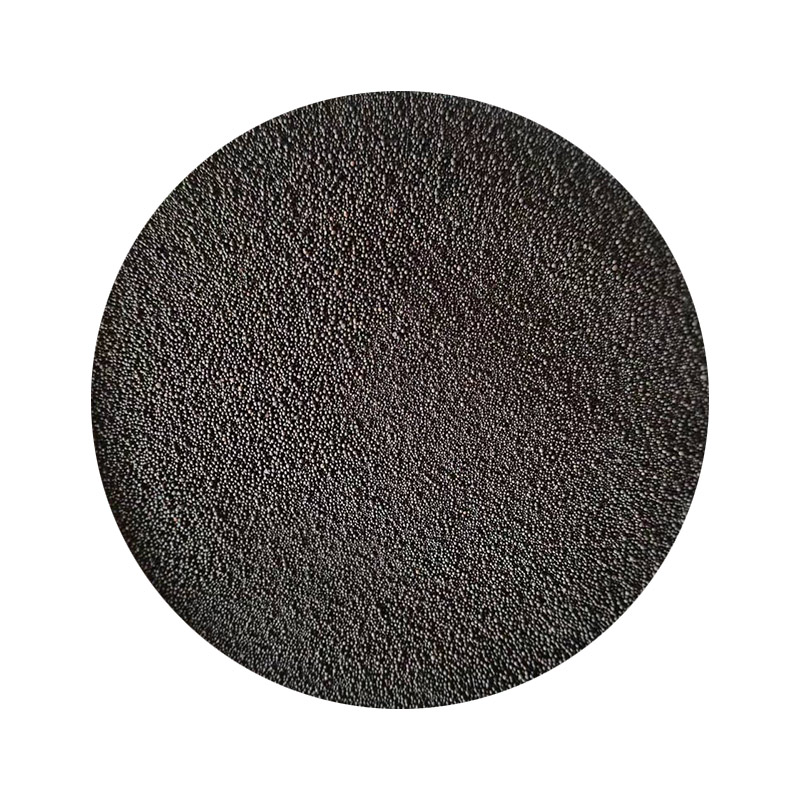
5. Versatile Curing Options Resin sand can cure at various rates, allowing for flexibility in production schedules. This adaptability is essential for foundries looking to optimize their workflow and meet customer demands quickly.
Applications of Resin Sand
The use of resin sand has proliferated across various industries due to its many advantages. Some of the most common applications include
- Automotive Industry Many automotive components, such as engine blocks and transmission housings, benefit from the high strength and surface finish of resin sand castings. This industry demands precision, and resin sand meets these rigorous requirements.
- Aerospace Components The aerospace industry requires castings that can endure extreme conditions. Resin sand provides the necessary strength and heat resistance for critical components, making it a preferred material for manufacturers.
- Artistic Castings Artists and sculptors often use resin sand for its ability to capture intricate details and produce aesthetically pleasing finishes. This application bridges the gap between industrial production and artistic expression.
Conclusion
In summary, resin sand has revolutionized the foundry industry by offering a superior alternative to traditional sandcasting methods. Its unique properties—high strength, excellent surface finish, and dimensional accuracy—make it an ideal choice for various applications across multiple industries. As foundries continue to innovate and seek ways to enhance their production processes, resin sand is poised to play an even larger role in the future of metal casting, ensuring that manufacturers can meet the challenges of today while paving the way for advancements tomorrow.
Post time:12월 . 11, 2024 02:46
Next:Understanding the Role of Metal Casting Sand in Manufacturing Processes