The Rise of Resin-Coated Sand Plants in the Foundry Industry
In recent years, the foundry industry has experienced a significant transformation, driven largely by advancements in technology and the growing demand for high-quality casting products. One of the most notable advancements has been the introduction of resin-coated sand (RCS) as a molding material. This innovative approach has led to the establishment of numerous resin-coated sand plants, which are increasingly becoming vital components of modern foundries.
Understanding Resin-Coated Sand
Resin-coated sand is a type of sand used in the manufacturing of metal castings. It consists of silica sand coated with a synthetic resin, typically phenolic or furan resin. This coating imparts several desirable properties to the sand, including improved strength, durability, and heat resistance. The result is a molding material that can withstand the high temperatures of molten metal while ensuring precision in the casting process. The use of resin-coated sand not only enhances the quality of the cast products but also reduces defects, that can lead to costly reworks and scrap.
The Process of Resin-Coating
The process of producing resin-coated sand involves several key steps. First, high-grade silica sand is selected and dried to remove moisture. Then, the sand is mixed with a predetermined amount of resin and a hardening agent, ensuring a homogeneous blend. The mixture is then cured at elevated temperatures, which allows the resin to chemically bond with the sand grains. The end product is a high-performance molding material that is tailored to meet the specific needs of various casting applications.
Advantages of Resin-Coated Sand Plants
The establishment of resin-coated sand plants offers several advantages for foundries. One of the primary benefits is the ability to produce customized sand mixtures that cater to unique casting requirements. This flexibility allows foundries to optimize their production processes, leading to increased efficiency and reduced waste.
Additionally, resin-coated sand significantly enhances the mechanical properties of mold cores. It provides excellent dimensional accuracy, reducing the need for extensive post-casting machining. This not only saves time and costs but also contributes to a greener manufacturing process by minimizing material usage and waste.
resin coated sand plant
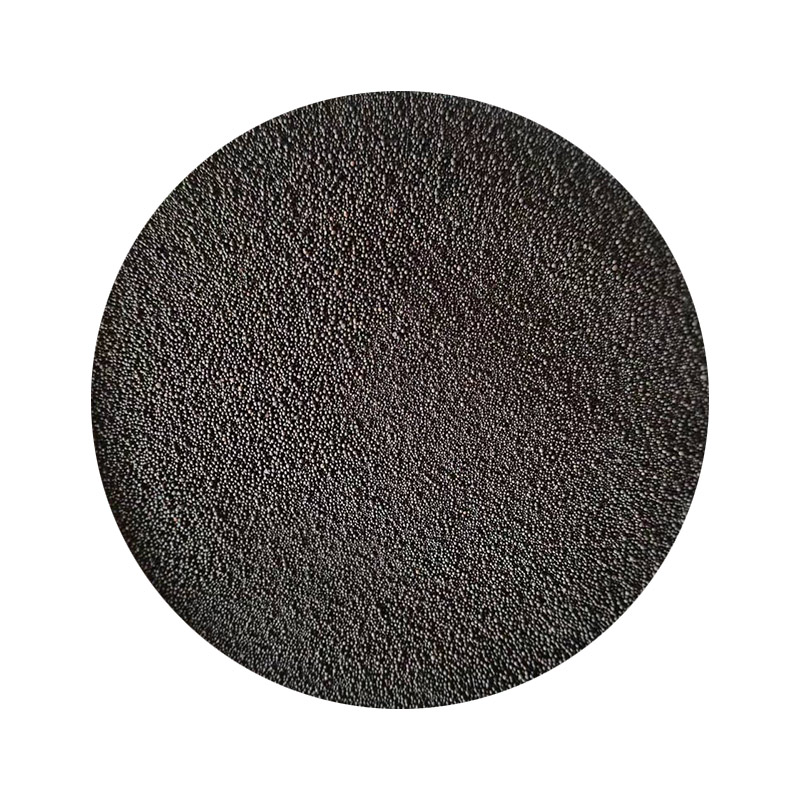
Furthermore, RCS exhibits superior thermal stability, allowing it to maintain its integrity during the casting process. This is particularly important in applications involving complex geometries or intricate designs, where traditional sand molding techniques may fall short.
Environmental Considerations
As the foundry industry faces increasing scrutiny over its environmental impact, resin-coated sand plants present a more sustainable alternative. The use of RCS allows for reduced emissions during the casting process, as the resin contributes to lower volatile organic compounds (VOCs) released compared to traditional materials. Additionally, many resin-coated sand plants are incorporating recycling technologies to reclaim used sand, further minimizing waste and promoting sustainability.
Challenges and Future Outlook
Despite the many benefits associated with resin-coated sand plants, there are challenges to consider. The initial investment in technology and equipment can be significant, which may deter some foundries from adopting this approach. Moreover, the sourcing of quality raw materials and the management of the resin curing process require skilled personnel and stringent quality control measures.
However, the overall outlook for resin-coated sand plants is positive. As the demand for high-quality castings continues to rise across various sectors, including automotive, aerospace, and energy, the need for advanced materials like resin-coated sand will only grow. Continuous research and development efforts are likely to yield even better formulations, further enhancing the properties of resin-coated sand and broadening its applications.
Conclusion
In conclusion, resin-coated sand plants are revolutionizing the foundry industry by providing enhanced materials that boost casting quality while promoting sustainability. As technology progresses and the demand for precision casting increases, these plants will play an essential role in the future of metal manufacturing. By embracing innovation, the foundry sector can meet the challenges of modern production while also contributing to environmental sustainability.
Post time:12월 . 26, 2024 01:31
Next:Exploring the Benefits and Techniques of Sand Casting for Cast Iron Products